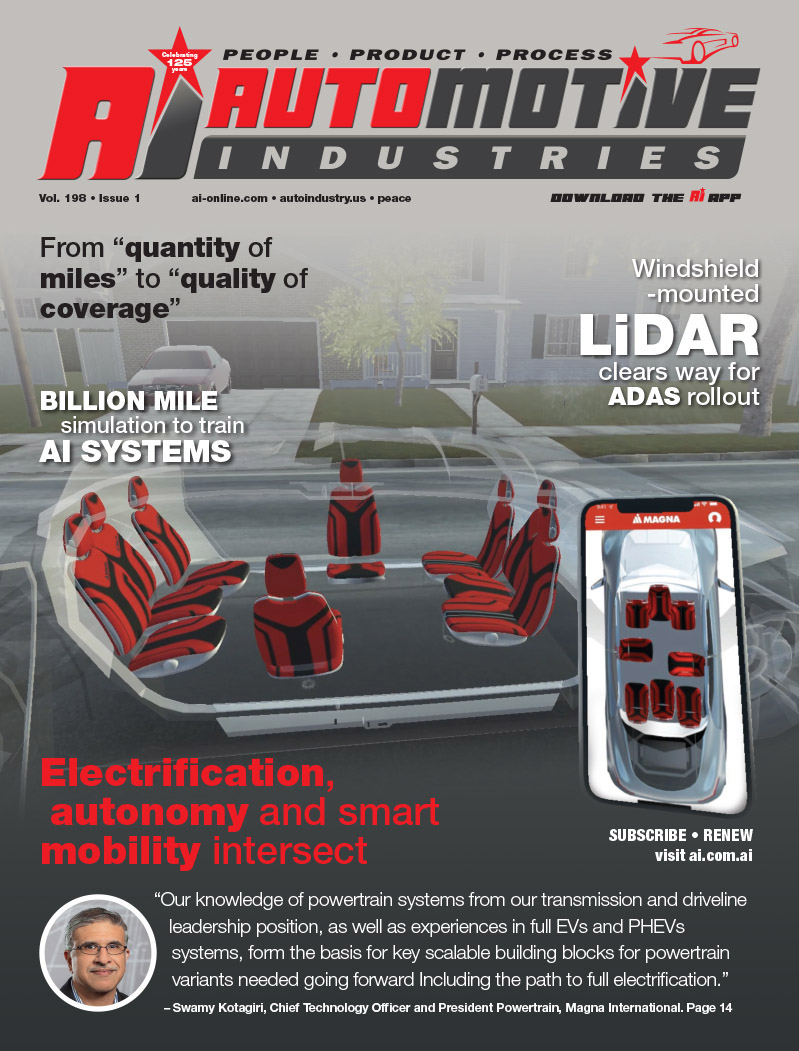
A new lightweight aluminum wheel manufacturing technology is helping OEMs reduce weight and make their vehicles “greener”.
The patented hybrid manufacturing process developed by Fundo Wheels of Norway uses friction stir welding (FSW). In 2007, the company won a US$50-million contract from Volvo to supply 600,000 aluminum wheels over three years using the process.
Fundo Wheels has its own research, development and design organization. Fundo is also teaming with one of its shareholder partners – Timminco – to assess, evaluate and develop magnesium wheels using FSW technology.
Fundo Wheels is 47% owned by Timminco. Timminco Ltd. is primarily owned by AMG, a publicly traded company incorporated in the Netherlands. AMG is a global leader in the production of highly engineered specialty metal products and advanced vacuum furnace systems.
Automotive Industries (AI) spoke to Hroar Carlsen, CEO, Fundo Wheels.
AI: How is your hybrid wheel technology different?
Carlsen: Our hybrid wheel represents a unique technical innovation for producing aluminum wheels. It is a two piece assembly concept, where rim and center disc are joined together using our patented FSW process. With FSW, we have the opportunity to achieve 25% weight reduction compared to cast aluminum wheels. Our hybrid wheel technology can combine the advantages of casting with the advantages of wrought (or forged) processing. A wrought aluminum alloy is used for our rim, where superior mechanical properties are of main importance. Casting can be used for the center wheel disc, where design freedom is a premium consideration. Using FSW, a weight reduction cavity is designed into the wheel disc periphery without use of cores or complex die technology. This is where much of the 25% reduction in weight, is achieved. The wheel disc can also be a forged design when weight reduction is paramount over aesthetic design.
AI: For what kind of automobiles is this technology targeted?
Carlsen: We target premium car producers needing weight savings to meet environmental and performance demands. Fundo strongly feels that environmental issues have become much more important for the premium car makers, and introducing the Hybrid wheel technology into this market now, is very appropriate. Presently, the technology is addressing wheels with rim diameters 19” and above, and automobiles where reducing unsprung and rotating weight is of greater value. Since wheels represent static and rotating masses, wheel weight reduction has a bigger effect (about 30%) on fuel consumption and CO2 emission than static vehicle weight in general. Additionally, since wheels contribute to unsprung weight, reducing their mass improves vehicle road handling characteristics and passenger comfort.
AI: Tell us about your FSW manufacturing process and the benefits of this process.
Carlsen: The FSW process is a solid state joining process with no melting of material. It is a plastic deformation process where the two materials to be welded are stirred together. This implies low heat input and no use of filler material, resulting in very good mechanical properties in the heat-affected zone. The FSW process was developed by The Welding Institute in the UK in the early 90’s, and is now utilized in several industries including the aerospace industry.
In the OEM wheel markets, there have been several concepts for lower weight aluminum wheels. However, we are confident that our concept is the best technical solution in the market combining significant weight reduction with reasonable production cost. Fundo has a worldwide patent on using the process for wheel manufacturing.
AI: How would you describe your quality standards? Tell us about the customer awards Fundo Wheels has won.
Carlsen: Our quality standards are reflected by our certification to the ISO-9001, QS-9000 and ISO-TS. We also have the environmental certification ISO-14001. In the Ford group, we are certificated to Q1 supplier. During our 30th year as supplier to some of the world’s most demanding customers, we have achieved several customer awards, from Saab, Audi and Ford/Volvo.
AI: What kind of opportunities do you think Fundo Wheels has in the BRIC (Brazil, India, China, Russia) countries?
Carlsen: Our present market strategy is focused in the premium car segment, As FSW technology expands in application and process maturity , we expect to become more attractive to emerging vehicle production markets.
AI: Why is Fundo examining magnesium wheels and particulate reinforced aluminum metal matrix composite (Al-MMC) center sections for possible future wheel products?
Carlsen: The siren song of magnesium as the lightest weight structural alloy for automotive applications is the main reason for this wheel product exploration. There is an existing niche business in performance motor sports for such a product. Fundo has a ready-made partner for magnesium wheel development in Timminco, one of its owners. Timminco specializes in developing and producing magnesium alloy ingot and extrusions. The team plans to bring this product opportunity to the attention of the USAMP activity.
In the longer term, Timminco/Fundo is pursuing more robust magnesium alloy solutions that fit the requirements of future road-going lightweight and green vehicle wheels. Reducing vehicle unsprung corner weight (static and dynamic) is becoming a more and more valuable activity.
Particulate reinforcement of aluminum alloys adds significant fatigue value to the parent aluminum alloy without sacrificing parent alloy strength. In metallurgical terms, it creates a fatigue limit for the alloy that the parent alloy does not otherwise exhibit. Fatigue is a key performance characteristic that must be considered in the design of any wheel center.
Such Al-MMC materials can be cast using the same processes with which aluminum alloys are cast, and at increasingly competitive costs. As important, the Fundo FSW process technology may be able to intimately join such materials to aluminum alloy rims. If the joining metallurgy is demonstrated to be sufficiently robust, Fundo’s engineering CAD tools will be able to optimize center section designs using Al-MMC metallurgical advantages to further decrease wheel weight.
More Stories
Some Ways How Motorists End Up in Collisions at U-Turns
Maximise Margins with Proven PPF Tactics
Finding the Car Boot Release Button – Tips and Tricks