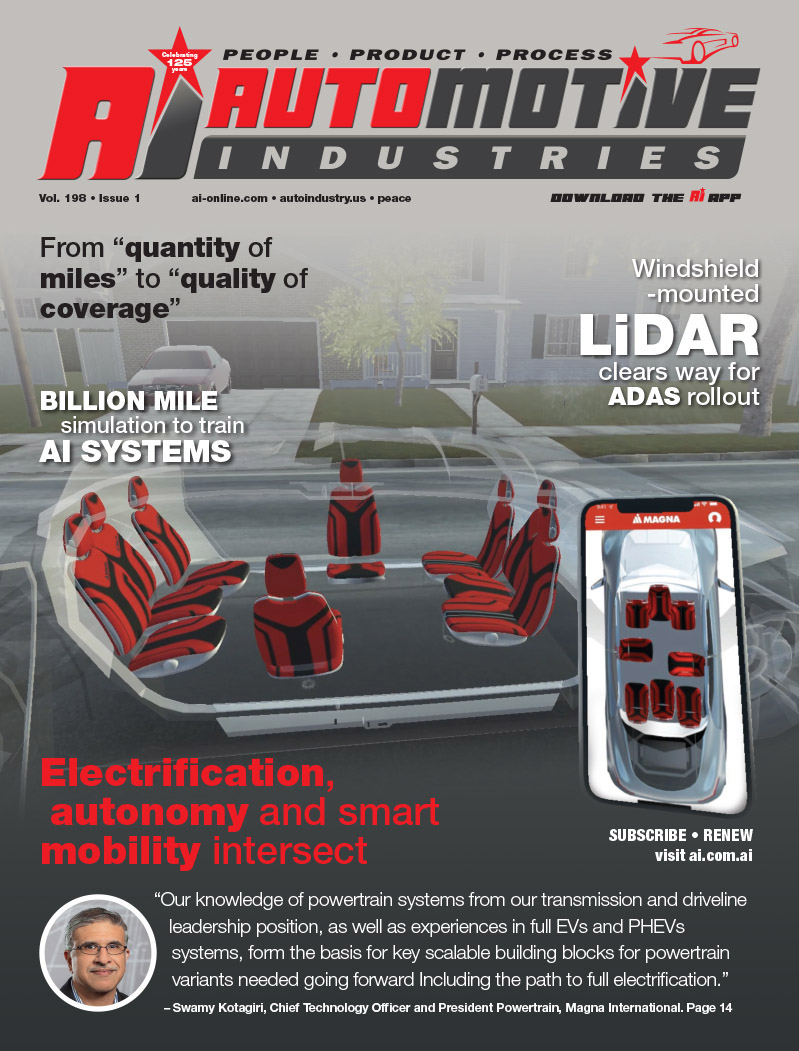
For years, inventor and industrialist Lennart Stridsberg has been pushing his hybrid vehicle concept with little enthusiasm from the auto industry. But that is all set to change. Today, green concerns are major challenges for auto companies – how to find alternative fuelled vehicles, cut emissions and improve fuel efficiency.
Most hybrid concepts claim a fuel reduction of some 25 to 30%. Simulations for the Strigear indicate reductions of 50 to 60 %. It would probably be easier to make the industry interested if we claimed 45%! Fuel reductions of 60% are hard to believe, says Stridsberg. However, imagine a conventional car with real life engine, body and tires but with a perfect transmission and perfect battery between the tires and the engine. One example of such a purely theoretical vehicle would save 73% of the fuel compared to the same car with a real life AT transmission, and a Strigear in the same car using real life electric motors and real life batteries would same 61% of the fuel. This means that the Strigear would still use 44% more fuel than the imaginary perfect transmission vehicle.
The Strigear engine uses two electric motors, an internal combustion engine and an actuator controlled gear box. The gear box could be an AMT, a DCT or a Zero shift. Stridsberg’s team suggests a Servo Synchronized Manual Transmission (SSMT) that uses the two electric motors in the Strigear basic system to control the gear shift and to do this without any sync rings or other hardware. With this method, gear shifts are performed in some 0.03 to 0.07 seconds. This makes the gear shift unnoticeable for passengers. The Strigear concept claims almost dramatically higher acceleration than competing system even when using almost identical components.
Stridsberg says that its hardware design eliminates the losses inherent in the electrically variable transmissions based on two motors and one or more planetary gear systems. The gear box permits the optimizing algorithm to select between, for example, six different topologies by selecting a suitable gear. The patented optimization algorithm gives better component utilization and the electric motor on the engine flywheel makes it possible to switch the thermal engine on and off whenever required and to add extra load to get a load point with high fuel efficiency.
When politicians start implementing regulations that can affect the CO2 emissions, there are not many alternatives to efficient hybrids using internal combustion engines. Using alternative fuels could be part of the solution, but that is far from evident. There is no enormous amount of biomass available, so biomass based fuels will not solve more than a fraction of the whole problem. The IEA estimates that bio fuels could cover between 4 to 8 per cent of the fuels used in the road transport sector in 2030.
Plug in hybrids or pure electric vehicles will be fed from the national electric grid. For the coming 15 – 20 years, there will not be enough wind, solar or wave power to replace all the coal fired power plants. This means that the marginal electric power will come from coal fired power plants. A plug in hybrid in electric mode or an electric vehicle will therefore emit more than twice as much CO2 as a Strigear vehicle of the same size. They will also have CO2 emissions that are higher than the EU regulations.
Automotive Industries spoke to inventor and industrialist Lennart Stridsberg.
AI: How would you today rate the automotive industry’s reactions to your hybrid concepts?
Initially, no one believed in the fuel reductions claimed. This has changed, now some 50% of the experts we meet accept our data before checking our simulations, and so far no one has challenged them after having checked our simulations.
AI: Please tell us about the challenges facing an engine designer when it comes to engine speed versus vehicle speed.
Almost all hybrid experts we have met are familiar with the idea that a hybrid engine speed must be independent of the vehicle speed to obtain low fuel consumption. I challenge that idea. The average efficiency of the engines in Strigear systems are typically 94 to 96 % of its peak engine efficiency, so there is only some 4 to 6% to gain by a continuous variable transmission. From a system point of view, there is far less to gain. If the vehicle requires 5 kW and the optimal engine efficiency point is at 30kW, it would not be a good idea to run the engine at 30kW and store the marginal 25kW in the battery. In such a case the losses in the generator, electronics and battery would be so large that it would be more efficient to run the ICE at say 15kW to get lower electrical losses. But in that case the ICE efficiency would be lower than optimal.
AI: What goes into the process of designing a hybrid engine concept taking into account these two factors – ie vehicle and engine speeds?
The hardware required to arrange a continuos variable transmission is far less efficient than the classic manual type gearbox. The gain in engine average efficiency, some single percent, is lost several times over by the lower transfer efficiency of the continuos variable transmission. Therefore, we are convinced that a stepwise gear box is the superior solution.
AI: How come you can obtain such a high average efficiency of the engine?
It is due to two things. First, we have an electric motor dedicated the engine. In fact, it is the fly-wheel of the engine. This motor can be dedicated to ensure that the engine is switched on and off when required, and can also add or subtract torque to ensure an efficient operating point. Second, we have a control algorithm that utilizes the possibilities given by the hardware in an optimal manner.
More Stories
Some Ways How Motorists End Up in Collisions at U-Turns
Maximise Margins with Proven PPF Tactics
Finding the Car Boot Release Button – Tips and Tricks