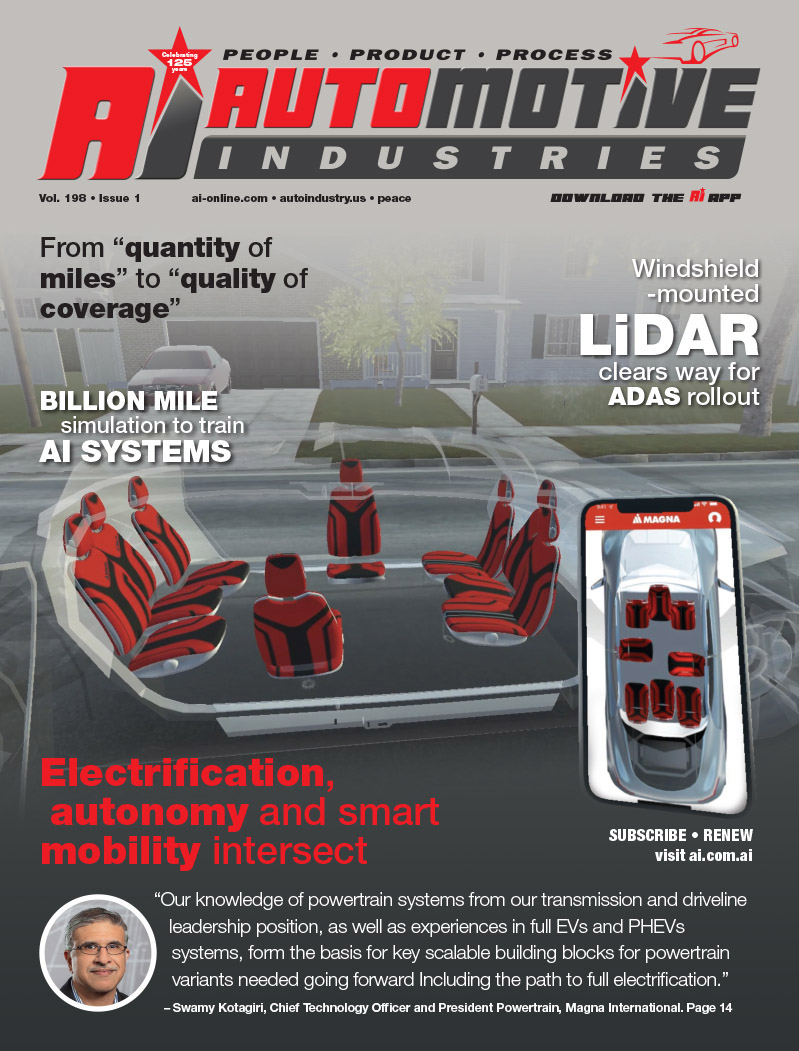
The all-new 2008 Chrysler Town & Country and Dodge Grand Caravan minivans will be built at Chrysler Group’s Windsor (Ontario) Assembly Plant and St. Louis South Assembly Plant located in Fenton, Mo.
“These are very important products for the Chrysler Group as we remain committed to the minivan market and maintain our leadership position,” said Frank Ewasyshyn, Executive Vice President — Manufacturing, Chrysler Group. “Our focus on flexible manufacturing and new investments, adding state-of-the art technology to plant operations, will help us ensure we can meet those demands and build almost anything, anywhere, with improving speed and quality.” The ability to produce several vehicles under the same roof allows the Chrysler Group to save millions of investment dollars and bring a vehicle to market faster, with even higher quality levels and minimal downtime.
Windsor Assembly Plant
With a $532 million investment, Windsor Assembly will be capable of building two different vehicle platforms and piloting a third simultaneously on the same production line. The ability to build multiple products on the same line enables the company to build and test prototype vehicles much earlier in the launch phase. Because the same tooling and same processes are employed (rather than a simulated line), the company can train operators and resolve manufacturing issues much sooner. Quality improvements are another benefit.
The key to the flexible manufacturing process at Windsor Assembly is the order in which the body is assembled using a unique under-body pallet system in the body shop. The same flexible pallet system also has been used at the company’s Sterling Heights Assembly Plant in Michigan where the Chrysler Sebring Sedan, Sebring Convertible and Dodge Avenger are manufactured, as well as the Toledo North Assembly Plant in Ohio, where the Jeep(R) Liberty and Dodge Nitro are produced. This means that the same production system may be used to build sedans, convertibles, minivans, sport-utility vehicles and crossovers.
This flexible manufacturing system was first used in the launch of the then all-new 2001 Chrysler Town & Country and Dodge Caravan series of minivans in the summer of 2000. Windsor Assembly ramped up to maximum production of about 25,000 units of the all-new model in just 25 days, compared with a 110- day industry average for a major change-over of this type.
The Windsor facility underwent a major change-over with extensive upgrades to accommodate the new minivans’ production requirements and Smart Manufacturing methods. The enhanced processes and installation of new technology also will benefit future product launches and additional product variants due to the greater levels of flexibility.
The Windsor Assembly Plant’s body shop’s under-body pallet system, an enabler of flexibility, gives the plant the ability to maintain production of the 2007 model year vehicles concurrent with change-over and pilot production for the new 2008 model year minivans. The system carries the under-body components for minivans and the Chrysler Pacifica on the same line, eliminating the need for separate conveyor lines for each product.
New, flexible robotic lines were added to weld the new minivan’s body sides and under-body sub-assemblies, which will accommodate future models and product variants at reduced investment levels. Once assembled, more than 350 points on the minivan’s body frame will be checked automatically for weld precision and dimensional quality.
A $246 million investment to Windsor Assembly has produced a new, state- of-the-art paint facility capable of accommodating the dimensions of at least 11 different body styles. Operational in the third quarter of 2007, the Paint Shop was modified to accommodate new robotic applications of two types of sound dampener technology, both of which contribute to the minivan’s refined driving experience and the new levels of quietness while riding inside.
In the Trim, Chassis and Final area, new processes also were developed to install safety features.
Recent agreements with UAW-represented employees also have cleared the way for new operating principles. The pacts are designed to foster greater creativity and innovation on the plant floor. They allow for work teams, self-designed work stations, a framework for flexible job classifications and extensive employee training. These elements will provide a better, safer work environment and further support assembly line operators.
Originally built in 1928, the Windsor Assembly Plant is currently the largest of the Chrysler Group’s 14 assembly plants at 4.01 million square feet. In 2003, Windsor Assembly became one of the first Chrysler Group plants to implement the flexible manufacturing strategy. This year marks the plant’s 24th anniversary of minivan production and the 14th anniversary of three shifts of operation. The plant employs 4,800 people.
St. Louis South Assembly Plant
In 2005, DaimlerChrysler announced it would invest as much as $1 billion in its two St. Louis-area manufacturing facilities. The manufacturing plants, located in Fenton, Mo., are home to the Chrysler Town & Country and Dodge Grand Caravan minivans (South) and Dodge Ram (1500 and 2500) Standard and Quad Cab Pickup (North). Part of this significant capital investment provides St. Louis South with the capability to manufacture multiple types of vehicles on one line.
St. Louis South will be the third Chrysler Group assembly plant to implement a fully robotic body shop, giving it the ability to automatically adjust to build multiple models within cycle time. Equipment, facility and process changes began in 2006 as the plants continue to build Chrysler and Dodge minivans. The investment also is expected to reduce new-model change- over downtime.
The 2.64-million-square-foot St. Louis South Plant was constructed in 1959. The plant employs 3,200 people.
The 2008 Dodge Grand Caravan and Chrysler Town & Country will be in dealerships in the United States in the fall of 2007.
More Stories
Sika – where battery storage technology for EVs, wind and solar meet
Driving Change with Circular Aluminum: Hydro’s Role in the Automotive Future
Transforming automotive paint shops with BASF Coatings’ GLASS Tool: A leap towards efficiency and sustainability