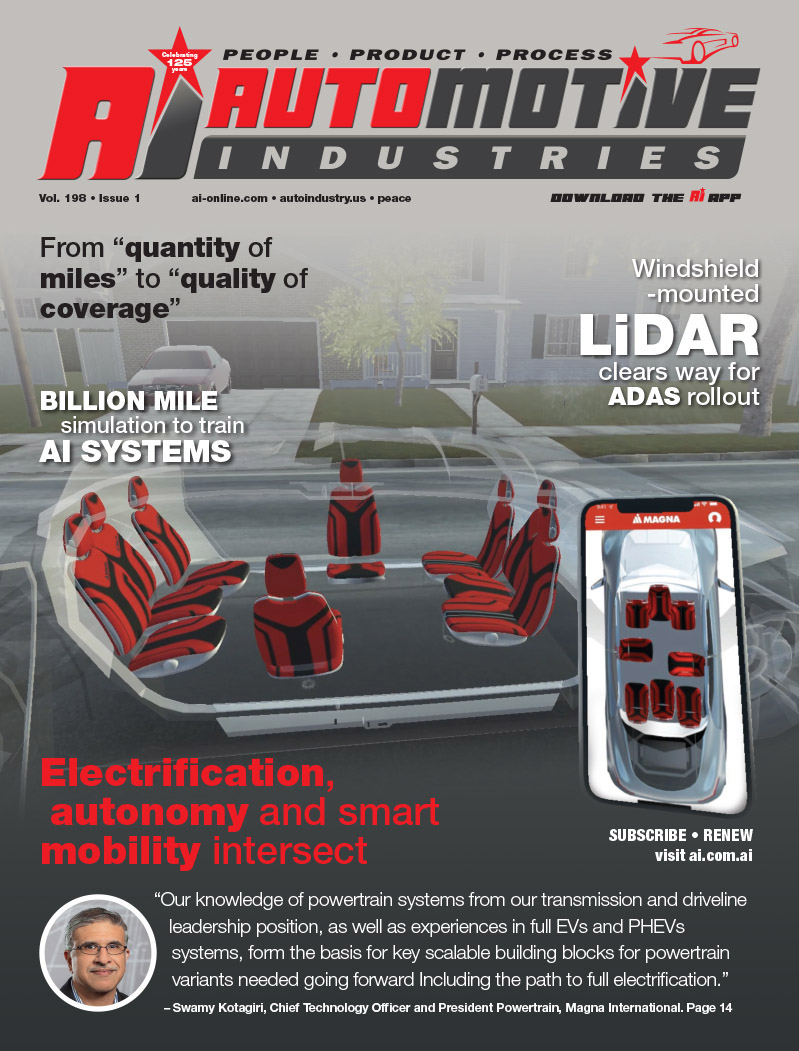
The Six-Sigma approach has become a cornerstone throughout the automotive industry, and in-process measurement is a requirement for an efficient implementation. Unfortunately, the trend towards 24/7/365 operation of production lines means the traditional night-shift measurements are no longer possible. We discuss this dilemma with Øyvind Røtvold, CEO of Metronor – a measurement systems company with most of the world’s automotive manufacturers on the customer list.
More and more top executives acknowledge the need for Six-Sigma environments for continuous improvement initiatives to boost profitability and the quality of services and products. These activities address the need for understanding “cause and effect†relationships and to pro-actively optimize product quality and reduce the risk of unstable processes.
Six-sigma engineers utilize so-called “DMAIC†phase models; Define the process; Measure key quality characteristics; Analyze process capability; Improve and correct the causes of deviation; Control actions.
At the same time, one of the most profitable strategies for cost-cutting is to build as many vehicles out of a single production line as possible. This minimises per-unit investments, and an increasing number of plants are therefore operating 24/7/365.
This creates a major challenge: How to retain a solid measurement component in the DMAIC model even with 24/7/365 production line operation and essentially no production line down-time.
Øyvind Røtvold of Metronor is quite familiar with this dilemma: “We have seen a marked shift in the requirements of our customers since Metronor entered the market some 15 years ago. The traditional scenario was to run in-process geometry assurance activities during the night-shift and on week-ends. The emphasis was therefore on systems that could support geometry assurance programs that systematically measured all aspects the complex tooling installations – geometry to CAD, repeatability, interaction with robots etc. These activities were typically run by highly skilled specialists with time available to conduct in-depth investigative measurements when issues were detected.
Now, industry increasingly requires systems that will also function well inside the current operations. No longer is a full shift available – measurements must take place during breaks of as little as 15 to 30 minutes – during meal breaks or shift changes. Traditional portable measurement systems have either been very large and heavy, have required pedestals or have involved aiming of two separate sensors – there is no time for any of this any more.
For Metronor this has meant that we have designed a new type of system to support these seemingly conflicting requirements. Our new light-weight SoloTwin system sets up in seconds and works effectively also in very tight spaces. By going in close, we achieve high accuracy even on large tools while avoiding the time penalty of conventional dual-camera based systems.â€
But why are measurements of the production tooling and process required in the first place? Røtvold explains: “All experience from our customers indicate that the DMAIC measurement component must include measurement of the production tooling and its capabilities for truly efficient “cause-and-effect†analysis. In-line and end-of-line inspection systems detect product drift and process instability, but cannot determine precisely where in the line it is occurring or what misalignment is causing it. As soon as drifts are detected, corrections need to be carried out without impacting production flow. Hence there is a need for metrology solutions that offers accurate and extremely fast measurement operation.â€
Metronor is one of the world’s leading manufacturers of measuring systems. Used mainly by the aerospace and automotive industries, Metronor’s systems are currently being used in more than 200 installations across the globe. Some of the automotive customers include Audi, BMW, DaimlerChrysler, Ford, GM, Honda, Hyundai, Nissan, Opel, PSA, SAAB, Toyota, Volkswagen and Volvo.
Volvo was Metronor’s original development partner, and the emphasis was on developing portable measurement systems that combined large volume capabilities with ease of use, high accuracy, excellent mobility and low cost. The SOLO system set a benchmark in the portable measurement market offering instant set-up, extreme ease-of-use and a lower cost than any comparable large-volume measurement system.
The new SoloTwin solution is based on the SOLO system by integrating a second camera into a single unit so that the SoloTwin offers a much wider (70 degree) field of view, making it possible to get very close to the tooling to be measured. Bringing the measurement system in closer to the tooling improves accuracy, makes positioning easier by reducing the space required and allows the operator to quickly capture all critical points accurately and efficiently.
In the real world, SoloTwin has been shown to set-up; tie-in to the coordinate system; perform measurements of all critical features of the assembly tools; verify measurement data relative CAD nominal; correct alignment issues of the tool, and get out of the station without interfering with the production cycle – in less than 20 minutes.
Røtvold is very pleased with industry feed-back: “The new SoloTwin is seen to set a new benchmark in meeting current industry requirements – uniquely combining point-and-shoot set-up and fast data acquisition with large volume versatility, ease-of-use, accuracy and extreme mobility. The market seems to like the price, too.â€
Metronor was founded in Oslo, Norway, in 1988. The first systems were delivered to SAAB and Volvo in 1991 and the first models of the current product range were introduced in 2004. Røtvold emphasises the special relationship Metronor has had with the QA and manufacturing engineering community of the automotive industry: â€A key factor in Metronor getting where we are today, is the focus we have always had on interaction with our customers. We do not see ourselves merely supplying measurement machines – we provide metrology solutions that provide our customers with critical information about the improvement potential of their processes. All our product development takes place with industry interaction. We were among the very first to compare measurements real-time to 3D CAD models on the shop-floor – since using 3D CAD cut cost and ensured data integrity. We worked with DaimlerChrysler to define best practices that included formal verification of tool repeatability for every jig in the production line. We worked with Volvo to develop the SwitchMode capability to quickly measure prototypes on the shop-floor while relating all measurements to the main body coordinate definitions. SoloTwin is just the latest example of this tradition – Metronor technology has continuously evolved based on the immensely valuable input from local champions in all our customer organization.â€
Today, Metronor has offices in Europe, North America and Asia. Local markets are served by distributors – mostly full-service representatives that handle sales, support and customer training – but Metronor also maintain a staff of application engineers at all offices that support both the local sales channels and end customers directly when needed.
“We are happy to be experiencing growth in all markets, but the strongest growth right now is in North America and Asia. In particular the Chinese and Korean markets are important for us, which is why we have an office in Beijing with our own staff supporting our many Asian distributors. The Asian automotive industry is catching up at an incredible speed, and we often find them more open to continuous improvement than customers in more mature markets.â€
Based on the core technology developed for the industrial measurement systems, Metronor has recently expanded into military systems. The Harmolign product line is a dedicated system for aligning the navigation-, targeting- and weapons systems of military aircraft in the field – developed under contract from BAE Systems for their Hawk and this summer selected also for the Helmet Mounted Sight system for the Swedish SAAB JAS-39 Gripen fighter. “Harmolign provides Metronor with a new business area†says Røtvold “but is also excellent news for our automotive customers. The need to certify Harmolign to the extreme requirements for ruggedness and survivability of e.g. MIL-STD-810 has taught us as a company a number of lessons that we can apply to make our industrial systems even more bullet-proof as all the key components of the industrial systems – such as the cameras and the intelligent LED targets – are also used in the military systems. While Harmolign takes us into a new market, it stays true to our core technology and contributes to continuous improvement also of our industrial systems.â€
More Stories
New generation of Donaldson compressed air dryer systems offers enhanced reliability and energy efficiency
Flexible Magna Manufacturing Solutions: The Key to Success in the Automotive Industry
Celanese helping OEMs and Tiers to overcome EV challenges