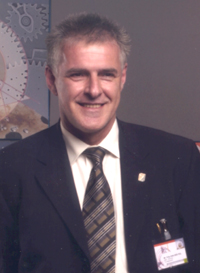
The trend of continually updating production processes is having an impact on the design of tools. Innovation is now the key for optimizing tool concepts, tool life and production speed, according to Dutch company SMS Stamp Tool Technologies.
Founded in 1958, the company’s products are used by some of the world’s best known companies in the automotive, electronic, semi-conductor, consumer article, medical and photo industries. SMS is a specialist in the CAD/CAM manufacturing of high performance stamping tools. SMS won the European Engineering Award and the Micron d’Or for the development of ceramic in lead-frame tools in 2002.
A sister company of SMS, Worldwide Tooling Service (WTS) specializes in CAD/CAM manufacturing of precise tool- and mould components, in tool maintenance and overhaul. SMS’s facilities in the Netherlands is TUV certified NEN-EN ISO 9001.
Most of SMS’ modularly-designed tools are carbide. However, ceramics are proving ideal in a wide range high volume tools. Ceramic components in lead-frame tools offer a four- to five fold tool life improvement and a significant reduction of maintenance costs and production loss, according to the company. Ceramic is also an ideal material in tools for stamping copper and non-ferro materials.
Automotive Industries spoke to Frits Vanderpol, president and chief executive officer of SMS Stamp Tool Technologies.
AI: How much of your business is automotive?
Vanderpol: About 30% of our turnover is directly linked to the automotive industry. Indirect around 50%, if we consider that our products which we deliver to several other types of industries, as connectors and semiconductors, will be delivered to automotive clients also.
AI: What are some of your automotive products?
Vanderpol: Stamped parts produced with fine-blanking dies are solely used in automotive industries for car parts as steering/gear mechanism, seats, safety belts, etc. SMS designs, manufacture and deliver production equipment in accordance to customer product requirements. The product design comes from the customer, the production equipment design from SMS or in co-operation. The SMS R&D facility is involved in optimising existing or developing new stamping and process techniques and materials.
AI: Are your customers mainly European?
Vanderpol: Our main base is Europe with a focus on automotive for 30% and other types of industries as connector, consumer, medical, health and semiconductor nicely divided.
Globally we export about 5% to the USA and the Far East. The main focus is still Europe, with a percentage of 45% outside The Netherlands and 55% locally.
AI: Do you have any plans to open new SMS facilities in other countries?
Vanderpol: We have start up plans to increase our activities as a first tier supplier in Europe. The home base of SMS stays in The Netherlands, but we are focussing ourselves in starting up joint ventures or subsidiaries globally. This will be effective within a couple of years.
AI: What are some of the new technologies SMS is working on?
Vanderpol: Plans, which we have started last year, are based on a “three-stage rocket†principle.
In co-operation with customers, we are developing new stamping technologies for three specific types of industries, which should results in faster production speeds and lower operational costs.
Based on our experience in supplying turnkey product life cycle solutions for metal plastic combinations, we are also developing new types of materials and processing techniques in this particular field.
From our operational side, the daily focus is on a strictly lean manufacturing-machining basis. In this way we are able to supply customers with logistic advantages, leading to a reduced stock and fast deliveries of components in according to a supermarket principle.
More Stories
Some Ways How Motorists End Up in Collisions at U-Turns
Maximise Margins with Proven PPF Tactics
Finding the Car Boot Release Button – Tips and Tricks