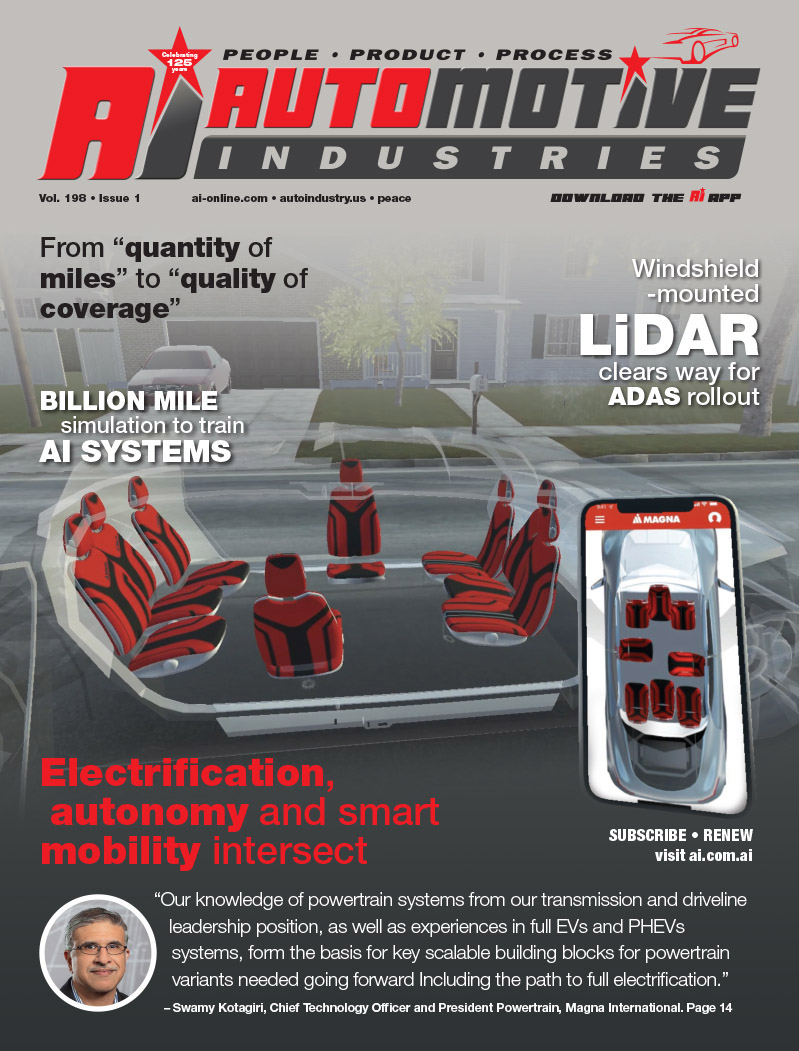
Swedish aluminum major Sapa AB’s automotive division, Sapa Automotive was founded in 1994 as a dedicated automotive sales organization. With over forty years experience, Sapa AB is the world’s third-largest manufacturer of aluminium profiles. Nearly 26 per cent of the 18 billion Swedish kronor (US$ 2,6 billion) revenues of Sapa AB, comes from its transportation and automotive segment. Sapa Automotive’s clients consist of car and truck manufacturers from around the world – plus system suppliers to the automotive industry.
Sapa Automotive has at its disposal its parent company, Sapa AB’s production facilities. Sapa has nearly forty aluminium-extrusion presses at plants throughout the world in countries like Sweden, Denmark, Poland, England, Germany, the Netherlands, Belgium, France, Portugal, USA, China, Lithuania and Slovakia. Plus the company has sales offices in Austria, Estonia, Finland, Italy, Canada, Latvia, Lebanon, Norway, Switzerland, Slovakia, Spain, South Korea, Czech Republic and Turkey.
According to Sapa Automotive, it works with the automotive industry by acting as consulting engineers, marrying automotive and aluminum extrusion technologies. “In every major automotive manufacturing country, dedicated Sapa personnel are on hand to ensure you Sapa’s total expertise and experience in extrusion technology for the automotive industry,†says a statement on the company website.
According to Sapa Automotive, the percentage of aluminum in vehicles is increasing at the expense of heavier materials since cutting down weight is a priority for most manufacturers. Another reason for the growth of aluminum is that vehicles have a greater number of cooling components for their air-conditioning systems.
According to the company, for some automotive customers, Sapa Automotive takes on a complete roof rail assignment. These roof rails are developed, manufactured, surface treated, assembled, packaged and distributed by us. They arrive at our customers’ assembly lines as finished subassemblies. Plus, Sapa Automotive makes extrusion-based seating parts that offer unique design possibilities. For example, the company developed an innovative serration tool that allows cost-effective manufacturing of high-precision seat slides. Structural seat parts such as back-rests can also be made from joined extrusions with a unique Friction Stir Welding technology giving increased strength, better straightness, closer tolerances and improved repeatability compared to conventional fusion-welding joints.
Sapa Automotive also offers aluminum extrusions that can be used for various engine parts such as fuel rails and fuel distribution parts, engine mounts and brackets, even valve covers and charge-air pipes. The company also manufactures frames and sub-frames from closed-section profiles that are hydro-formed three-dimensionally into the required shape. To these, cross-members and brackets can be welded to form a complete assembly. Radiator mounts, dashboard braces, impact beams and bumpers are some examples of extruded structural parts. Trim around door openings, behind door handles, on dash boards and in various places throughout the interior are perfect examples of high-finished trim parts that benefit from the durability of aluminum extrusions, says a statement from Sapa Automotive.
Sapa Automotive prides itself in offering state-of-the art aluminum extrusions as far as design and manufacturing go. Sapa Automotive works closely with Sapa extrusion factories all over Europe and Asia to provide cost-effective delivery. The company has also invested in efforts to develop extrusion dies – the company has so far made more thatn 150,000 extrusion dies making its die makers some of the most experienced in the world.
Another focus for Sapa Automotive is the surface treatment of its aluminum extrusions for both increased functionality as well as for design purposes. The company offers three surface treatments – anodizing, lacquering and Decoral. Anodising is one of the most common surface treatments that is used to give a permanent new appearance as well as to make aluminum corrosion resistant. Apart from natural anodizing, Sapa also does the treatment using oxide layer impregnated with color pigments. The company offers powder coating and also Decoral which is a variation of powder coating that produced patterned surfaces.
“Sapa Automotive is never content to leave you with a raw extruded profile. Our aim is to add value by functioning as your total manufacturing partner. Regardless of whether an order calls for a limited number of parts with a high degree of manual work, a fully automated assembly line or anything in between, we will add value to the aluminum profile through bending, machining, surface treatment, and assembly. Sapa Automotive offers all available fabrication methods. We will refine and develop aluminium extrusions into complete, ready-to-assemble components and sub-systems for our customers,†says a statement on the company website.
Sapa Automotive’s ultimate aim is to be a single source contract manufacturer of automotive components. The company says it has the ability to assemble and deliver finished products or complete sub-systems anywhere in the world. “Our key words are minimalism and multi-functionality. We’ll make sure that our profiles are the right thickness and have the proper radiuses for the task, no more, no less. And second, we strive to investigate if there is a better solution available, studying any proposed component in its working environment to see if we can integrate more functions into a single, cost-effective component,†says the company.
For example, Sapa Automotive supplied fabricated aluminum profiles for airbag deflectors for Autoliv. The deflector houses the gas generator which spreads the gas when the car’s airbag is activated. The deflector is mounted in a casing that contains all the airbag’s components and there are profiles holding the tube in place.
Automotive Industries spoke to Laurent Andrzejewski, market co-ordinator, Sapa Automotive.
AI: What percentage of a car is made up of aluminum and how much do you expect this to grow by over the next few years?
A recent study from the European Aluminum Association (EAA) shows the amount of aluminum used in new European cars has risen from 50 kg in 1990 to 132 kg in 2005 and is predicted to grow by another 25 kg by 2010.
In 2005 two million tones of aluminum components were put on European roads in new passenger cars.
Another study ordered by the North American Aluminium association and made by Ducker Worldwide states that the growth in Europe has been of 5% per year for the last six years and predicts that it will continue to growth at the same path for the years. The equivalent for North America is 3,7% and 3% for Japan.
Europe is also leader when it comes to innovative solutions for brackets as well as for body and chassis components mainly with the aim of improving safety and performance.
AI: What kind of technology is Sapa Automotive working on to improve the usage of aluminum in vehicles?
Sapa Automotive is continuously working with the latest technologies in order to keep up with the tough competition. We can mention for instance the innovative friction stir welding technology to join extrusions. This welding method uses a rotary dowel to join pieces with minimal influence on the material’s properties compared to traditional welding. Extruded aluminum car back-rests are manufactured this way, as well as floor, roof and side panels for train cars which shows that the method is approved for applications with very high mechanical requirements. The potential of this joining method in the automotive industry has yet to be fully explored.
Another top of the line technology is hydroforming which consists in shaping an extrusion three-dimensionally inside of a die with help of internal water pressure.
Complex shapes are possible with this method, which allows the precise tailoring of the cross section and three-dimensional bending of profiles with extremely tight tolerances and very good repeatability. The method has great possibilities for structural members and pipe components with varying cross sections. This makes it possible for instance to increase the section of a part, and therefore its moment of inertia, in the places where a parts is most solicited, thus optimizing its shape without adding superfluous extra weight.
When it comes to more conventional fabrication method such as punching, Sapa is working in close collaboration with expert tool makers. By combining our know-how, our engineers are able to push the limits of what is possible to achieve in term of durability, tolerances, repeatability and high process speed when fabricating into hard alloys with thick wall-thickness in narrow spaces. This is very useful for applications such as seat rails or complex engine brackets and makes us competitive even for large volume parts.
Additionally, extruded components can be designed with many integrated smart functions that ease assembly and decrease downstream production costs. Screw ports, tracks for bolt heads and nuts, snap fit joints, hinges are examples of what can be designed in a profile without extra cost in order to enhance its functionality.
AI: How do you market the material to automotive companies and what has their reaction been?
We market aluminum as the “green metal†full of potential for the automotive industry. Its unique material characteristics such as high strength-by-weight ratio, non-corrosive properties, recycle ability, ability to be shaped into complex forms and its natural shine are heavy arguments for the use of this light metal. And last but not least, the extended use of aluminum in cars is a strong premise in the struggle to reduce emissions. Studies prove that 1 kg aluminum can replace 1,8kg steel while fulfilling the same requirement and even getting a slightly better result. For every 100kg of aluminum used in a medium size car (C-segment), the CO2 emissions will decrease with 9gr/km. Now that the European Union has agreed on common targets for emissions of maximum 130gr/km (120 gr/km for the cars themselves and 10gr/km to be gained from other sources such as more efficient fuels, better road asphalts, etc.) at the horizon 2010, this will be a strong argument for car makers to think aluminum instead of steel.
AI: Are there any low-weight competitors to aluminum that can be used for vehicles? If so, what are they and how does aluminum compare to them in terms of durability and functionality?
Of course, there are alternative low-weight competitors to aluminum extruded parts. We can mention heavy duty polymers, magnesium, extra and ultra high strength steel or die cast aluminum.
Polymers are very formable, resistant and you can get nearly any shape you want, but they are oil based products which means that they are price sensitive when crude oil prices are record high, they are more polluting both when being produced or recycled, and they do not reach the mechanical strength that can be reached by aluminum.
Magnesium is lighter and stronger than aluminum, but also much more expensive. Magnesium parts are complex to fabricate because of the explosive magnesium dust and chips when in contact with some liquids. Casting dies are expensive and the size of the parts has a limited scope. Magnesium fabrication shops are must therefore be very specialized with a negative impact on the part price.
Steel producers have done a tremendous work in developing extra and ultra high strength steel. It can be used with very small thicknesses, thus a reduce weight, but formability is still limited and price quite high. Though assembly methods such as robot spot welding can be done using standard equipment in place at most car OEM. Steel parts are also corrosion sensitive and need surface treatments that alter the recycle ability of the fabricated parts.
Die cast aluminum parts are used a lot all around the car and especially on powertrains, steering and transmission. Their main disadvantage is the die investment cost, especially for large parts, and porosity and homogeneity problems which makes it necessary to oversize the parts and thus the weight, and makes then unsuitable for any decorative or high finish application, or when brittleness is an issue. When it comes to recycle ability, die cast aluminum can only be re-melted into other cast alloys, and cannot be used for refined alloys such as for extrusion billets.
AI: What is Sapa Automotive’s game-plan going to be over the next couple of years to boost its contribution to Sapa AB’s revenues from its current turnover?
Good can be better, better can be best! Sapa Automotive will continue to strive after perfection with a very competent staff eager for greater challenges. We will focus on developing our customer base within car and truck manufacturers and system suppliers. We will continue to strengthen our organization for offering better service, to develop our partnership with our suppliers located in low cost countries in order to offer cost effective solutions to our customers. We will focus on high level of automation for high volume parts to assure high capacity and quality.
We will continue to be pro-active in continuously improving existing processes and parts and reducing waste. In the long run, we even intend to reengineer our fabrication shops into competence centers for even better reactivity and technical support. We will develop our website www.sapaautomotive.com with exiting customer cases and smart design ideas. Finally, we will emphasize on the virtues of the “green metal†that is aluminum and the benefits that every environmentally attentive car and truck manufacturers can get by choosing high added valued extruded components all over the vehicle.
More Stories
Some Ways How Motorists End Up in Collisions at U-Turns
Maximise Margins with Proven PPF Tactics
Finding the Car Boot Release Button – Tips and Tricks