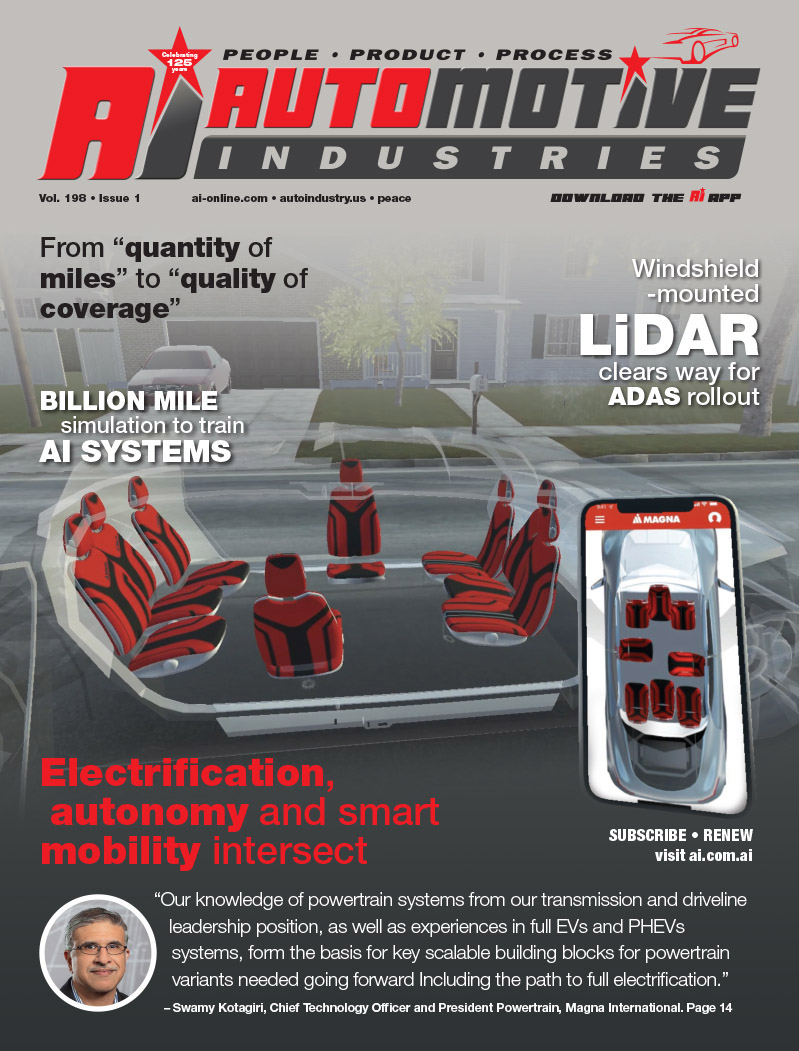
Faced with challenges of extreme weather and terrain conditions, shock, vibration and thermal stress, the automotive industry utilizes Spiralock thread form in numerous applications. Automotive Industries asked James P. Gillis, Executive Vice President and Chief Operating Officer at Spiralock Corporation about the company’s latest technology breakthroughs.
Gillis: Spiralock’s mission is to develop innovative products to help our customers solve problematic fastened joint applications. Our application engineers work with our customers to identify challenging applications while in the field, which translate into wonderful opportunities for our R&D staff in Michigan.
This year, the company is launching a new V-band Clamp Nut for use in high temperature exhaust applications. The nut is designed to eliminate galling due to the long run down on the male thread, in addition to providing unlimited reuse while maintaining its locking feature. The nut also has extra thread length and load distribution for improved fatigue performance.
In addition, we are developing our manufacturing capability for thin walled nuts, which provide weight savings as well as better balancing associated with the self centering aspect of Spiralock threads and closely held perpendicularity of the nuts. These nuts are used in turbo charger applications as well as auto racing and aerospace applications where weight reduction is important.
Additionally, Spiralock has a new style of wire thread insert that eliminates the installation tang, called the Spiralock Drive Notch TM Insert, which should be available later this year. Spiralock wire thread inserts are used by diesel and gas engine manufacturers and aerospace companies for soft materials such as aluminum or magnesium to provide the threaded joint with added strength, secure locking and multiple reusability.
Furthermore, we have many projects under development to solve specific threaded joint applications, including a nut that will free spin onto a bolt and have prevailing torque to prevent it from coming off, a locking fastener for soft joints (a gasket), and a tamper proof nut with special exterior geometry.
AI: What percentage of your revenues comes from the automotive sector and by how much do you see this sector growing?
Gillis: The automotive sector represents 20% of our overall business. We anticipate this sector to have the largest percentage growth over the next five years, partly due to our efforts in Asia, Europe and South America.
AI: In which geographical areas of the globe has Spiralock grown fastest?
Gillis: Our most recent expansions into Brazil and China have resulted in significant business in a short period of time, averaging growth of 90% or more each of the past four years. Our more established business units (US and Western Europe) have experienced growth in the 15 to 30% range over that same period. We anticipate another increase of 23 to 27% in global revenues in 2006 with Europe seeing the highest overall growth in the range of 40 to 45%.
AI: What are your plans for further expansion both at home and globally? Any new manufacturing plants?
Gillis: Presently, we are planning on opening a new operation in mainland Europe shortly after the first of the year to better support our customer base in Western and Eastern Europe.
We are also investigating the possibility of opening operations in Japan, Thailand and India similar to our European operation to support our customers in those areas.
Spiralock in action
The secret to Spiralock’s thread form is a 30 degree – wedge – ramp cut at the root of the female thread. The wedge ramp allows the male fastener to spin freely relative to the female thread and eliminate galling. When clamp load is applied, the crests of the standard male thread form are drawn tightly against the wedge ramp, eliminating radial clearances and therefore, any transverse motion that causes loosening under vibration.
Once clamp load is applied, it establishes a continuous spiral line of contact along the entire length of thread engagement, which more evenly distributes the loads of the threaded joint throughout all the engaged threads.
More Stories
5 Conclusions One Can Make by Analyzing Car Accident Statistics
Why You Should Invest in Regular Car Washes to Protect Your Investment
Workers’ Compensation for Repetitive Stress Injuries