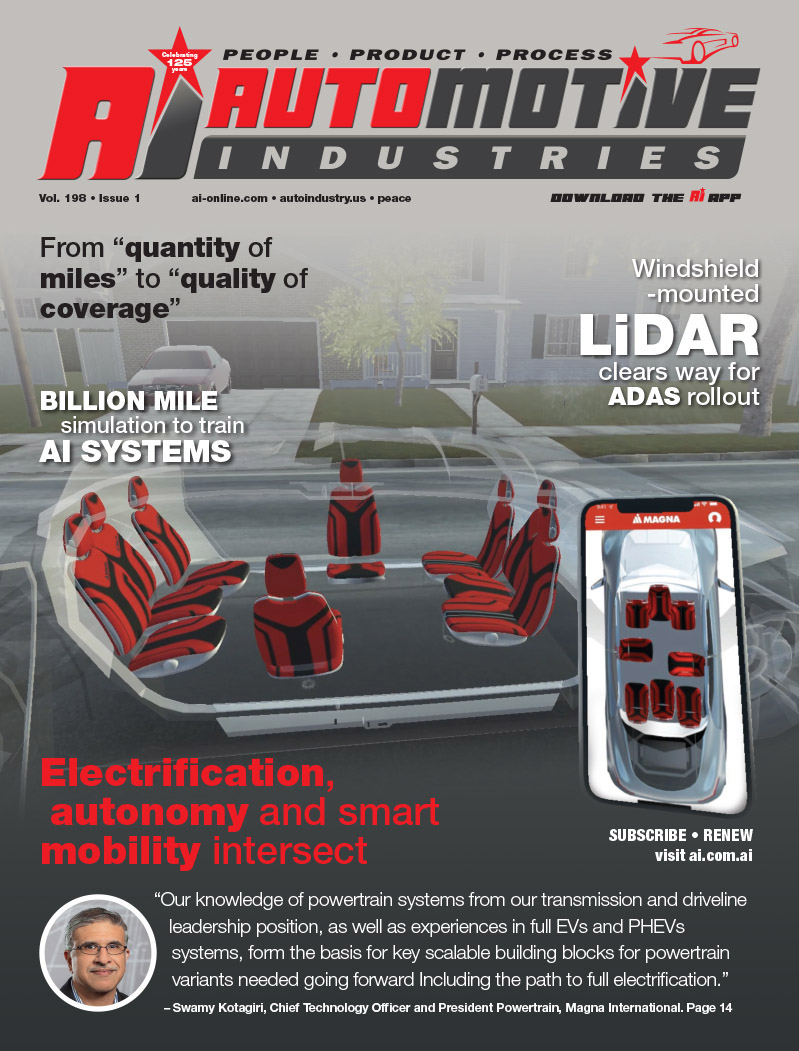
Hydro Aluminium Precision Tubing Tønder a.s is part of Hydro Aluminium’s automotive division. The company is one of the top three aluminium producers worldwide. Automotive Purchasing News spoke to Michael Schäfer, key account responsible for Audi in the Precision Tubing organization. of Hydro Aluminium. Hydro Aluminium is Audi’s preferred independent supplier of cylinder heads and crash management components.
Automotive Purchasing News (APN): What kind of technology and experience has gone into the development of new applications such as the fin cooler, the precision drawn tube and the fuel cooler?
Schäfer: Hydro Aluminium has invested about DKK 100 million (EUR 13.5 million) in a new extrusion press. The new press is being used for high-volume products of the type micro MPE profiles. By doubling the production capacity, the company can cover the entire European market of this product type, where the company already has a market share of over 60%. Typical applications of the lightweight profile are condensers and evaporators for air conditioning equipment, heaters, intercoolers for diesel engines, and also radiators.
Our products, which also include the PA12 coated Hycot® tube, can be found in almost all modern European cars.
APN: How do you go about developing new components in partnership with OEM’s?
Schäfer: We mainly focus on heat transfer and liquid line applications where we see our core competence. If we spot a market opportunity that lies within our competence range and within our manufacturing capabilities, we start a development project in a very systematic way with clearly defined targets. It is our goal to develop a product that can reach a broad customer base. This can be quite difficult, since the requirements from the OEM’s typically differ a lot. The Hydro fuel cooler is a typical example of our targeted development, where we started with a broad specification and we ended up with a customised product fulfilling the particular requirements of Audi, for example.
APN: How close did you have to work with Audi on the design of the fuel lines?
Schäfer: Audi is bending and bundling the fuel lines for the B and C platform in Ingolstadt and Neckarsulm. We supply the straight lines directly to Audi’s in-house bending centre.
In most cases we supply our fuel lines in straight lengths to the system suppliers, who assemble the complete fuel bundle. In the case of Audi, however, the supply chain is shortened. Audi’s fuel system engineers do the design of the fuel lines and provide the specifications to us. We review the drawings and make recommendations with regard to the manufacturability of the design or propose alternative designs.
APN: What are the benefits of using the new aluminium fuel cooler?
Schäfer: When we developed the new fuel cooler, our target was to use proven manufacturing technology. The fuel cooler is extruded and machined in one piece and the advantages of this production method is that the finished product is completely without brazing or joints that might cause leaks or aggressive corrosion attacks due to residual surface flux. The relatively low pressure drop is also an important feature of our cooler. Since the injection pump can only supply a limited pressure for pumping the surplus fuel back to the tank, it is important that the fuel cooler device does not create excessive backpressure. We optimised the internal geometry of the cooling profile in order to achieve the best compromise between the heat transfer and the pressure loss.
One important innovation going into the fuel cooler product is the aluminium alloy itself.
Hydro has developed a long-life alloy, which is six to eight times more resistant against corrosion attack than the conventional extrusion alloys. The major advantage of the Hydro fuel cooler concept is that it is easy to integrate into given spaces without requiring expensive manufacturing tools and with a minimum of reengineering required. Usually the available space on the car underbody is restricted, so the designer is looking for an easy-to-adapt solution that does not require costly changes in the underbody panels. In order to adopt the cooler to the existing fixation points, we use specially designed plastic brackets. The brackets can be produced in injection moulded PA66 plastic, which is a well-known material that can withstand the harsh environment beneath the car.
APN: OEM’s are always looking for reduced development costs and a competitive product with higher quality. How do you fit into that category?
Schäfer: In general we do not ask our OEM customers to participate in the development costs, since it is our primary goal to sell the product to a broad customer group in order to achieve high production volumes.
APN: What are the new uses in the automotive industry for the types of product you are developing – for example, Hycot Fin-Cooler for power steering applications?
Schäfer: Current developments in the automotive industry are striving for higher performance of the functional components. This trend often results in additional heat energy that has to be dissipated to the environment, as in the case for the high-pressure diesel injection pumps or the hydraulic power steering circuit. Aluminium is the natural choice for heat transfer applications, combining light weight and strength.
APN: How far are you prepared to go in supporting customers with projects?
Schäfer: We try to differentiate ourselves from the competition by providing the best technical service in the market. We have a team of application engineers who are experienced in dedicated application areas. Since we deliver our product usually as semi-fabricates to our customers, the role of the application engineer is to advise the customers how to use our products in the best possible way in terms of process and application technology.
We have made investments into test benches such as a wind tunnel in order to be able to provide measurement data to our customers. The technical service is part of our product offering and is highly appreciated by the customers. We also have the possibility to consult our metallurgical experts who are based in the Hydro R&D centre in Karmøj , Norway. Here we have all necessary equipment to go into the depth of metallurgical analysis. Further we have established a centralised A&D centre called Alunova with bases in Denmark and Florida, USA, providing new product concepts to the business units within the global precision tubing market. Hydro Alunova generates ideas that derive from its core competencies and the global network of partners and worldwide plants placed in Europe, North America, South America and Asia.
APN: Where do you see Hydro Aluminium technology being used in the future?
Schäfer: Apart from the classical applications for aluminium tubes such as water cooling, air-conditioning and power steering, we see a strong growth for the use of aluminium in the fuel line market. The main driver is the governmental requirement to reduce the total hydrocarbon emission of the fuel system, which requires new ways of connecting the tube, a subject we are currently working on. We also closely follow the development towards the new Co2 driven air-conditioning systems, which will require new standards for aluminium tubes due to the higher operating pressure and temperature than in today’s conventional R134 driven air conditioning systems. A third application is high pressure lines, which has mainly been the domain of steel tubes. In this regard, connection technology is the main issue, since the change to aluminium requires changes in the current connection standards. However, we are convinced that the ongoing attempts to save more weight and stricter corrosion requirements will be in favour of aluminium tubes.
More Stories
5 Conclusions One Can Make by Analyzing Car Accident Statistics
Why You Should Invest in Regular Car Washes to Protect Your Investment
Workers’ Compensation for Repetitive Stress Injuries