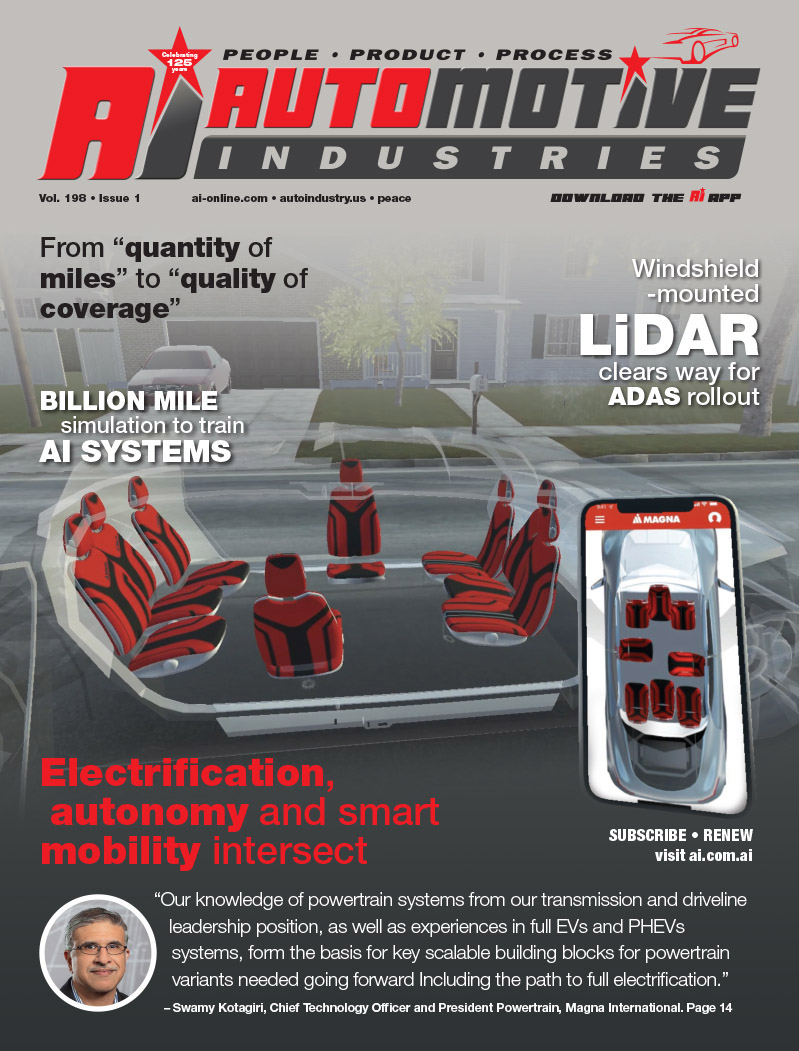
Seeber-Roechling Automotive is one of the worlds leading manufacturers of systems and components made of polymer materials and natural fibre plastic composites on and around the engine as well as for the underbody and interior of modern vehicles. Automotive Purchasing News spoke to Seeber president Georg Duffner.
Automotive Purchasing News (APN): What are the trends in the use of thermoplastics and in particular new materials and processes in terms of lower part weight and increasing overall functionality?
Duffner: Experts estimate that without the increasing use of plastics, the average car weight would have risen by 25 % instead of 10 % from 1960 to 2000. And the situation today is almost the same. For instance, without a hybrid frontend carrier instead of a steel version an actual Audi A8 would weigh at least 5 kg more. Besides the strong need for weight reduction, there are new fields of application in which plastics and electronics form an ideal combination such as controllable air duct systems. These systems mark off a new proposal for intelligent air flow towards the radiator.
APN: What is the real potential of polymers in under the hood technology?
Duffner: Particularly in view of the increasingly complex air flow that may result from the engine design, the polymeric applications play an increasingly important role. For instance, blow moulded tubes that are bent in several directions have hard and soft sections being ejected in sequence. This allows engineers to adjust the tube to any free space within the engine compartment. Another possible field of action is the integration of electronic components such as level indicators, sensors, pumps or a scald protection function into containers.
Furthermore, the improvements of sound protection that have taken place continually.
APN: What are the challenges to Seeber-R?ing Automotive in relation to optimising aerodynamics and sound insulation?
Duffner: Since around the early 1980s, components for engine and body undershields made of glass mat reinforced thermoplastics (GMT) have been manufactured using compression moulding. (GMT is an approximately 3 mm to 4 mm thick semi-finished product made of a glass mat impregnated with PP.) The next development goal was to avoid the production stage of manufacturing a semi-finished product and to produce the composite of glass fibres and PP directly before the compression stage at the component manufacturer?s site. This was called the direct long-fibre reinforced thermoplastics (abbreviated to D-LFT) process.
Over the past few years now the surface area of the body undershields has continuously increased, mainly for aerodynamic but also for acoustic reasons. In our opinion the optimisation of wall-thickness of components made in GMT or D-LFT technology reached a level up to which a substantial progress can no more be achieved. As a result, Seeber-R?ing Automotive has developed sandwich components with a very light core and stiff cover films.
These have first been introduced to the market on the BMW 5 and 6 series.
APN: How does Seeber-R?ing Automotive contribute to the effort of the OEM?s to create the ultimate impression of comfort and safety in the field of vehicle interiors?
Duffner: The passenger compartment has become a living room on four wheels with a high degree of functionality. When Seeber-R?ing Automotive got the order to develop and manufacture the rear centre console of the Maybach, we were confronted with the enormous complexity of this module which comprises a large multitude of materials, functions and technologies. We believe that our contribution mainly is to offer fascinating solutions for the integration of functions. The central armrest for the Smart ForFour is a good example of intelligent and innovative product design. By turning the upside of the armrest 180? down or tilting the armrest 180? to the rear both the front and the fond passengers can use one and the same cupholder function integrated in the backside of the armrest. Another aspect of our business is that there are numerous injection moulded and blow moulded parts in the interior as well; sometimes invisible such as air ducts for the climatisation, sometimes visible such as several painted parts we supply to BMW and Land Rover. In fact it is a trend that the quality of surfaces gains importance from year to year.
APN: What are the developments in door panels ? seen from the point of view of the OEM?
Duffner: Our latest door panel projects for VW and Audi (VW Touran, Audi A3 and VW Golf in China) required a notable amount of investment into production technology and building construction. In the case of the VW Touran we were first to apply the MuCell? technology (Microcellular Foam Technology, developed by scientists of the Massachusetts Institute of Technology in Cambridge, USA) for the backmoulding of balustrades and inserts of the door panels on the European market. Also the laser cutting technology was introduced as a new manufacturing technology.
APN: What are the trends in the use of natural fibre moulding materials?
Duffner: Under our brand names: seeBIOzell (woodfibre reinforced material), seeBIOflex (a blend of natural and synthetic fibres), as well as seeBIOform, seeBIOpur and seeBIOdur (natural fibres with EP, PU and AC ? matrix) we develop, produce and deliver door panel carriers, back panels, hat shelves or even mats to the vehicle manufacturers and various interior system suppliers. We also investigate the possibility of using natural fibres during injection moulding which we call the seeBIOinject process. Besides the environmental aspects the main driver for the success of natural fibres certainly is the general need for weight reduction. In the case of door panel carriers we could achieve improvements of around 40% compared to injection moulded parts (ABS), at even better impact behaviour and at lower emission levels. Furthermore, certain natural fibres are available at comparatively stable prices.
APN: How does Seeber-Roechling Automotive work with OEMs to develop new applications ? including the knowledge and expertise in your competence centres?
Duffner: Knowing that we have a high share of component business in our product portfolio, it is absolutely crucial for success that we know as much as possible about every part we produce. This is not only for the purpose of optimising material usage, structure or process stability but also in order to reduce development time. The latter also enables us to meet challenging time schedules of our customers. In addition we gather experience in system design and become able to develop complete modules. For our customer there is a real benefit when he can work together with the same contact person over a long time and get immediate answers to his problems because of the short distances within the competence centres.
APN: Please expand on your integration of development, manufacturing and logistics ? what does this mean in practice to the OEM?
Duffner: Seeber-R?ing Automotive, a 100% subsidiary of the R?ing group, Mannheim is organised as a group of companies acting in a way in which our customers can find elements of centralisation and decentralisation. Central functions like the development work done at competence centres and our key accounting management include a worldwide approach and responsibility. On the other hand production, logistics and quality issues can be handled better when the distance between the customer and Seeber is rather small. The challenges of globalisation as well as the necessity of quick reactions to market changes require a high amount of flexibility which we believe we offer our customers worldwide.
More Stories
Shaping the future of the automotive industry at Automechanika Shanghai 2024 with the most fringe programme events and speakers yet
Some Ways How Motorists End Up in Collisions at U-Turns
Maximise Margins with Proven PPF Tactics