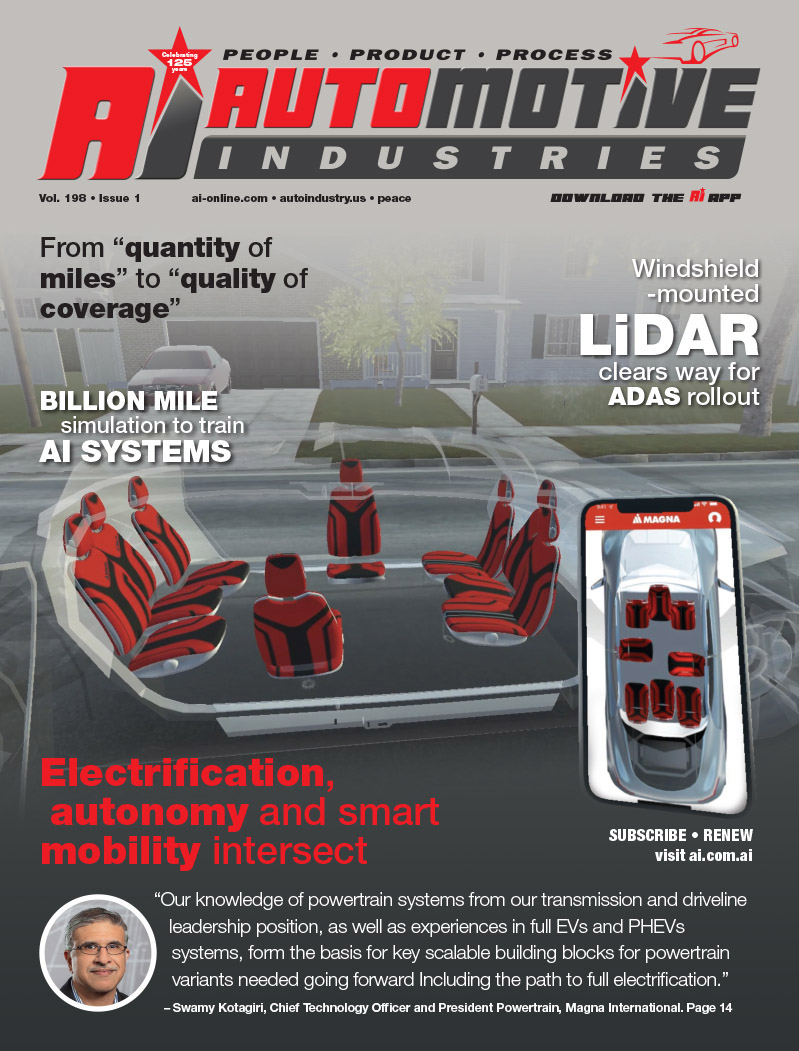
Thomas Kraus of Rasmussen discusses with Automotive Industries (AI) some of the challenges facing suppliers of complete tube systems.
Kraus: Our aim is not only cost reduction but also to achieve improvements with regard to the size and the weight of a part or system while at the same time responding to enhanced requirements.
AI: In what areas do you see a potential for growth?
Kraus: We see a potential for growth in the areas of Cooling Water Tube Systems (NORMAFLEX CWS), Transmission Oil Cooler Tube Systems (NORMAFLEX TOC), Hydraulic Clutch Tube Systems (NORMAFLEX HCS), Swivel Joint Exhaust Pipe Clamps (SEC) and flange connections for exhaust systems (NORMACONNECT V).
AI: How do you intend to increase your share of the market?
Kraus: We introduce innovative products that are able to replace existing technologies, for example a cooling water vent line made from polyamide for the E90 instead of a rubber hose as used with the E46 engine. We focus on new technologies and, correspondingly, our investments in R&D are considerable.
AI: What are the trends in using new materials and processes in terms of lower part weight space saving design and increasing overall functionality?
Kraus We replace rubber hoses with light-weight but strong plastic tubes and instead of clamp connections (spigot – hose – clamp) we use quick connectors. Then we integrate valve technologies in our portfolio. For exhaust systems we offer our SEC swivel joint exhaust pipe clamp and the V-clamps to replace flange connections.
AI: What is the cost comparison with alternative materials?
Kraus Cost reduction with new technologies amounts to 30% – 40% as compared to the former part price. We offer complete systems with perfectly matching components. We can rely on a vast product range and we are able to develop, design, produce and test almost any component. In our accredited test laboratory we can simulate almost any real-life situation of an engine. Thus we can test and design our systems in line with given requirements. Line systems consisting of components made by different manufacturers often combine different connection technologies and therefore do not achieve the same performance as our complete systems.
AI: How close do you work with OEM’s in developing new applications – success stories?
Kraus We are represented by resident engineers and account managers at almost all OEMs. Thus our cooperation as an active development partner usually starts at the very beginning of a new vehicle project. We know all requirements and goals from scratch. We often can use pre-developed concepts which only need to be adapted to the vehicle or engine platform concerned. Final testing for verification is then carried out at the OEM’s and in our own life-cycle test procedures.
AI: Tell us about the technology and expertise that goes into developing applications such as the cooling system ventilation pipes for BMW.
Kraus We are developing a solution for the cooling water system ventilation made from plastics that answers the special requirements with regard to the reduction of weight, size and price. Together with BMW we have thus worked on the modification of the E90. The functionality of our plastic lines could be verified in a number of life-cycle tests during summer and winter operation.
More Stories
NXP accelerates the development of software defined vehicles with new family of Ethernet switches
Flexible Magna Manufacturing Solutions: The Key to Success in the Automotive Industry
Meet Rita Case – recipient of 2024 NAMAD Lifetime Achievement Award