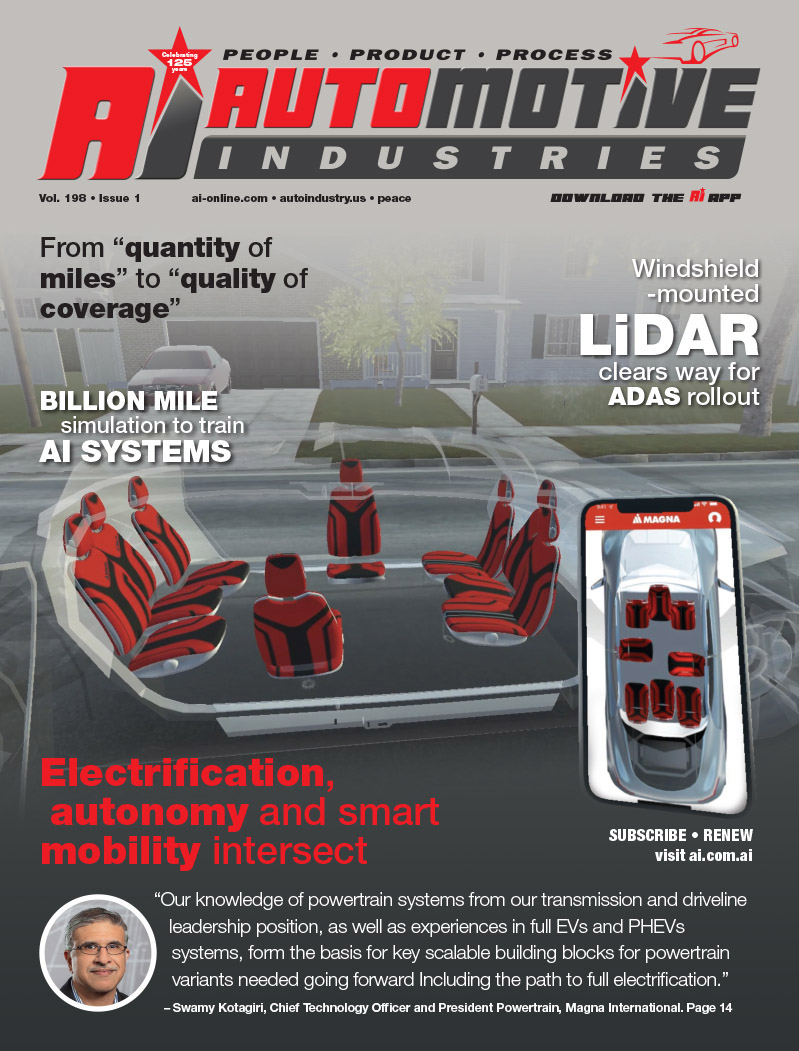
The Wave of the Future?
WaveCrest sets a course to bring wheel motor technology to the automotive industry.
 ![]() |
This detail of WaveCrest’s wheel motor shows (from left to right) the cover, stator assembly and rotor assembly. |
�I was first exposed to the company back in June,” Schaum says. “After retiring from DCX, I was doing some consulting on the future of powertrain for automobiles. I did a web search on hybrid electric vehicles and stumbled on to WaveCrest.
Coincidently, Schaum was contacted by a headhunter who was working for a company that was looking for someone to begin the commercialization of their automotive technology. That company turned out to be WaveCrest Laboratories. The relatively young enterprise founded in January of 2000 is continuing the development of a revolutionary electric propulsion technology, the brainchild of Siberian neurosurgeon Dr. Alexander Pyntikov.
“I was asked to come down and take a look and frankly, I was quite skeptical,” Schaum says.
Schaum knew that wheel motors have been a desire of automotive engineers for some time. Wheel motors were the only technology missing from General Motor’s HyWire fuel cell “platform vehicle” that AI drove last year (AI January 2003, pg. 42). In fact, Larry Burns, GM vice president, research and development has already visited WaveCrest’s facilities.
“I went down there and I just fell in love with the technology,” Schaum says.
Schaum consulted with a couple of motor experts and checked out the numbers on WaveCrest�s web site, paying close attention to things like efficiency and torque density, the amount of torque you can get out of a device for a given volume.
He now heads Vehicle Systems, WaveCrest’s automotive group that was formed in the first quarter of 2003.
WaveCrest�s first automotive application is a version of its Adaptive Motor System, the same electric propulsion system used to power its TidalForce M-650 mountain bike.
In simplified terms, the wheel motor is a large electric motor, like the ones you might find on a slot car. In a regular can motor, the armature spins inside the can when an electric current is applied. A wheel motor is an inverted architecture. The armature, in essence, is bolted to the vehicle and the “can” spins around it.
The wheel motor is made up of an aluminum hub, lined with a permanent magnet. Inside of the hub is a multi-phase, DC brushless motor, arranged so that the rotor surrounds and rotates around the center-mounted stator. The rotor is made up of a series of independently-controlled electromagnetic coils driven by a proprietary power electronics module. The housing is backed by an iron plate, a necessary part of any electric motor. The rotor turns on Timken bearings.
The magic is in the electronics and algorithms that control the coils.
Schaum says that the system can be updated every 100 milliseconds, keeping track of the position of the rotor and optimizing when the coils need to be turned on or off. The algorithms used to control the coils are the reason that WaveCrest has been able to demonstrate what Schaum says are here-to-fore unheard of torque densities.
Schaum says that the motors on WaveCrest’s first demonstration vehicle are exceeding 700 Newton-meters and the laboratory has tested motors approaching 1000 Newton-meters in a volume that fits into a 16-inch wheel. The benefits of wheel motors reach well beyond the obvious, which is to propel the vehicle.
The “Holy Grail,” as Schaum refers to it, would be four independent wheel motors. This would give engineers full vector control at each corner, or complete control of the torque to each wheel. By controlling the torque command to each wheel, WaveCrest could create a very low cost, super efficient stability control system that doesn’t rely on the vehicles braking system. All that’s needed is a yaw sensor and steering wheel input, which is currently on all cars equipped with stability control.
Going a step further, electric motors can be turned backwards. By turning each rear wheel in a different direction, the vehicle would be a lot easier to maneuver in and out of tight spaces. And in an ideal world, Schaum says the electric motors could be used to stop the car, eliminating the need for brakes and the un-sprung weight they add to the car. Wheel motors also eliminate the need for a planetary gear set or transmission.
“It’s just elegant in its simplicity,” Schaum says, “that we have motors which can either be in a pure electric or a hybrid electric propulsion configuration.
While Schaum says that the feasibility of doing a wheel motor that can be mounted to the front of the vehicle is only a year away, the company is initially focusing its efforts on creating a rear-drive e-axle because they know now that they can make a system that will work for rear-wheel-drive.
Schaum notes that of the 16 to 17 million vehicles sold in North America each year, 60 percent are front-drive vehicles. He sees WaveCrest’s e-axle as the perfect supplement to front-drive vehicles. Schaum can also see the technology integrating into GM’s full-size hybrid pickup.
“Our idea is to take the output through the inverter to a storage battery and out to a pair of hub motors.
A Smart roadster equipped with a rear-drive e-axle will be used to test algorithms and further reduce the mass of the system. Schaum says that they are learning that the early motors are far more massive than they need to be. Schaum envisions making the housing lighter by making it part of the wheel. The iron backing plate can also be thinned up and Schaum says that research will determine the necessary size and number of Neodinium magnets needed for the coils.
“We�’e getting smarter and smarter,” Schaum says. “I wouldn’t have signed on with the company if I didn’t think we could do it.” But he doesn’t see any of WaveCrest’s technology showing up on vehicles before the 2007 or 2008 model year.
“If you think about it,” Schaum says, “we’re already launching the 2004 model year and everything takes three years for validation.
The next step toward commercialization of the product is to develop a manufacturing strategy. Schaum is currently talking to major motor manufacturers intending to outsource that part of the process to a company that’s well established and has good quality systems installed. The next phase will be to partner with an existing Tier 1 supplier. Schaum says that it’s necessary to partner with someone who not only has the respect of the OEMs but knows all of the steps required for commercialization such as ISO9001, Six Sigma quality control.
WaveCrest isn’t concentrating all of its efforts in the automotive industry. The military has shown some interest in the technology due to the stealth and agility of a vehicle equipped with the system. WaveCrest is also marketing an electric mountain bike with a wheel motor on the rear hub and battery pack on the front hub and bidding on contracts for electric scooters and wheelchairs. Schaum finds it interesting that none of these electric vehicles use wheel motors, noting how they can increase efficiency and range as well as allowing for faster recharging. The space currently occupied by the motor could now be used as a storage space and the use of wheel motors would allow for the chairs to be folded so they could be easily stored.
And just for fun, WaveCrest has designed and built an outboard motor that uses the wheel motor technology.
There seems to be no end to the uses for wheel motors.
More Stories
Best Wheel Size for Off-Road Adventures: What People Get Wrong
Trusted Auto Collision Repair That Restores Both Performance and Peace of Mind
What You Need to Know About Tire Pressure in Winter vs Summer