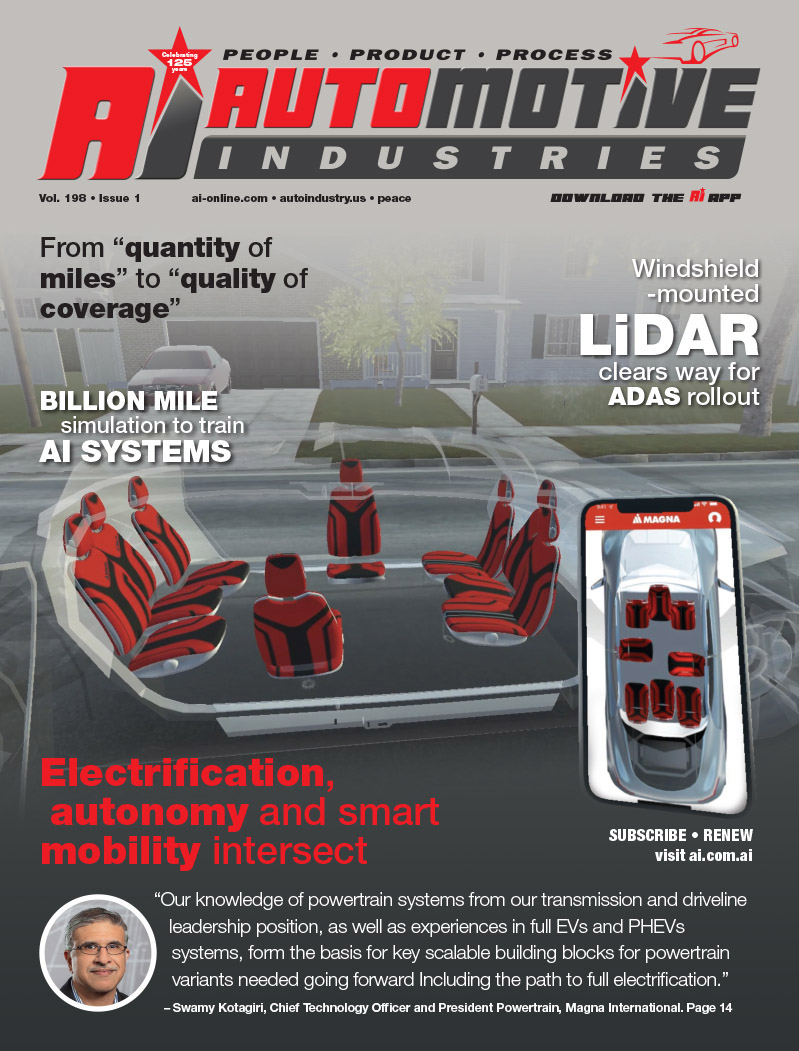
Sealing the Future
Wacker Chemical Corp. turns innovation into warranty cost savings.
![]() |
Wacker liquid-injection sealing technology on this Ford Motor Co. oil pump reduced warranty leak failure from 3 percent to zero. |
Wacker currently has six production facilities and 10 sales offices throughout North America. Wacker Siltronic is headquartered in Portland Ore., and the group’s silicones, ceramics and specialties business divisions are located on a 240-acre campus in Adrian, Mich., (about 60 miles southwest of Detroit).
Serving as a central production, sales and R&D facility, Wacker has been producing elastomers, silicone fluids and silicone emulsions at the Adrian site since 1969. Its siliconebased products are used for such automotive applications as lubricants for airbags and seals for powertrain systems. Wacker is also a leader in injected gasket technology on assembled engine components.
President and CEO, Dirk Funke says that Wacker sees a 5 percent average yearly growth rate in the global silicones market through 2006, with North America and China targeted as growth regions for Wacker.
Liquid injection sealing
Liquid injection sealing is the latest technology in powertrain sealing combining the best of both liquid and molded seals. In lieu of an O-ring of gasket, the part to be sealed is assembled prior to the injection of the material. The sealant is injected through a port into a cast-in or machined groove on one of the mated surfaces.
Thomas G. Jacobs, an applications chemist for Wacker, says that the advantages to this system are excellent performance due to a custom fit for each assembly and a cost savings as there’s no need for mold tooling or part inventory. Ford Motor Co. turned to Wacker to help them solve an oil pump sealing problem on its 3.8 and 4.2L V-6 engines found in the Mustang and Freestar minivan.
“The part they were using had about a 3 percent warranty leak failure,” Jacobs says. “Using this system they are now down to a zero leak failure with 750,000 units on the road. “We’re bolting the oil pump directly to the front cover with a small groove in the oil pump and injecting the material on their production line,” says Jacobs.
Jacobs says that Ford realized an 85 percent savings in material and installation costs alone and further increased savings by reducing the warranty leak failure.
The material is applied robotically which improves accuracy and precision. Ford worked in conjunction with Wacker in the design of the application and control systems that are unique to this procedure. The robots need very little maintenance (a 30 cent tip needs to be replaced every eight hours) and they can be programmed to fill any size or shape cavity.
The material cures in three minutes and is pressure tested for three-and-a-half minutes at 75 psi. The injected sealant displaces the air through the part flange forming a seamless seal. The injection pressure and volume can be monitored for “real-time” quality control.
“By watching for a pressure spike during injection,” says Jacob, “we can tell when the groove is filled. We then have a volume calculator which tells us whether the groove has been completely filled or not.”
Jacobs says that the system is so sensitive that it has provided Ford data that shows porosity variances on its castings Wacker has developed two types of expansion-sealing materials. One that swells when exposed to motor oil or other petroleum products and one that swells when exposed to coolants or water-based products. “Since this material is expanding over time,” Jacobs says, “we can maintain or retain fastener preload through the life of the vehicle.”
Wacker is able to seal a wide latitude of surface finish requirements from 15 micrometers to 300 micrometers.
Though Wacker has yet to prove it, theory is that injection sealing results in a reduction in vibration. By eliminating the shim material that is inherent in most gaskets, the metal to metal joint, in theory, will transfer the vibration over the entire surface of both parts.
Wacker has tested the seals to 300,000 miles at pressures as high as 100 psi. They were also treated to a bath in used diesel oil. “We chose used diesel oil,” says Jacobs, “because it is very high in sulfur content and very acidic.”
Production trial runs of 35,000 units were done with zero warranty issues with 30 months in service. Wacker is now working with Ford on front and rear transmission seals. They are also working with DaimlerChrysler on rear end seals and with Visteon on seals for power steering pumps.
Jacobs says that Wacker is developing applications for radiators and HVAC systems. “Silicone is a great material for sealing HVAC,” Jacob says, “because it doesn’t mildew.”
Fuel cell manufacturers are very interested in a sealing material that expands when it comes in contact with water. Wacker has partnered with Ballard to develop seals for fuel cell stacks. Currently the stacks are sealed with several hand-applied layers.
Wacker is developing a one piece gasket that will replace the multiple layers. Ballard is also working on replacing the hand-tooled carbon plates with plates molded from a carbon powder. Wacker is working on the development of an adhesive that will hold the carbon together.
Frictional Coatings
Wacker’s EKagrip frictional coatings are designed to increase the coefficient of static friction in powertrain applications such as central bolt designs in crankshaft and camshaft applications, continuous variable timing and balancer shaft modules. Wacker is currently testing several fastener applications.
“Fastener people are looking into this technology because it may solve a lot of their problems,” says Michael A. Fundus, senior manager surface treatment. Wacker is also looking at the potential of using EKagrip for transmission, clutch, suspension/chassis and body applications.
The coating is not affected by lubricant films and can be applied as a tailor-made shim, foil gasket or as a direct coating. EKagrip is a nickel dispersion coating made up of electroless nickel layers with entrapped hard material particles. Wacker uses diamond particles, but Fundus says that these could be replaced with carbides. When the EKagripcoated part comes in contact with the mating surface, the diamond particles penetrate the mating surface increasing friction by as much as 300 percent.
Wacker has developed a unique way of applying the EKagrip coating. Tailor-made foil gaskets coated with EKagrip are designed so the coating can be applied exactly where its needed. With an industry emphasis on lightweight engine designs and mass reduction, powertrain engineers have gone to many aluminum engine parts.
“Unfortunately,” says Fundus, “aluminum has very low coefficient of friction. A 1 mm thick EKagrip foil doubles the coefficient of friction of aluminum.”
Wacker is currently supplying GM with a captured washer that fits over the damper hub on the GM’s inline four- and five-cylinder engines that power the 2004 Chevrolet Colorado and GMC Canyon mid-size pickups.
The injection-molded Elastocil ring has a tailor- made EKagrip foil gasket that fits inside. Wacker manufactures the washer and foil gasket and installs it on the damper hub before shipping the part to GM.
Fundus says that starting in 2004 Porsche will be using at least one friction foil on all of their engines.
More Stories
5 Conclusions One Can Make by Analyzing Car Accident Statistics
Why You Should Invest in Regular Car Washes to Protect Your Investment
Workers’ Compensation for Repetitive Stress Injuries