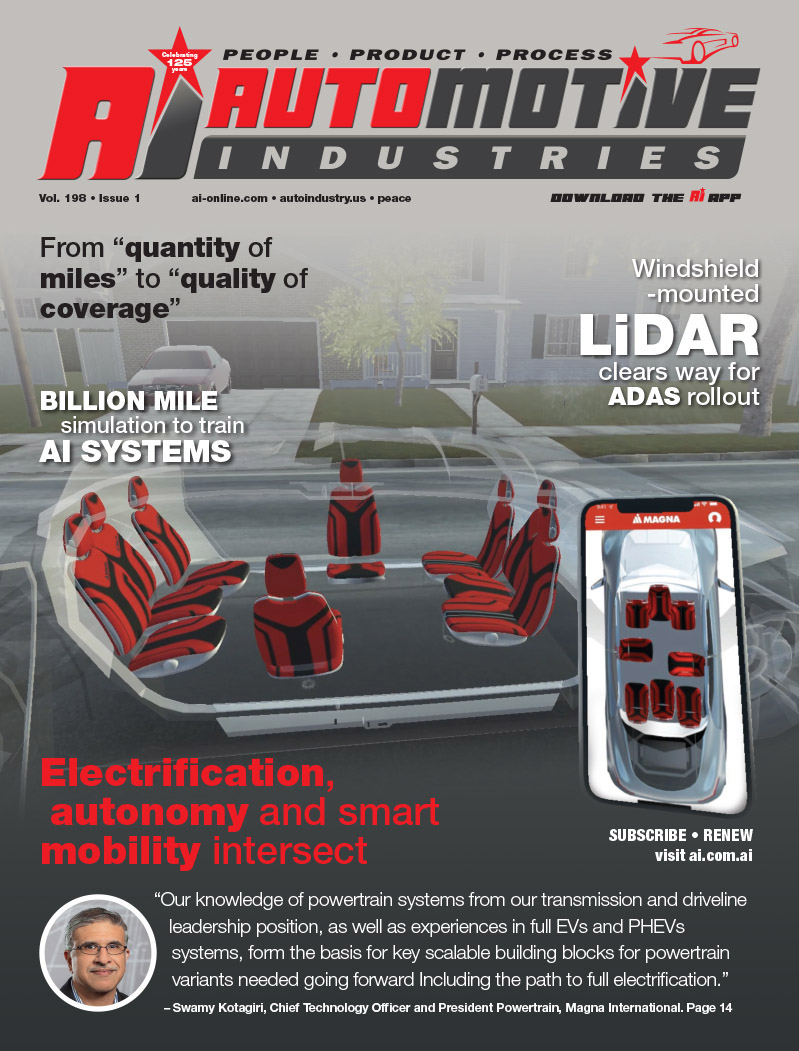
All GM vehicle engineering is back at the Tech Center under one roof.
![]() |
GM’s entire vehicle engineering team will work together in this new addition to the Warren, Mich., Tech Center. |
Drawing boards have been replaced by computers and a virtual reality studio allows designers to view their creations, or sit behind the wheel of an interior, before any models are built.
The Research and Development Center, one of six labs around the globe, works in conjunction with leading universities and government agencies to forge new frontiers in mechanical and chemical science as related to the automobile.
Advanced vehicle development is done in the Portfolio Zone. Built about a year ago, the facility offers a large space to bring in competitive vehicles for comparison and examination, a private meeting room for top level management to hash out the details and a state of the art computer center, where math data is projected on one of three large screens. Designers, engineers and marketing people can make real-time changes to mathbased computer models, cutting into the time it takes to bring new vehicles to market. Math data is a large part of manufacturing as well, as GM implements its Global Manufacturing System. Everything from floor design to ergonomics can be done virtually, saving time and materials.
On June 18, 2003, GM dedicated the newest addition to the Tech Center campus. The 2.2-million square-foot Vehicle Engineering Center (VEC) will consolidate all of GM’s North American engineering under one roof, in close proximity to all of the other vehicle development functions.
“What we have in place is the continuum of activity in our vehicle development process,” says James E. Queen, GM Vice President, GM North America Engineering. The bright blue, eight-story tower, rising above the renovated podium office building will house the 11 vehicle line teams in a program management area, with electrical, structural, HVAC engineers, etc. each with their own floor. The new building also has a physical mockup area.
“For the first time in our history,” says Queen, “we will have our entire electrical team together in North America. That’s extremely powerful. It will help GM further reduce cost and throughput time.”
Queen says that this most recent journey began in 1992. At that time the company was organized into several separate business units (think Cadillac, Oldsmobile, Saturn, etc.) and each unit had their own engineering center. Truck engineering alone was strung out in 11 different buildings throughout southeastern Michigan.
Though a lot of good work was being done, it created very expensive and time consuming processes. As this consolidation has progressed, since 1996, GM has cut throughput by 33 percent and reduced the collective engineering budget by 47 percent.
The basement of the center houses the core communication center, an impressive computer nerve center that ties GM North America with the other three global regions, Europe, Latin America and Asia/Pacific, allowing them to share data in real time. “We’re doing programs 24-7, around the world,” says Queen. “This is a big advantage for our company because of its size. There are a lot of assets and infrastructure already in place and we’re taking the next step to leverage that.”
Data is stored in what could be the world’s largest server and data storage showroom. Just about every manufacturer’s nameplate (Dell, Sun Microsystems, Compaq) can be seen as you stroll the aisles. The center can back up one pedabyte of data, making it the fifth largest data storage facility in the world. Software upgrades can now be done globally in just two weekends, a job that used to take six months.
The basement also houses VEC’s power station, with plenty of juice to run all of the computers as well as a battery back-up that can run the building for 45 minutes. Workers started moving in last November and will continue to transfer to the new building through the balance of this year into the first quarter of next year. By that time, the full 8,000 person workforce will be on site.
More Stories
5 Conclusions One Can Make by Analyzing Car Accident Statistics
Why You Should Invest in Regular Car Washes to Protect Your Investment
Workers’ Compensation for Repetitive Stress Injuries