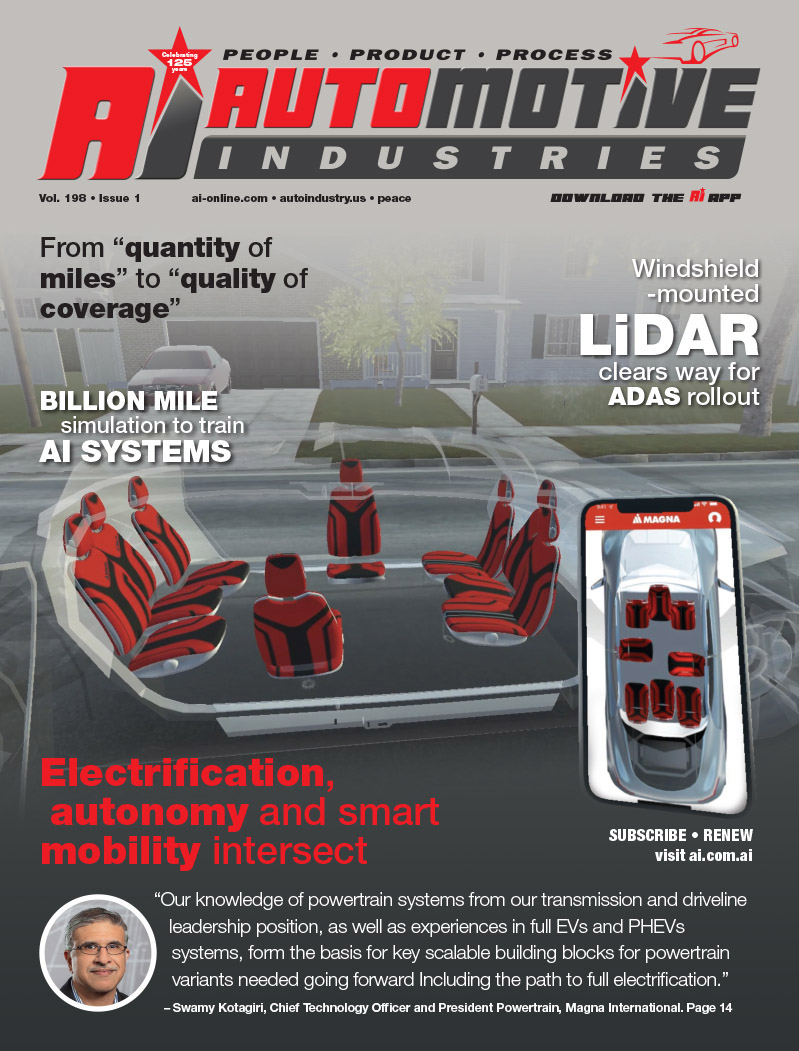
You’d think that with two manufacturing facilities receiving gold and silver awards, three models leading their respective categories and the Cadillac brand finishing a strong second in the latest J.D. Power Initial Quality Survey, that Gary Cowger, president of General Motors North America would be on top of the world. Well, not quite.
For the sixth straight year, he’s watched the Toyota Motor Company grab the coveted winner’s trophy — the trophy that Cowger is certain will one day belong to GM. Certain enough that he and other members of GM’s manufacturing team are on record as saying it’s not a matter of ‘if we beat Toyota, but ‘when’ — a rather lofty goal considering the competition. “I absolutely think it’s a realistic goal,” says Cowger. “I’m not as hung up on a time frame because I can only control how good GM’s quality continues to progress.
“I don’t know what (second place) Honda and Toyota are going to do every year. If they deteriorate again it may be sooner rather than later. If they don’t it’ll probably be a longer period of time. But the point is, that is the goal and I think we’ll get there.”
![]() |
Gary Cowger (right) and Cadillac General Manager Mark LaNeve reveal the 2004 Cadillac CTS-V at the New York Auto Show. CTS single-handedly vaulted Cadillac to second place among brand names in the 2003 J.D. Power initial quality survey. |
J. D. Power’s 2003 IQS showed that for the first time since 1998, the industry average remained flat at 134 problems per 100 vehicles (PP100). But more importantly to GM, both Toyota and Honda showed a significant drop in the quality ratings. (Toyota dropped eight points from 107 PP100 to 115, Honda from 113 to 126). Are we finally seeing a kink in the mighty Toyota’s armor?
“As their product line-up gets broader and broader,” Cowger says, “they’re running into the same issues that those of us who are fullline manufacturers have, and that is you’ve got a lot of entries in a lot of segments and a lot of customers to make happy.”
Those “issues” created the opening that could have moved GM past Honda and pulled it within drafting distance of Toyota. And while they did close the gap it wasn’t quite the way they had hoped. GM saw a deterioration of three points, dropping to 134, one point below the industry average.
“Are we happy with it? No,” Cowger says. “There are a couple of launch issues that we can isolate that if we hadn’t had them we could have had as high as an eight point improvement.” Cowger won’t get specific, but admits that one of those issues was supplier related — an infant failure that should have been caught in validation, but somehow made it through the system and out to the customers. The fix was quick, but not quick enough to keep it from showing up on customer’s Power surveys. Major issues rarely show up on J.D. Power surveys these days. NVH and noise related issues are the top complaints among those surveyed. And things like fuel mileage have found their way onto the list. It was the fuel mileage on GM’s Hummer H2 that helped banish it to the bottom this year, further hurting GM’s overall score.
“I’d be surprised if they didn’t see it coming,” says John Ivers, partner and executive director of quality/customer satisfaction at J.D. Power and Associates. “They do a survey of their own, actually, we do it for them, that gives them early warning on these things.” In fact Ivers believes that GM has a competitive advantage over other manufacturers because they have J. D. Power do their quality tracking work. Other OEMs, who use other metrics that differ from the Initial Quality Study, create a certain amount of internal confusion as to what goals to shoot for. “That tends to, in some cases, demoralize workers,” says Ivers, “when they shoot for moving one particular needle and pull it off, but it doesn’t really affect initial quality.”
“It also adds cost,” Ivers continues, “because you wind up having one layer of analysts for the J.D. Power results, another layer of analysts for the internal tracking folks and a third layer of analysts to figure out why the two don’t always agree.”
GM not only uses J. D. Power’s metrics to measure quality, but has pushed the J.D. Power IQS results right down to the shop floor. Cowger stresses that it’s important to get everyone thinking about the customers, and what the customer’s aspirations are.
“That’s their role in this thing,” Cowger says. “They’ve got to take the design they’ve been given and execute it flawlessly.”
![]() |
Fairfax assembly workers created the ‘verbatim car’, a Pontiac Grand Prix with J.D. Power survey complaints called out on the vehicle. Workers now have visual eveidence of the areas that need special attention to quality. |
“That ends up being best practice,” Cowger says. “It gets blown throughout the whole system.”
While Cowger had hoped for a better overall showing in the IQS survey, he is very pleased to see that GM’s Global Manufacturing System (GMS), a system that he helped implement, is finally showing results. “That’s one of the reasons why eight of the top twelve plants (in the 2003 J.D. Power IQS) are GM plants,” Cowger says.
GM’s manufacturing facilities also posted significant improvements in the The Harbour Report 2002, with a 4.5 percent overall improvement. For the first time in the history of the report, GM moved ahead of Ford as the number one domestic manufacturer in assembly, engine and transmission quality — a direct result of GMS, according to Ron Harbour.
GMS is rooted in the Toyota Manufacturing System, a system that GM has had access to since the NUMMI joint venture in 1983. If the system can post such great quality numbers, why has it taken so long to show any effect? “It’s taken way too long,” says Cowger. “It’s been a 10 year journey getting manufacturing converged. I started the manufacturing center back in ’92, but I think that what happened is that it took a long time to get the building blocks in place, which included by the way, people’s attitudes and beliefs.” Ron Harbour says that they failed to initially understand how the Toyota system worked.
“The first mistake they made was coming back and trying to emulate the tools,” Harbour says.
GM thought that installing things like ANDON systems and error-proofing stations were the keys to Toyota-like quality. “In the maturation of a lean organization,” Harbour continues, “those tools really come later in the process. You have to have a strong team-based organization and as they start the process of problem solving, they pull those tools.” Those tools are an answer to situations that arise that cause quality, cost or productivity problems.”
One of GM’s shining GMS stars is Lansing Grand River. The greenfield plant launched the Cadillac CTS last year with a J.D. Powerrated score of 88 problems per 100.
“That’s a Toyota-like number,” says Ivers, “To do that in a greenfield plant is noteworthy,” he adds. And to do that up north in the land of the UAW is also noteworthy. They’ve clearly achieved something worth replicating there.” Ivers also points out that the CTS’s IQS score was the driver that moved the Cadillac brand into second-in-class behind Lexus in this year’s survey.
“Most manufacturers that I know that have tried to benchmark a BMW 5 series,” Ivers says, “have gone into that expecting their CSI and IQS performance to deteriorate, just because those customers are tougher customers. GM not only got those customers with the CTS, but got such great reviews from them in initial quality.”
“I think we’re already starting to show that our launch process and the GMS are working very well,” Cowger says.
Harbour says that Lansing Grand River is a testament to the (GMS) system. He says that what GM has done right is realized that they don’t really need to work on productivity if they focus on quality.
“If they get quality the right way by having good repeatable processes and predictable processes,” Harbour says, “then the rework, the repair, the overtime, all of that stuff starts to fall away — costs come down and productivity goes up.”
With the success of Lansing Grand River behind them, GM will really put GMS to the test this year and next. They are scheduled to launch 16 new products in 2003 and follow that with another double digit launch in 2004.
While Cowger admits that no manufacturer has improved its quality rankings with so many simultaneous launches. “The game plan next year is to do the launches and not deteriorate at all,” he says. “That would be a first.” “That’s a good goal,” says Ivers. “There are a few manufacturers who outdistance that.”
Ivers says that Toyota tends to do better than GM in launching its vehicles, launching them somewhat better (about 5 problems per 100 vehicles better) in initial quality than the vehicles they replaced.
J.D. Power data demonstrates that the Chrysler Group has gotten an even better launch discipline together. Their new programs launch with an initial quality of about eight problems better than the vehicles they replaced. “GM has gotten fairly good at its launch disciplines but not to that point.”
![]() |
Cowger (right) introduces the Malibu Maxx SS at the New York Auto Show. GM is betting on Malibu to gain back market share from Honda and Toyota. |
“Let’s say you pass them one year and your five points ahead,” Harbour says. “I don’t think that’s going to do it. What will be necessary is to show consistent performance.” Ivers says that while initial quality is important, what is more important to consumers is the longer term quality of these vehicles. “It influences more purchase decisions among consumers,” Ivers continues. “And it really represents a bigger gap between GM and Toyota.”
“The hardest thing to overcome is the perception that you make bad cars,” Harbour says. “GM, and Chrysler are still trying to live down the vehicles that they’ve built in the past.” Harbour says that even if the cars that they build today are as good as a Toyota or Honda, they will still need to convince the buyer that they should try GM again.
“One of the virtues of a Toyota, from a consumer standpoint,” Ivers says, “is that the question of whether or not they can fix them right the first time is sort of a moot question. That’s because Toyotas just don’t break very often.”
GM is taking steps to design more durable vehicles. They have enlisted help from Tatsuhiko Yoshimura, a retired Toyota quality expert. “Jim Queen, (vice president, GM North America engineering) “has brought him back to look at the whole engineering process,” says Cowger.
Yoshimura will look for ways to improve the design and product development processes.
Cowger says that he will also interface with the manufacturing group, giving insight on how GM is doing things compared to what he saw at Toyota and recommending improvements.
“He’s been very complimentary of our manufacturing system so far,” Cowger says. GM also understands if they really expect to pass Toyota that GMS needs to apply to more than just manufacturing. On May 1st, Kent T. Sears was named North America Vice president, manufacturing processes and global manufacturing system implementation. His will be responsible for the continued implementation of GMS for everything outside of manufacturing.
“Its further recognition by GM,” says Harbour, “that GMS is not just a manufacturing system, it’s a whole business system, as the Toyota Production System is.”
Harbour says that what will ultimately make GMS work for GM is that GMS isn’t the special of the month like so many of the programs in the past.
“It truly has been something that they’ve developed and stuck with now for over ten years,” says Harbour.
While most of the elements are in place for its push to the top of the quality charts, GM still has to deal with issues that Toyota has either already taken care of, or hasn’t needed to. For GMS to work, GM will need the full cooperation of the UAW and CAW.
“All of our success is dependent on one thing,” Cowger says, “engaging the hearts and minds of every operator in all of our plants. We’re focused on that and we have been focused on that for the last few years.”
While their relationship has been rocky in the past, GM and the UAW seem to be focused on a common goal these days, becoming a more competitive company and increasing market share. For GM that means more capital and a rising stock price. For the union it means job security and a possible increase in the number of jobs.
“I think they probably have a more constructive relationship with the UAW and the CAW than most people would believe,” Harbour says. “They’ve made the UAW part of this.”
That relationship will be put to the test when contract negotiations begin in September. A tough time at the bargaining table won’t help GM realize their launch goals.
GM will also need to improve supplier relations if they plan on staying on top once they get there. According to a recent study by Planning Perspectives, Inc. top suppliers have a better relationship with foreign OEMs operating in North America than they do with the U.S. Big 3.
While it is difficult to say if this affects quality, John W. Henke, head of Planning Perspectives, says suppliers say U.S. automakers value cost much more than quality compared with Japanese automakers.
The domestic automakers renegotiate prices with their suppliers every year, he says. This results in suppliers possibly reworking a component to bring down costs and with it, occasionally, quality.
“Japanese feel they got the best price at the beginning and just ask for productivity increases,” he says.
Henke’s says that the approach that domestic OEMs are taking appears to be alienating suppliers not involving them and not looking to the supplier for help and support.
“I think we all have a pretty good handle on supplier quality now,” Cowger says. “In fact, since we’ve put the supplier quality group in, headed by Kevin Williams, who we just promoted to vice president, quality in North America, we have cut supplier spills by over 50 percent per year. The suppliers, quite frankly are getting better at it. The good ones are getting lean and putting in the right manufacturing processes to make sure that they ship nothing but quality.
“In fact in many cases they have the expertise we need to deliver these next level execution steps in quality.”
But Cowger feels that GM needs to do a better job of bringing suppliers in earlier in the integration process.
And then there’s always Toyota. To paraphrase the old racing adage, catching Toyota is one thing, passing them is quite another.
“If you ask Toyota, they have plenty of room for improvement,” Harbour says. “They do believe they’re one of the strongest companies in the industry and they have every reason to believe that. They’re always trying to find ways that they can take more cost out or bring quality to a higher level. They are in this endless pursuit of building every vehicle out their plants with absolutely no defects.” Is GM at Toyota’s level?
“Not by any means,” says Harbour.
But he agrees that they are well on their way down the quality road and ahead of their other domestic competitors. “At the end of the day,” Cowger says, “what we’re after is getting delighted customers.” Harbour says it’s those customers that will ultimately benefit.
“Toyota, Honda and Nissan, have made GM, Ford and Chrysler better companies,” says Harbour. “They’re raising the bar, and the winner in that is the customer. Pricing is better, features are better, and quality is dramatically better than when you and I first bought cars.”
More Stories
5 Conclusions One Can Make by Analyzing Car Accident Statistics
Why You Should Invest in Regular Car Washes to Protect Your Investment
Workers’ Compensation for Repetitive Stress Injuries