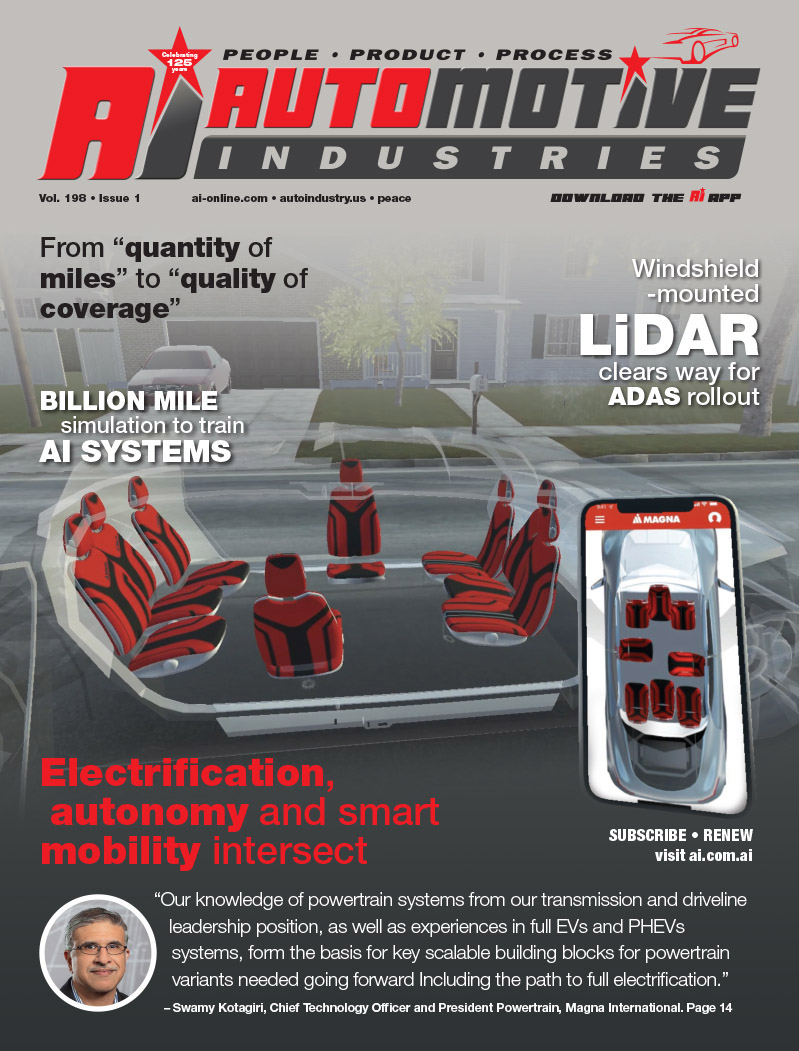
General Motor’s Fairfax assembly plant in Kansas City, Kan., is poised and waiting. Workers rolled the last 2003 Pontiac Grand Prix out the door on February 6, 2003 and production of the 2004 Chevrolet Malibu, the first North American-built Epsilon platform vehicle won’t start until August. Gary Cowger, GM’s President of North America, says that the extended launch window had to do with some shuffling of GM’s product launches.
“When (Bob) Lutz (product development and chairman, GM North America) and I came into these jobs, Cowger says, “we pulled the (2004) Grand Prix ahead because we needed to get some activity going in Pontiac.” The ’04 Grand Prix joined the rest of the MS2000 platform family in Oshawa, Ontario Canada, and Lansing, Mich. is still building the current Malibu through August.
“We didn’t need to shut the plant down,” says Troy Clarke, group VP manufacturing and labor relations. “This is a unique situation for a manufacturer and we’re taking advantage of it.”
GM invested $500 million dollars readying Fairfax for Malibu production.
![]() |
Three of Fairfax’s 200 team leaders fine tune their assembly station in preperation for the 2004 Malibu launch this August. |
![]() |
Workers inspect a Malibu side panel. The panels are stamped in one piece, both inner and outer. |
GM has also invested $50 million dollars in a 55,000 sq.-ft. addition to the body shop that houses a six-stage Muller Weingarten press, installed to stamp the Malibu’s one piece inner and outer side panel.
In fact all of the exterior sheet metal for both the Malibu and Malibu Maxx will be stamped at Fairfax.
A new conveyor was installed in the assembly area to handle the cockpit installation. Delphi will supply the cockpit module. The engine subassembly area has been pared down from 10 stations to two. Workers now dress the engine with parts specific to Malibu and marry the engine to the cradle before it’s sequenced into the line. GM wanted to source out the entire engine and cradle sub-assembly, but union workers fought to keep some of it in-house.
Union representatives say that outsourcing will be a topic of discussion in the upcoming contract talks. The UAW would like the opportunity to bid on any jobs that GM wants to outsource in an attempt to keep them in the plant.
GM also did a complete renovation of the paint shop. The initial plan called for three semi-robotic booths but after discussions with the union, it was decided that the lowseniority paint booth jobs could be eliminated and the paint shop was converted to two fully-robotic booths.
GM’s global manufacturing system allows for the re-use of machinery and equipment between plants. When all of the facilities are brought on board, GM will be able to pull machinery from one plant and simply plug it into the same footprint at another, linking it to the same controls architecture. Fairfax is receiving about $4 million in equipment from other plants, like segments of conveyor from Oklahoma City, and pieces from Lansing, Mich., Spring Hill, Tenn., and Orion, Mich.
Last year GM saved $24 million dollars by re-using existing machinery and equipment. Combined with the savings in powertrain and stamping, GM saved $60 million dollars in 2002.
By creating a common global launch process, GM now has the ability to gather information from all global launches in one place. A lot of what GM is doing in Fairfax was learned from the assembly of the Opel Vectra in R?sselshiem, Germany, the first vehicle to be built off of the Epsilon platform.
A liaison team made up of workers from the Fairfax plant have spent the last two to three years working in tandem with GM employees in R?sselshiem as well as the design and technical centers in Warren, Mich. What they learn is transferred to the WorkPlace Development Centers (WDC) — an area set up in the plant that recreates a station on the assembly line.
Manufacturing engineers and team leaders work together to find the best way to perform each assembly task. Fairfax’s two WDCs, (one for chassis and one for trim) will be reduced to one once production is up and running. It will be used to test and perfect changes to assembly procedures before they are implemented on the line.
While the team leaders are busy perfecting their jobs, the skilled trades workers are going back to school.
Their jobs will be to install and maintain the new equipment, so they’re being brought up to speed on the new technology that’s coming in.
On-going training is done in the plants’ technical training centers. Instructors are well-schooled in their perspective expertise. They design their own course manuals, paring down the vendor’s manual to focus on only the skills that will be needed to work on the equipment in the plant.
Duplicate robot cells are installed in the tech centers to help instruct in teardown and repair. To GM’s advantage, if a robot goes down on the floor, it can be swapped for the classroom model, and the malfunctioning robot becomes a teaching tool.
About 200 team leaders from both shifts are currently working out the final launch details, doing the first of 600 validationbuilds in buckets of 10, four minutes per station. Team members will return on July 21st with full production beginning on August 11.
GM has set some aggressive quality targets for building the new Malibu. “We would not be able to focus purely on Malibu right now if we were building Grand Prix,” says Bob Dolan, assistant plant manager. “So these build events can get a lot more tense.”
Dolan says that the J. D. Power quality target for this car is 95 (problems per 100 vehicles) “Internally we’re going to set a target lower than that.”
Last year’s Malibu was J.D. Power segment leader at 93.
Dolan explains that the workers have their own reasons for building good, quality cars. “We have the capability to build a higher volume than scheduled,” he says. “We want to hit that target for a couple of reasons.” Dolan says the plan right now calls for a third shift. “We want to make sure that’s a solid plan.”
“The better we launch this product productivity- wise and quality-wise, the more likely the customer will accept this product and it will help us get the third shift. Other than that, I’d like to get a third product.”
Dolan says that Fairfax was originally built with the capability of 66 jobs per hour. With Malibu set up for 47, another product could be flexed into the line to bring capacity back to 66.
More Stories
Easy Car Maintenance Tips to Prevent Accidents Due to Malfunctioning Parts
Exploring the Best 2024 Jeep Gladiator Add-ons for Performance and Style
Maximizing Tire Life with the Right Air Pump for Car Tires