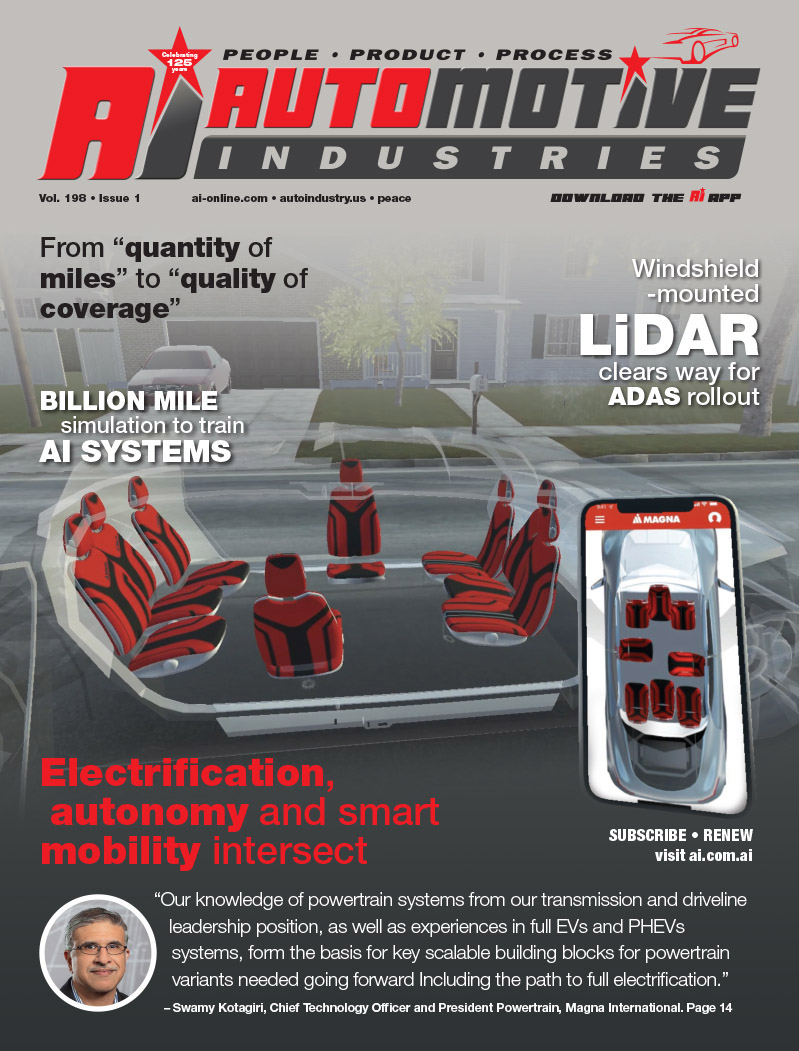
A lot of people seem to think that automotive plants have complete control over their own destiny. They consider a plant’s management and its workforce to be almost exclusive factors in determining whether an operation can be classified as a “good” or a “poor” performing plant.
Nothing could be further from the truth because there are many other critical factors that impact a plant’s performance. I like to think an automotive plant is more like a work of art. Yes, beauty is in the eye of the beholder, but I happen to believe a clean, high-quality, efficiently run automotive operation is a thing of beauty.
A beautiful piece of art is not created by one or two strokes of an artist’s brush, nor how well an artist uses one particular color. It’s the entire body of work that is judged. In much the same way, an automotive plant’s success is determined not by only one or two factors, but by many. Management and non-management workforces play important roles in helping determine a plant’s success.
There are times when management and hourly workers should be held accountable for their operation’s lack of improvement. But at the same time, labor is only part of a bigger picture that determines a plant’s performance. And workers aren’t always making excuses when they say other factors are the real causes when their operations struggle.
I was reminded of this fact recently while working to improve a manufacturing process at an automotive assembly operation. One of our clients was struggling to meet its production goals, mainly because of troubles in one specific area. After visiting with the plant and meeting with company officials, it was quickly determined the problem was not a plant issue — it was a flaw in the design of a new component.
The plant, it turned out, was given a new component that was made up of more parts than the old component. The new component also required many more welds, twice as many load sequences and three times as many metal forming operations.
In order to produce the new component, the plant had to add new equipment and robots, as well as manpower. And that required changes in the plant’s floor plan, because production of the new component required more space — space the plant did not have to devote to this one component.
Is it any wonder the plant was struggling to build the new product? Should this plant be considered a bad operation because it was given a new product that was flawed in its design for manufacturability? Of course not. The struggles at the plant simply were a culmination of flawed design and process.
Michelangelo could not have painted the ceiling of the Sistine Chapel without following a process. Michelangelo received a commission to paint the chapel’s ceiling in 1505. He used the next three years to plan, and then four more years to paint his masterpiece before it was finished in 1512.
Not every vehicle built today is a masterpiece, of course. But good or bad, almost every manufacturing operation provides a snapshot into a company’s way of doing business. Everything from labor and equipment productivity to product and process engineering is on display. So is a company’s approach to lean manufacturing, as well as the processes and practices that are designed to help an operation improve its quality and productivity.
A plant is going to reflect all of the planning and execution that went into it. The best plants, and the best manufacturers, understand all of the factors that impact a plant’s performance. They work hard to carefully put all of these pieces together.
And when it’s done right, it’s a piece of art.
More Stories
Your Guide to Filing a Car Accident Claim
Steps to Take Immediately After a Car Accident
What Makes SUV Cars More Prone to Accidents?