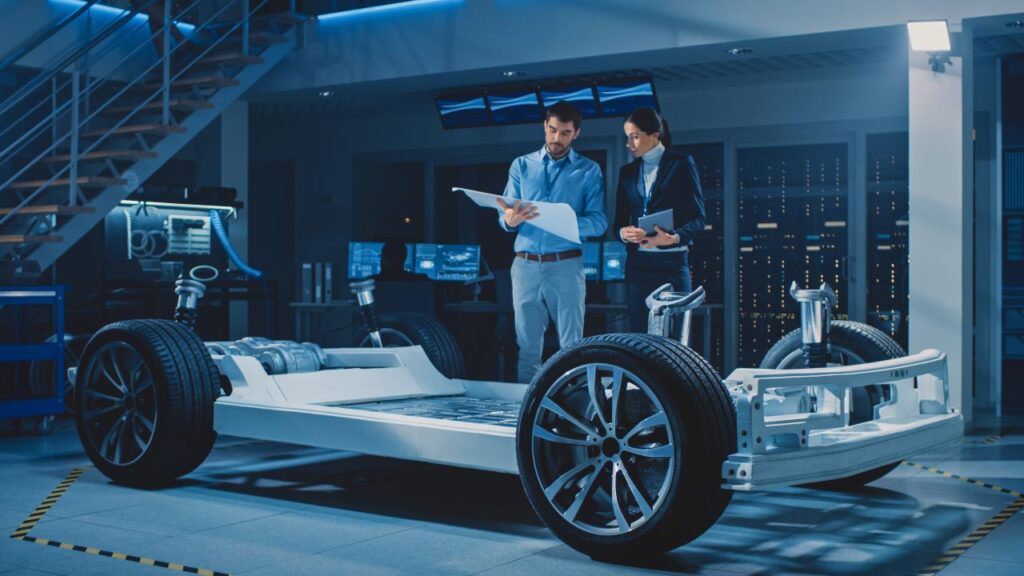
The changing market environment and evolution of the traditional powertrain is transforming the automotive industry at an unprecedented pace.
Composite parts for electric vehicle battery casing applications are making it possible for manufacturers to meet the challenges of developing components that are lighter, stronger and quicker to process.
Huntsman showcased its portfolio of polyurethane products that can be used to create underbody and upper cover battery protection components up to 30% quicker than some existing technologies* at the 2024 Battery Shows in Europe and North America.
The products can also save weight and can increase strength and structural performance. Covering numerous battery protection needs, Huntsman’s one-stop shop includes encapsulation solutions for the thermal, structural and mechanical protection of battery cells. These foam technologies can be tailored to different processing and automated production needs.
Automotive Industries (AI) asked Irina Bolshakova – Global Marketing Director Automotive – Polyurethanes at Huntsman, what new technologies the company showcased at this year’s Battery Shows in Europe and North America.
Bolshakova: At this year’s Battery Shows, Huntsman’s automotive team presented a series of new polyurethane-based developments for battery enclosures, battery cell potting and underfloor protection.
AI: What products does the new range include?
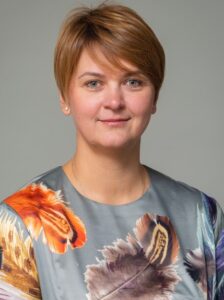
Bolshakova: The new technologies include a novel family of battery cell potting materials – SHOKLESSTM polyurethane systems – and a composite technology developed for thermal and structural battery protection, VITROX® WCM polyurethane system.
AI: How do the new SHOKLESSTM polyurethane foam systems help safeguard the structural integrity of EV batteries in case of impact or a thermal event?
Bolshakova: SHOKLESSTM polyurethane foam systems can provide structural integrity through superior mechanical properties (elastic modulus, tensile strength and elongation to failure) in the range of typical battery operation temperatures. In the case of thermal events, SHOKLESSTM systems are capable of being formulated to meet customer needs for thermal protection.
AI: How do the new solutions compare to non-polyurethane alternatives in terms of providing thermal as well as structural protection at a cell, module, or pack level?
Bolshakova: Huntsman battery solutions can enable automatization for OEMs and battery manufacturers through robotic application and flexible processing temperatures and tunable cycle times.
The versatility of Huntsman’s polyurethane technology can also provide broad mechanical performance (elastic modulus, tensile strength and elongation to failure) helping to fulfil key customer needs.
AI: How can the moldable encapsulant version of the SHOKLESSâ„¢ system further expand design and manufacturing options for EV battery manufacturers and OEMs?
Bolshakova: The moldable SHOKLESSâ„¢ encapsulant version can enable cell protection at different battery configurations, such as cell to pack, and cell to module systems. The moldability can enable flexible choice of battery cells configurations and geometries.
AI: How quickly can you apply your know-how to the challenges facing automotive manufacturers into developing new products that help to address clearly identifiable gaps in the market?
Bolshakova: Our Global Automotive Platform at Huntsman Polyurethanes has dedicated technology and innovation centers located around the world (North America, Europe and Asia) – in close proximity to our customers.
This means our commercial and technical teams can provide support across the regions at local customer facilities – which helps build close customer relationships. Leveraging field insights and internal capabilities (such as modelling and simulation capabilities) also enables our team to respond to customer demands in an agile way, shortening typical industry product development cycles, which can help customers adapt quickly to changing market conditions.
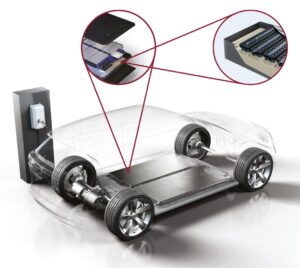
AI: Are SHOKLESSâ„¢ polyurethane systems compatible with different manufacturing methods such as open- and closed-pour (injection) and cold-cure molding?
Bolshakova: Our SHOKLESSTM polyurethane systems are versatile and can be processed using most of the common polyurethane process technologies and manufacturing methods, i.e. open mold pouring or closed-mold injection.
AI: Do you offer simulation and modeling capabilities with the new systems in order to help customers customize and optimize processing parameters, as well as the structural and thermal performance of the materials?
Bolshakova: Yes. We have dedicated simulation and modelling teams. This capability helps customers understand and predict material performance in final applications, such as battery packs: from cell to full pack level.
It can also help customers optimize the processing of our materials (flow patterns, filling rates). Combining processing and material predictive analysis, customers could understand and resolve challenges in manufacturing and improve final performance at the early stage of product development.
AI: And what about your VITROX® WCM system?
Bolshakova: VITROX® WCM system is a new polyurethane technology that can help protect batteries against thermal events when used in battery lids. As the automotive sector’s reliance on lithium-ion batteries has increased, and as the share of electric vehicles on the road has grown, the requirements for housing batteries have become more complex – but effective thermal insulation and lightweighting remain top priorities for specifiers.
VITROX® WCM system is an advanced polyurethane-based solution developed to be used as an alternative solution to mica or metal thermal shields.
AI: What are the main benefits of this system over other alternatives?
Created in close liaison with a global Tier-1 supplier to the automotive industry, VITROX® WCM system has been developed to provide improved thermal resistance alongside the structural performance needed for mission critical battery housing applications.
Thermal shields made using the technology can withstand abrasive impact from overheated particulates. In addition, thermal shields made using VITROX® WCM are easy to process using compression spray or wet compression molding techniques.
Flexible processing of VITROX® WCM system via such manufacturing methods can help to create composite parts of complex shapes with short cycle times.
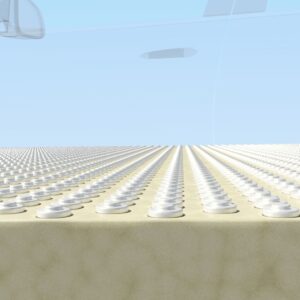
AI: What’s next for Huntsman Polyurethanes?
Bolshakova: The changing market environment and evolution of the traditional powertrain is transforming the automotive industry at an unprecedented pace. With a long track record in the sector, our team is experienced at meeting customers’ needs and helping them grow.
We are fully committed to delivering materials to the current market with traditional automotive polyurethane technologies (seating, acoustics) as well as new, emerging technologies, developed to support the drive for more electric vehicles.
Footnote:
* Compared to other competitive technologies but results may vary depending on specific component design. Data generated by 3rd party lab and owned by Huntsman. Results generated in lab or field conditions which are typical for this application. Data variations due to varying processing or ambient conditions cannot be excluded. These properties are not part of the product specifications.
While all the information and recommendations in this publication are to the best of our knowledge, information and belief accurate at the date of publication, nothing herein is to be constructed as a warranty, express or otherwise. Huntsman warrants only that its products meet the agreed specifications. Typical properties, where stated, are to be considered as representative of current production capabilities and should not be treated as specifications. In all cases, it is the responsibility of the user to determine the applicability of such information and recommendations and the suitability of any product for its own particular purpose. The sale of products referred to in this publication is subject to the general terms and conditions of sale of Huntsman International LLC or of its affiliated companies.
SHOKLESSTM is a trademark of Huntsman Corporation or an affiliate thereof in one or more, but not all, countries.
VITROX® is a registered trademark of Huntsman Corporation or an affiliate thereof in one or more, but not all, countries.
© 2024. Huntsman Corporation or an affiliate thereof. All rights reserved.
More Stories
Some Ways How Motorists End Up in Collisions at U-Turns
Maximise Margins with Proven PPF Tactics
Finding the Car Boot Release Button – Tips and Tricks