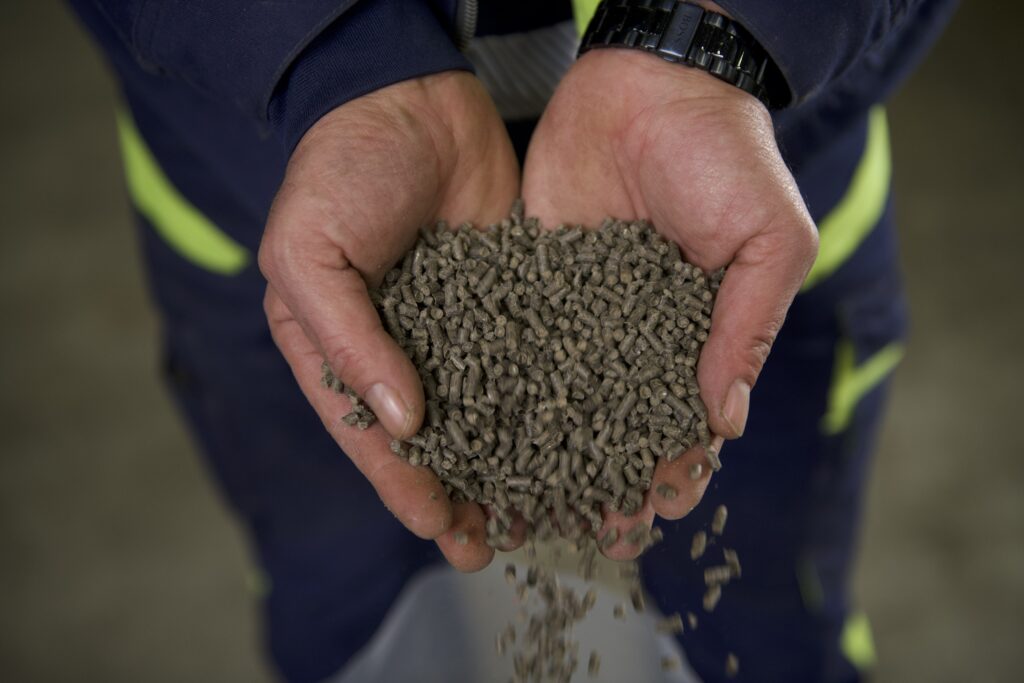
In this Automotive Industries interview, Kurt Kronawittleithner, Global Applications Director at UBQ Materials, delves into the company’s groundbreaking efforts in transforming unsorted household waste into climate-positive thermoplastics. He explains how UBQ’s patented technology breaks down waste into basic building blocks, which are then reconstituted into UBQ™, a sustainable bio-based matrix that serves as an alternative to oil-based resins. This innovative material addresses the growing need for environmentally friendly solutions within the automotive industry, particularly as manufacturers face increasing regulatory pressures to meet End-of-Life (ELV) requirements and aggressive Net-Zero targets.
Kronawittleithner highlights UBQ’s partnerships with key automotive players, such as Mercedes-Benz, which now uses UBQ™ in the production of various car parts. With a focus on expanding its portfolio, UBQ has introduced products like UBQ ClimaPos™ and the UBQ Q Series, both designed to enhance performance and circularity while reducing carbon footprints. These products contribute to waste diversion, CO2 emissions reduction, and resource preservation, making them ideal for the automotive industry’s shift toward sustainability.
Additionally, Kronawittleithner discusses the challenges and triumphs UBQ has faced in promoting this novel material, as well as their collaboration with Teknor Apex to develop more durable and versatile products for automotive applications. As UBQ continues to innovate, the company is positioned to play a pivotal role in shaping the future of sustainable automotive manufacturing.
Automotive Industries interview with Kurt Kronawittleithner, Global Applications Director at UBQ Materials
Automotive Industries: Hi Kurt, can you explain how UBQ Materials transforms unsorted household waste into a climate-positive thermoplastic and the impact this has on the automotive industry?
Kronawittleithner: UBQ Materials uses all residual waste, including all organic and unrecyclable refuse as feedstock to its conversion process. Through patented technology, UBQ breaks the organic waste into its basic building blocks, including fibers, cellulose, lignin, collagens and sugars and binds them with the inorganic materials, reconstructing them into a new bio-based matrix, UBQ™, that replaces oil-based resins in car parts.
This material is an “available now” solution supporting ELV (End of Life) impending regulations in the EU and aligns with the aggressive Net-Zero targets set by global OEMs, alleviating the pressure across the entire value chain to reduce emissions where they are still falling short.
Automotive Industries: What are some of the most exciting innovations within UBQ’s product range specifically tailored for the automotive market?
Kronawittleithner: As a relatively new innovative solution, UBQ has proven itself through its partnerships, specifically in the auto industry. Following commercialization in 2018, UBQ partnered with Mercedes-Benz, and what began as a material replacement in one automotive part in 2019, has now expanded to validation in 33 parts using UBQ™ in place of virgin and recycled plastics, in the interior and exterior of their cars.
After working closely in collaboration with industry partners, customers and various OEM’s, UBQ launched a robust portfolio of products to address our customers’ needs. Our R&D team meticulously engineered them to meet specific targets including odor mitigation, impact and product performance in combination with circularity, increased post-consumer recycled content along with emissions removal and avoidance goals.
UBQ ClimaPos™, an additive that is recommended for load levels 10-20% and enables GHG removal and avoidance as a formulation ingredient. UBQ Q Series is a thermoplastic material replacement that has a neutral appearance and is perfect for applications that do not require a smooth finish.
Both products can be combined with an odor mitigation modifier called UBQ Nclozur™ which was specifically created for use in interior auto parts where stringent odor and emissions standards.
Automotive Industries: How does the incorporation of UBQ™ material into automotive manufacturing processes contribute to reducing the industry’s carbon footprint?
Kronawittleithner: A little UBQ™ can make a big difference, and there are significant environmental benefits, including waste diversion, CO2 emissions removal and avoidance, and resource preservation (fossil or agricultural).
There is also the significant benefit of expanding the recycled content bill of materials for the industry, offering a functional post-consumer material as an alternative to virgin and recycled plastics.
Taking a product out of the waste stream and converting it to a sustainable additive that can be used again in several industries, including automotive, this is true circularity and value for society.
Automotive Industries: Can you provide examples of automotive components currently being produced using UBQ’s patented material?
Kronawittleithner: We have an extensive pipeline of automotive applications currently in the validation process including interior and exterior parts, visual and non-visual, as well as structural applications. Cable channels are currently in series production, and we aim to have more parts “Made with UBQ” in serial production by years’ end. The newcomers include other interior parts such as door pockets, air conditioning and under-body parts. Across the logistics chain, UBQ is also used in logistics boxes at the suppliers’ manufacturing sites.
The value proposition of UBQ, diverting waste and providing a climate-positive, biobased, recycled content option, is an excellent argument for broad application in the industry.
Automotive Industries: How does UBQ Materials ensure the performance and safety of its products when used in automotive applications?
Kronawittleithner: We maintain detailed knowledge of our material’s composition at every stage of the process. By conducting rigorous internal end controls on a lot-to-lot basis, we guarantee our homogenous products consistently meets the required quality standards.
We have a well-designed third-party quality control and verification process to ensure we meet the requirements for participating in various markets. Specifically, we are fully compliant with RoHs and GADSL requirements.
Automotive Industries: What challenges has UBQ faced in promoting the adoption of its sustainable material within the automotive sector, and how have these been overcome?
Kronawittleithner: UBQ is a novel material in a new category of biobased materials. The challenge lies in convincing an innovative leader to spec-in a “Made with UBQ” part into their vehicle. Mercedes, a leader in sustainability and innovation, was willing to work with us and their molders to spec-in a part made with UBQ. Initially, it was difficult for UBQ, as a new material class, to be added to specifications. However, with ongoing discussions about regulations on recycled materials and carbon reduction goals, companies are seeing the benefits of working with sustainable materials and this has worked in our favor.
Automotive Industries: How does the collaboration with Teknor Apex enhance UBQ Materials’ ability to serve the automotive industry?
Kronawittleithner: We initially joined forces with Teknor Apex in 2022, with an expansion in 2023 to help manufacturers create more malleable, long-lasting products and again in 2024 to focus on industrial and consumer durables. They have an excellent reputation as a specialty compounds producer for many applications across the sector, and with their technical teams developing suitable solutions.
Automotive Industries: What role do you see UBQ Materials playing in the future of sustainable automotive manufacturing?
Kronawittleithner: UBQ is on the path to becoming a favorite tool for material specialists to include in their repertoire helping them fulfill an ever-growing requirement of carbon-neutral or carbon-negative products.
Automotive Industries: Can you discuss any upcoming projects or partnerships within the automotive industry that UBQ Materials is particularly excited about?
Kronawittleithner: UBQ has formulated products and passed the notoriously difficult requirements for structural parts. We are currently in development to create new combinations with minerals, like gear box housing, air conditioning parts, under body and under hood parts.
Automotive Industries: Obviously UBQ is the product of this era. What would you wish for in faster / broader implementation?
Kronawittleithner: We were proud to recently be named on the Best Inventions of 2023 list by Time Magazine. My wish is to directly engage across OEMs, defining tangible goals and therefore creating interest with tier-one companies. As the system evolves, companies are required to focus on sustainability goals and we are here to work together to close the loop between the waste and materials ecosystems, bringing circularity and positive climate impact to the automotive industries and beyond.
More Stories
Some Ways How Motorists End Up in Collisions at U-Turns
Maximise Margins with Proven PPF Tactics
Finding the Car Boot Release Button – Tips and Tricks