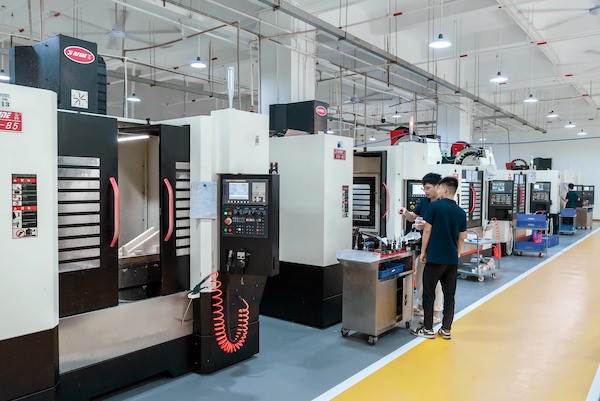
One of the most revolutionary things that AI brought into the manufacturing industry is quality management. With the advent of AI the quality control has enhanced in accuracy and scalability. This shift is most apparent in rapid prototype manufacturing which requires speed and reliability of the quality check process in creating prototypes quickly.
Real-time processing of data is one of the strengths of AI and it translates well to the improvement of quality control processes. From defect detection to performance monitoring, AI systems can be instrumental in ensuring that products that are produced are of high quality.
AI is reinventing quality control in manufacturing by automating various aspects of the process, particularly in industrial design prototyping, where even minor flaws or variations can significantly impact production.
AI-Powered Inspection Systems
One way in which AI is changing the face of quality control is through the use of automated inspection systems. These systems use machine vision, sensors, and even deep learning algorithms for real-time visual inspection for defects, which is far more accurate than manual inspection. For instance, machine vision in a matter of a second can zoom through millions of pixels and see imperfections which may remain concealed from naked eyes of human inspectors. This enhanced accuracy leads to high-quality products as faulty products are not released into the market as they have to meet quality standards.
In the case of rapid prototype manufacturing, such an ability to inspect prototypes is invaluable. The use of AI in the design of the prototype ensures that any issue with the design is identified from the time it is being produced. This is the reason as to why prototypes are designed to have as much detail as the final product; their accuracy is important. AI improves the quality of these prototypes by pointing out flaws and giving feedback that can be acted upon right away to eliminate errors incurred on the process.
Real-Time Monitoring and Data Analysis
One of the biggest advantages of integrating AI for Quality control is that it can monitor the process in real-time and quantity data on production. Previously, manufacturing companies inspected products after certain intervals, which meant that defects could exist between two inspections. On the other hand, AI systems have the advantage of monitoring production lines continuously and enhancing quality while identifying any variance to standard. These systems can observe the defects and at the same time accumulate vast amounts of data which could in turn be utilized for the refinement of subsequent production procedures.
AI can capture data and make important decisions based on that data to preserve quality. For instance, AI can easily indicate when a machine is likely to develop a fault, which would enable manufacturers to fix the problem before it causes production of substandard products. This is especially useful in industrial design prototyping, where quality control and assurance are crucial. Through real-time monitoring and data analysis, AI ensures that fabricated prototypes closely reflect the intended design, eliminating the need for subsequent modifications or potential complications.
AI’s Role in Industrial Design Prototyping
In industrial design prototyping the main aim is to develop the prototype that will look like and perform like the actual product. This process can also involve ‘designing while designing’ and the possibility of running simulations with the new designs proposed under various scenarios. AI plays a big role in this step because it helps to complete some of the actions automatically and guarantees that each of the prototypes reflects the required characteristics.
For instance, AI can help to select the appropriate prototype design by evaluating different parameters that characterize the material, strength and functionality of a prototype. This makes it easier for manufacturers to develop more accurate and functional prototypes in a shorter duration of time. AI also helps to minimize human mistakes or variations that can be encountered during the prototyping of a particular product. AI also helps its users achieve faster time to market since it reduces the amount of time taken to transition from developing a prototype to mass-producing the item.
Moreover, systems that contain elements of artificial intelligence guarantee that prototypes are subject to thorough quality control checks. In industries such as aerospace or automotive manufacturing and other industries where product accuracy is crucial, AI helps to identify discrepancies in the design or the material used before they progress to other stages of manufacturing. Such accuracy is necessary within the digital manufacturing process to develop prototypes which would be useful within the industrial design space.
AI and Predictive Maintenance in Manufacturing
AI is also being applied in predictive maintenance, considered a priority in manufacturing to sustain a high quality. This is where AI is used to help analyze the condition of the equipment to determine when it will be most likely to fail or to need servicing. It would allow manufacturers to detect possible problems before they escalate and create serious complications that might lead to defects or delays in production.
Predictive maintenance systems with the application of Artificial Intelligence use sensors to monitor different machinery variables: temperature, vibration, and machine speed. These systems themselves do not repair the faults, but there are alarms made by the systems that let the operators fix the issues. This saves time and guarantees continuity of production and hence high-quality products.
In rapid prototype manufacturing, product delivery is always a sensitive factor, and this is where predictive maintenance helps to eliminate machine breakdowns which may slow down the overall production process. AI capacity in anticipating and preventing these challenges allows the production lines, especially quality control, to proceed uninterrupted by equipment breakdowns.
Conclusion
AI is impacting quality control in manufacturing as it increases its accuracy, speed, and effectiveness. These approaches assist the manufacturers in maintaining high standards as well as reducing costs and downtime by means of real time monitoring of the machinery, predictive maintenance and defects detection.
However, in rapid prototype manufacturing, the use of AI guarantees precise and quality prototypes that do not take much time to produce. Its use in industrial design prototyping also enables modification depending on the data collected in the real world. Further advancement in AI will see improvement in quality assurance since there will be minimal waste hence contributing significantly to innovation within production.
More Stories
Some Ways How Motorists End Up in Collisions at U-Turns
Maximise Margins with Proven PPF Tactics
Finding the Car Boot Release Button – Tips and Tricks