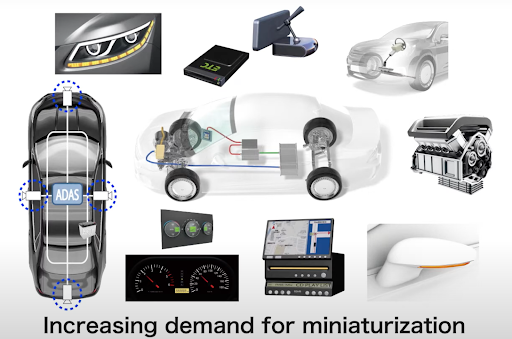
Discrete Mid-Power MOSFETs
Chip-level integration of low-power transistors together with the continual advancement of exotic materials for high-power switching have led to a general neglect of discrete mid-power MOSFETs. However, these devices remain critically important to a wide variety of applications for which off-chip switching can yield performance advantages in efficiency, thermal complexity, and total output power. In the area where silicon carbide (SiC) and gallium nitride (GaN) transistors are considered overkill and integrated common wafer MOSFETs provide inadequate power capability and switching performance, external discrete silicon MOSFETs play an essential role.
Figure 1. Automotive MOSFET Product Map
As discrete MOSFETs are designed in isolation, manufacturers can tailor every aspect of the production process to optimize the switching performance for any given application. The same cannot be said for integrated MOSFETs, however, where the device parameters tend to be bound by the shared characteristics of other devices in the integrated circuit (IC).
For example, the base wafer material and chemistry, geometric feature sizes, thermal characteristics, wire bonding, packaging process, and even the orientation of the devices within the package must accommodate the needs of every component in the IC. The drawback is sub-optimal performance of the power MOSFET.
Discrete MOSFETs, on the other hand, can be optimized for a variety of performance metrics. Typical figures of merit for mid-power MOSFETs include:
- Maximum VDS: the peak voltage that the device can switch
- Eas: Avalanche energy, or the amount of energy the MOSFET can withstand when the maximum VDS is exceeded during a transient spike
- ID: the average and peak drain current that the device can withstand
- RDS: the resistance of the device when conducting — this directly translates to efficiency and thermal loss
- Rth: the thermal resistance of the package; directly translates to ease of cooling the device
- Qg: the total gate charge, defines the switching times at a gate drive current
- Ciss: the input capacitance, which influences switching characteristics
- Size: the physical dimensions of the packaged device
Depending on the application, designers can select from a wide variety of discrete MOSFETs — each with its own set of characteristics — to optimize the switching circuit for speed, power efficiency, and the like. This flexibility and associated performance gain are traded for PCB real estate and the cost of additional components on the board. But, in most cases, this is a trade worth making.
Automotive Requirements
With the increasing reliance on electronics in automobiles, the demands for reliability, size, cost, and performance are growing across every automotive system. As Figure 2 shows, electronic systems built from ICs are permeating virtually every inch of the modern vehicle, including advanced driver assist (ADAS) systems, engine electronic control units (ECUs), and even interior lighting and infotainment consoles.
Figure 2. Automotive ICs Continue to Proliferate
In all of these applications, the constituent ICs, along with discrete MOSFETs, are subject to environmental stressors and reliability expectations that are far more demanding than those associated with their general-purpose counterparts. In an effort to ensure the safety and reliability of automobiles, the Automotive Electronics Council (AEC) has issued a qualification standard that specifies the conditions under which electronic components must reliably function. The AEC-Q100 standard is specific to packaged ICs, and manufacturers label their parts as “AEC-Q100 qualified” to prove to their customers (with internal testing data)that their parts meet or exceed these standards.
For plastic packaged discrete MOSFETs, the AEC-Q101 standard focuses on several reliability pillars across a chosen temperature range, typically starting at -40°C and extending to between +85°C and 150°C.
- Group A tests involve environmental stressors such as temperature and humidity across different storage and operating conditions.
- Group B tests are focused on accelerated lifetime testing, including failure modes and rates at high-temperature operation.
- Group C tests are specific to the packaging of the device, covering wire bond durability, pad solderability, and lead integrity.
- Group D tests are specific to the semiconductor structure, relating to failure modes like electromigration and hot carrier injection.
- Group E tests are focused on electrical functionality and include two models for electrostatic discharge tolerance (ESD).
- Group F tests deal with statistical defect rates.
- Group G tests are for mechanical stressors (vibration, shock, torque, etc.).
To produce a single part that meets AEC-Q101 standards is a significant undertaking and a noteworthy achievement, and therefore commands higher prices and preferential selection from engineers. To build an entire system that uses AEC-Q101 qualified parts is even more challenging — but is critical to ensuring the safety and reliability of automotive operations.
ROHM’s Automotive MOSFETs
ROHM offers a broad selection of automotive MOSFETs optimized for high-speed switching and low on-resistance. These highly reliable products are qualified to meet the AEC-Q101 standard and are available as single N-channel, single P-channel, and dual-channel configurations. Across the portfolio, a wide variety of packages helps to satisfy the industry demand for miniaturization and thermal compliance.
One representative example is the RF7Gxxx and RF9Gxxx family of MOSFETs, which offer up to 12A of continuous drain current, 40V drain-to-source voltage, and only 30.3 milliohms of on-resistance. What makes this device unique, however, is the package design. These 2x2mm devices feature ROHM’s proprietary 125-micron step-cut process, creating a full wettable flank solder connection. This design improves the general quality and reliability of the solder joint while also allowing for post-process inspection. In addition, both F7 and F9 variants of the MOSFET provide two pin-out configurations, as Figure 3 shows. The F7 configuration, which is common in the industry, provides pin-for-pin compatibility as a drop-in replacement, while the design of the F9 maximizes safety by reducing the likelihood of a direct drain-source short. This is particularly important in electric vehicle applications, where this failure mode can lead to potentially catastrophic safety implications.
Figure 3. ROHM Offers 2-Pin Configurations – One for Compatibility and One for Safety.
This type of thoughtful package design is evident across ROHM’s entire MOSFET lineup, giving automotive designers the freedom to craft circuit solutions optimized for reliability, miniaturization, and thermal performance.
In addition to mid-power discrete MOSFETs, ROHM offers a subset of high-voltage models specifically tailored for automotive applications. These devices have been designed for drain-to-source switching voltages ranging from 250V to 800V, with continuous drain currents between 1A and 20A. Available in D2PAK and TO-252 packages, the most common application for such MOSFETs is in switching power supplies, especially in electric vehicles where common bus voltages are either 400VDC or 800VDC. Again, attempting to integrate a high-voltage switch such as this one into control circuitry would prove difficult and yield unacceptable inefficiency. A much better solution is to use discrete MOSFETs tailored to high-speed, high-voltage switching that are also packaged for thermal optimization, underscoring the need for continual advancement of such devices.
Application Examples
Discrete MOSFETs can be found in nearly every subsystem of modern vehicles. Applications where ROHM’s mid-power MOSFETs offer a unique advantage are in LED drivers for interior lighting, display backlights, and accent lighting, and in brushless DC motor drivers for seat control, mirror adjustment, and similar electromechanical systems.
The high level of refinement in today’s LED illumination requires the ability to offer dimming ratios that exceed 10,000:1 with no visible flicker at the lowest setting. To achieve this standard, ROHM designed a buck-boost converter with a novel low-duty-cycles switching scheme to eliminate flicker, as Figure 4 shows. Also visible is the discrete MOSFET controlled by the OUTL pin, which ultimately regulates the current to the LED array.
Figure 4. LED Driver with High Dimming Ratio Using an External Boost MOSFET
This MOSFET must be able to switch relatively large currents (on the order of 10A) with low on-resistance and high switching speeds in the smallest possible form factor. This is a perfect match for ROHM’s single-channel NFETs in the full wettable flank DFN package.
Similarly, controlling brushless DC motors is often achieved using discrete MOSFETs on each winding with a dedicated control IC, as shown in Figure 5. The six NFETs must also be able to handle moderate current levels while switching at fast PWM frequencies in a very small form factor.
Figure 5. BLDC Motor Driver Using Six Discrete MOSFETs
ROHM’s mid-power MOSFETs are an ideal candidate for this type of drive circuit, especially considering the importance of adequately switching the motor windings at high speed with tightly controlled overlap and relative timing.
Continual Advancements in Mid-Power MOSFETs
While high-power, high-speed GaN and SiC devices remain in the spotlight, there is still a vital need for mid-power discrete MOSFETs. As such, ROHM continues to invest in improving these devices with novel packaging solutions, high-voltage capability, and reductions in on-resistance. At the same time, qualifying them under rigorous automotive standards has yielded a portfolio of MOSFETs that is indispensable in the designer’s toolkit for producing reliable, high-performance vehicle systems.
To learn more, visit the ROHM website.
More Stories
Some Ways How Motorists End Up in Collisions at U-Turns
Maximise Margins with Proven PPF Tactics
Finding the Car Boot Release Button – Tips and Tricks