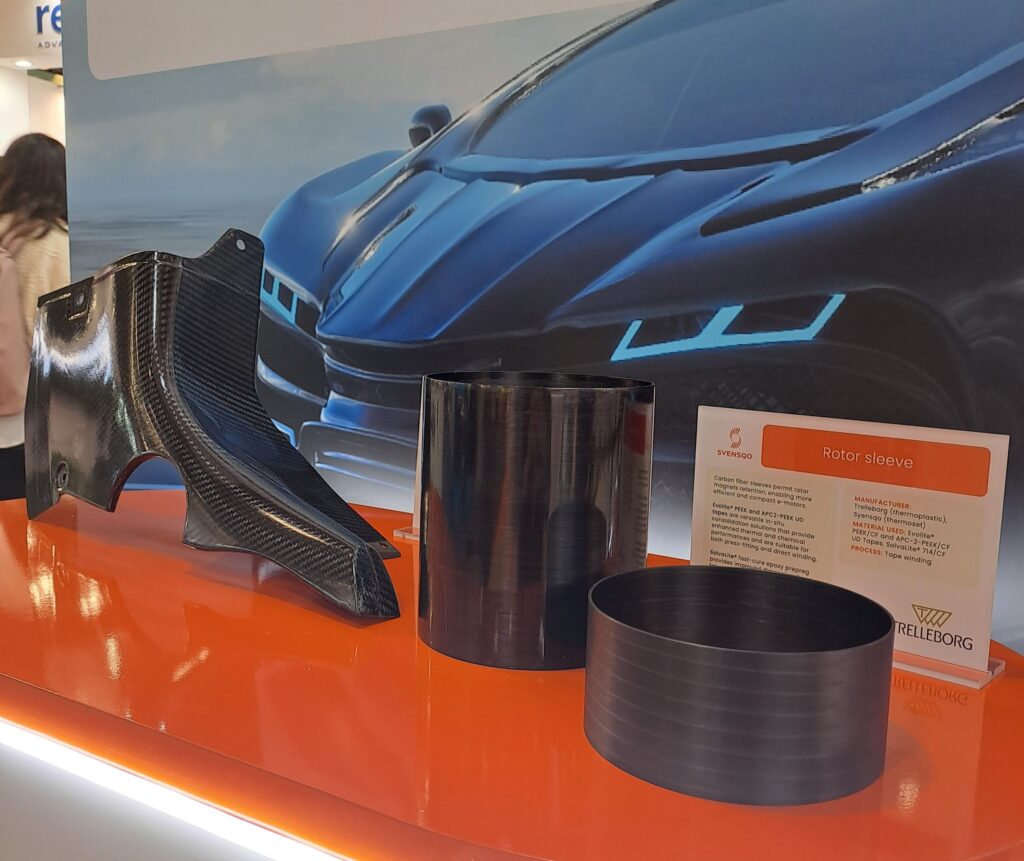
Carbon fiber rotor sleeves for more efficient and compact e-motors.
Legislation and changing consumer preferences driven by global warming are shaping a new generation of technological breakthroughs in the automotive industry.
With the rapid transition to electric vehicles, much of the attention is focused on batteries, which comprise around 40% of the price of a vehicle.
There are also safety concerns around lithium-ion batteries, which can ignite if not properly configured, managed, and isolated.
Automotive Industries (AI) asked Stefano Montani, Automotive Marketing Manager at Syensqo, how the company’s advances in materials are supporting electrification.
Montani: There are two important solutions.
For battery enclosures and module end plates, Solvalite® thermoset and Evolite® thermoplastic composites offer high specific strength and stiffness, superior flame resistance and durability.
One of the features of Solvalite® is its resistance to thermal runaway events.
It withstands 1,000 degrees Celsius for a minimum of five minutes.
This allows passengers enough time to exit the vehicle before it catches fire.
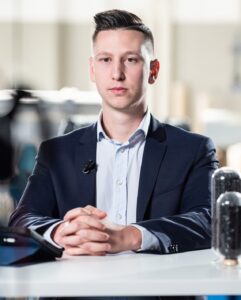
Syensqo’s materials for thermal runaway mitigation also include Ryton® PPS, XencorTM LFT, and Xydar® LCP, which ensure OEM compliance with crucial safety regulations.
The other solution is the rotor sleeve, a cage made with carbon fiber reinforced composites which is used to house the magnets within the rotor. This prevents the magnet from coming loose at high speeds.
AI: What are the latest Syensqo innovations for e-motor efficiency?
Montani: Thanks to the fact that we can offer both thermoplastic and thermoset materials, we are able to tailor our solution based on the need from the customer.
We traditionally have two product offerings.
SolvaLite® 714 is a new generation of unidirectional carbon-fiber and woven-fabric products pre-impregnated with SolvaLite® 714 epoxy resin. It cures in less than 10 minutes at 150 degrees C.
It can be wound into the shape of a sleeve and then press fitted on the rotor.
The second is a thermoplastic solution based on KetaSpire® PEEK, which is also wound, and press fitted, but without needing curing.
So, it offers a shorter cycle time.
But what makes this solution so important is that, in addition to allowing the rotor to spin faster, the topology of the rotor can be changed to allow optimum positioning of the magnets, which in turn reduces the total cost of the motor and the weight.
Syensqo offers multiple other material solutions for e-motors with renowned brands, including KetaSpire® PEEK, Torlon® PAI, Amodel® PPA, Ryton® PPS, Xydar® LCP, AjediumTM Films, XencorTM LFT, Tecnoflon® FKM, Fomblin® PFPE and Galden® PFPE.
AI: How do you address battery safety requirements?
Montani: Battery safety is one of the main discussion points with our customers. Thermal runaway, which occurs when an overheated cell ignites the entire battery is a big area of concern.
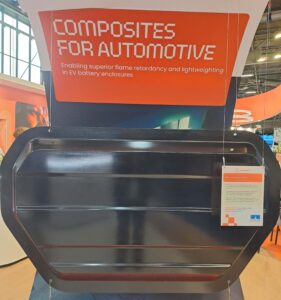
We want to address this issue with thermal epoxy prepreg that can contain the fire and avoid propagation for a certain time. It is not only a fire protection system, but also brings the mechanical performances which are typical of our composite products.
It can resist crash events, which are, of course, mandatory for battery systems.
We recently launched an innovative fast-curing epoxy prepreg system designed for a wide range of structural parts and reinforcements in premium battery electric vehicles. SolvaLite® 716 FR combines reliable EMI shielding performance and efficient processing of large volumes at high production rates with a significant lightweighting potential compared to existing solutions.
AI: What are the four critical areas of sustainability that Syensqo is focused on with its innovations?
Montani: To respond to the sustainability goals of the automotive industry, Syensqo has developed a new version of its flagship MTM® 49-3 resin, containing 30% bio-sourced monomers.
This new epoxy prepreg version will help OEMs and Tiers to reduce fossil depletion and meet their carbon neutrality goals, while ensuring the same high levels of quality, processability and mechanical performance as its original counterpart.
We are targeting the same applications as the flagship MTM® 49-3, which are structural parts and body panels.
Structural components include battery enclosures, chassis components and spoilers.
We also focus on sourcing more sustainable or recycled fibers.
For this we have two approaches.
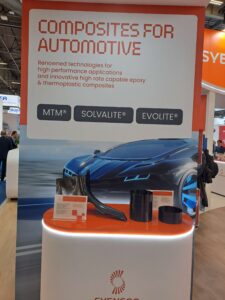
On one side, we are working and collaborating with Trillium to develop biosourced carbon fibers, which will significantly reduce the overall global warming potential (GWP) of the carbon reinforced composite.
On the other side, we are working on recycled fibers, and here, we are investigating how to get the best mechanical performances out of the recycled fiber.
AI: Please tell us more about the Syensqo approach to mass balance.
Montani: We are in a transition phase to a complete circular economy. We are leveraging the mass balance approach, as are many actors of the plastics industry. We are relying on independent certification bodies that allow us to track the flow of materials through the entire value chain and certify the content of circular and renewable feedstock in materials and end products.
Renewable resources derived from organic waste, crops or vegetable oils are used as feedstock in the very first steps of chemical production.
Through a verifiable bookkeeping system, the quantity of bio-based feedstock is allocated to specific downstream products.
This approach will help our customers to reach both their performance and sustainability goals.
AI: What is next for Syensqo?
Montani: We are intensifying our focus on advanced materials, encompassing specialty polymers and composites, as pivotal elements of our innovation strategy.
Our commitment to the electrification of the automotive powertrain is unwavering, driven by our conviction that the future belongs to electric vehicles.
More Stories
Some Ways How Motorists End Up in Collisions at U-Turns
Maximise Margins with Proven PPF Tactics
Finding the Car Boot Release Button – Tips and Tricks