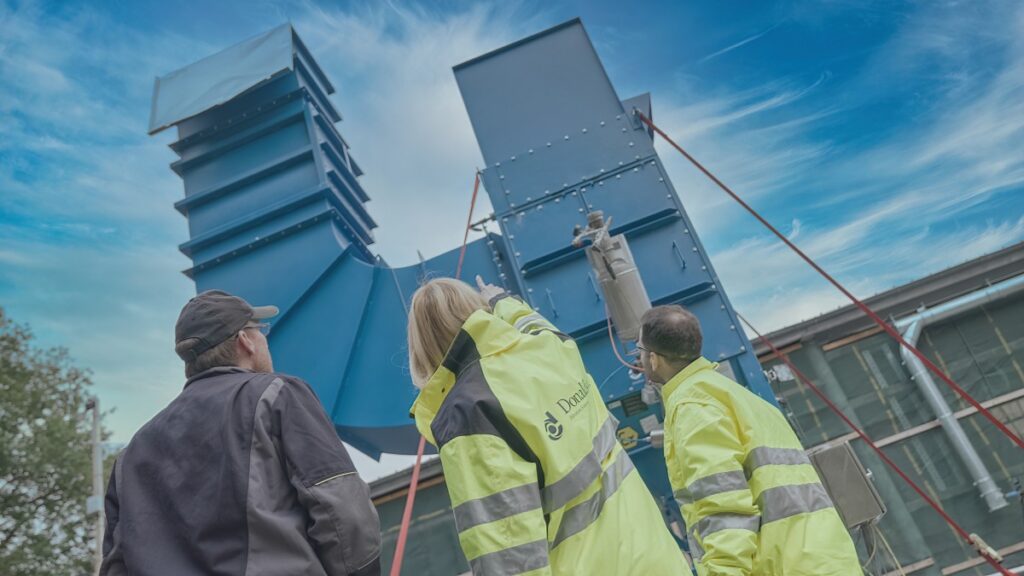
Mitigate Combustible Dust Fire and Explosion Risks
A well-designed, maintained, and operated dust collection system is an integral part of managing risks associated with combustible dust, as well as complying with laws and regulations.
Overview
Combustible dusts are fine dust particles that have the potential to catch fire and/or explode under certain circumstances. Examples of combustible dusts include most solid organic materials (e.g., sugar, flour, wood dust, etc.), metals (e.g., aluminum, steel dust, etc.), and more.
Many production facilities generate, handle, transport, process, or store materials that cause or become combustible dust. The airborne dust created by such processes is no mere housekeeping problem. Once those particles have settled in difficult-to-reach places throughout a site, any subsequent disturbance can produce a potentially explosive dust cloud – and when exposed to an ignition source, there is the potential for a fire or explosion. The creation of a risk mitigation plan is therefore necessary for most facilities.
It is essential for process owners to understand their dust hazards and ensure they manage combustion risks in their processes. The responsibility for evaluating and managing risks, creating an explosion protection mitigation plan, and complying with all applicable laws and regulations lies with the process owners, who know best their process, facility, and workers.
Strategy
Getting Started On Your Mitigation Strategy
Getting started on your combustible dust mitigation strategy can seem daunting. Each facility’s dust hazard analysis and eventual explosion mitigation plan will be unique, so there is no ‘one’ strategy that everyone should follow. Nonetheless, there are some basic steps* that can help you get started on your mitigation plan:
- Determine whether your dust is combustible — Start by assessing your dust and processes to determine whether your dust is combustible by sending a properly collected sample of your dust to a qualified lab. If it’s shown to be combustible, further tests will determine if it’s explosible, how quickly that can happen, and how much force it can carry.
- Understand the basics and examine your processes — Learn how fires and explosions can happen by understanding the fire triangle and explosion pentagon. To identify and manage one or more of the elements in the triangle to decrease fire and explosion risks, you should audit your process to identify where nuisance dusts are generated, released, or tend to accumulate.
These are often intake and mixing locations, bag dumps, and welding or cutting stations. In each location, analyze the production processes, housekeeping practices, dust control measures, and potential ignition sources present.
This information will help direct the selection of equipment needed to help mitigate these hazards.
- Know your laws and regulations — The process owner is responsible for the selection of the combustible material management strategy and to assure compliance with all applicable European Union directives, codes and standards.
Local, national, and international regulations, codes, and standards will impact your combustible dust mitigation strategy. Knowing the regulations that apply to your facility is critical, and you should always research the legal requirements in your area and develop a mitigation plan accordingly.
In Europe and many parts of the world, the two of the most commonly referenced standards related to the protection of employees and equipment from risks related to potentially explosive atmospheres are 1999/92/EC and 2014/34/EU (ATEX Directives), published by the European Union.
- Develop a mitigation plan — Once you understand your dust, analyzed your processes and facility, and studied the local laws and regulations, you can start developing your combustible dust risk mitigation plan.
The four key measures to consider when developing your plan are:
- Prevention measures (e.g., training employees, having equipment that has a separator device to remove materials that can ignite combustible materials, etc.)
- Dust control measures (e.g., having well-designed and operated dust collection systems, ensuring proper maintenance and housekeeping, etc.)
- Ignition control measures (e.g., implementing an ignition control plan such as grounding and bonding, minimizing static electrical charge, ensuring no improper mixture of metals, ‘no smoking’ signs, etc.)
- Protection measures (e.g., location of the dust collectors, dust collector safety features such as spark detection, maintenance of emergency exits, etc.)
One of the key steps in mitigating your explosion risk is selecting the right dust collection system.
As a manufacturer and supplier of industrial filtration solutions, we can assist process owners in the selection of filtration technologies. To provide this support, we need complete and accurate information on all potentially combustible contaminants and the fire and/or explosion mitigation plan(s) that you as a process owner intend to pursue. Once your risk mitigation plan is prepared, we can help review it and integrate our Donaldson equipment into your dust management strategy.
Solutions
Leveraging our extensive experience combined with our wide breadth of product offerings, we can help you with your combustible dust management and control strategy, by proposing dust collection solutions for your processes. Our solutions focus on helping you manage your combustible dust and the attendant risks in your process.
To help you manage combustible dust in your facility and to comply with the ATEX directives, Donaldson can deliver these four different types of dust collection systems, depending on your needs:
- Non-reinforced Unit — Either a standard dust collector or an earthed (grounded) unit if there is a safety concern regarding ignition sources.
- Reinforced Unit — Dust collector equipped with additional features, capable of containing a potential dust explosion within the unit, as specified.
- ATEX Unit — ATEX-certified dust collector that will be located in an ATEX zone (a potentially explosive atmosphere).
- Reinforced ATEX Unit — An ATEX-certified dust collector equipped with additional features, capable of containing a dust explosion within the unit which will be located in an ATEX zone.
More Stories
Mosaic Click board from MIKROE delivers global coverage multi-band and multi-constellation tracking ability
Current transducer from Danisense selected for DC charging station testing device demonstrator at TU Graz
New Click board from MIKROE helps develop and train ML models for vibration analysis