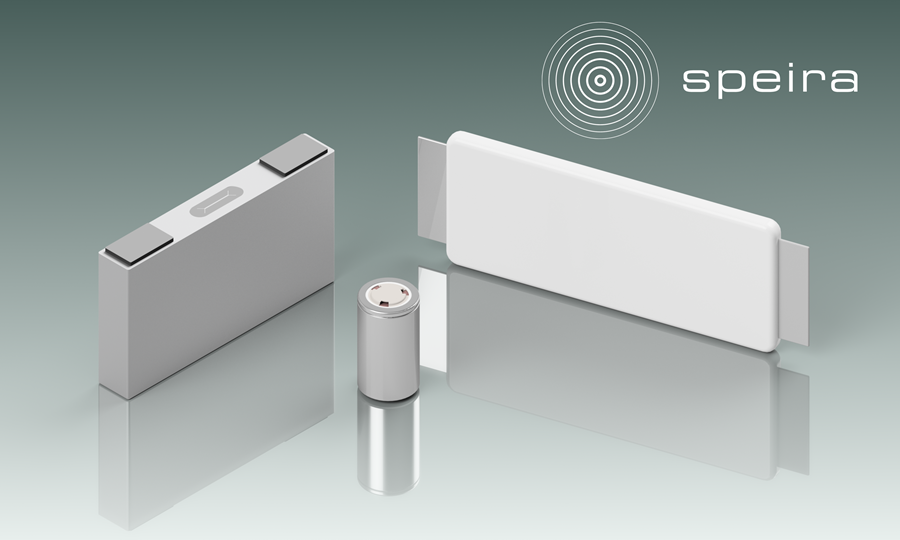
Aluminum properties such as high thermal and electrical conductivity, low density, high formability, strength and recyclability have established it as a material of choice for various components within high-energy lithium-ion battery (LIB) cells and battery packs.
Automotive Industries (AI) asked Dr. Hartmut Janssen, Head of New Business Development & Innovation at Speira, to provide us with some background into new developments.
Janssen: We started developing material for automotive batteries 10 to 12 years ago, and now offer a full portfolio for a range of applications from cell to pack level. We are convinced that the complexity of battery systems and aluminum products is tackled best in a process of cooperation and co-creation with OEMs and Tier 1 and Tier 2 suppliers. Hence, we set a big focus on partnerships, be they scientific partnerships or partnerships with our customers.
AI: What is your R&D focus?
Janssen: We are one of the biggest suppliers of material for prismatic housings and supply some of the world largest battery producers with our battery electrode foil. In addition, we have a range of material solutions covering cell housing, electrical conductors, heat exchangers and vehicle integration ready for market.
With cell housings, there is a divide in technology and corresponding material selection. For instance, pouch cells consist of laminated materials, which are a mix of plastics and aluminum. Prismatic cell technology uses only aluminum, while cylindrical batteries rely on nickel plated st
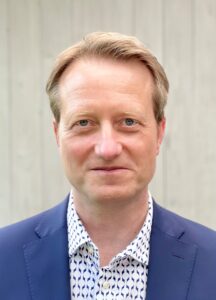
eel (NPS). We believe that cylindrical cells, and in particular large-format cylindrical cell like Tesla’s announced 4680 cell, would benefit from aluminum cell housings.
Tesla’s decision to move from the 2170 cell size to 4680 has led to reconsideration of cylindrical cells within the automotive industry, but it comes with challenges such as thermal management. From our perspective aluminum is a key element of the solution. That is why we commissioned a big study into the technology of aluminum for cylindrical cell housings, which was recently published as a white paper.
Larger LIB cell formats require significantly better heat conduction as well as reduced internal resistance. Therefore, the low thermal and electrical conductivity of nickel-plated steel become limiting factors. LIB cell housings made from aluminum alloys featuring about 4x higher electrical and about 3x higher thermal conductivity can help to overcome these challenges. We have developed material solutions for aluminum housings of cylindrical cells and evaluated the potential impact of NPS substitution in co-operation with universities, research institutes and industrial partners.
The next focus area is battery design concepts, but this depends on what the OEMs and battery manufacturers decide about switching from the current modular design to cell to pack technology. We have material solutions for all the emerging technology.
AI: What are the advantages of aluminum?
Janssen: High performance automotive batteries rely on optimization at every level, from inside the cell to the battery pack. Some components are structural and hence require mechanical properties, while others require certain chemical and physical properties. It’s the versatility of aluminum which makes it appealing for cell design specialists as well as mechanical and electrical engineers who are pushing the limits of battery technology.
What has been evident from the first EV generation is the weight-saving potential of aluminum in battery packs and crash structures. Reducing weight to increase the range of electric vehicles was the starting point for greater use of aluminum in vehicles.
However, diving deeper into the pack and the cell reveals aluminum materials provide additional characteristics. For instance, aluminum is widely used for electrical connection of the individual battery cells due to its excellent electrical qualities. While copper is a better conductor, aluminum provides the combination of lower weight combined with good electrical and thermal conductance. This is particularly important for fast charging. Aluminum also provides the perfect combination of electric and thermal conductivity for other conductor applications and heat exchangers.
Another interesting example is the prismatic cell housing, which demands extreme formability during production and mechanical strength and electrolyte compatibility in service. In addition, reliable and fast laser welding is key for product quality and productivity.
On top this the next market trend consists in circularity and sustainability of batteries, which comes along with increased use of recycled material, and this is where aluminum has a number of advantages.
AI: Is this why you are acquiring Real Alloy Europe?
Janssen: Real Alloy is the biggest third-party recycler in Europe. The acquisition will enable us to close the loops to help our customers to further decarbonize their manufacturing activities. Real Alloy’s employees also add the right knowledge and expertise on top of the production capacity needed.
AI: How does this match the latest European trends in EV development?
Janssen: The market is really driven by governments. So, there is a strong push for e-mobility, which will see it being the leading technology in future. Also, the latest statistics show one in three vehicles in Europe is now electric. In addition, EU legislation and customer expectations are challenging the industry to be more sustainable by using green energy and reusing or recycling. These trends match Speira’s ambitions, as we are committed to producing low-carbon aluminum and creating closed loop material flow.
AI: How is Speira responding to the market needs?
Janssen: We have been monitoring developments and positioning ourselves since we saw the first drive towards e-mobility. There are two different focus areas. One is the classic automotive applications such as the body and frame. In this sector, we don’t see much change.
The difference lies in battery integration. We have differentiated between the battery technology and the integration of batteries into the vehicle structure in the form of what we call battery boxes.
For battery boxes, the focus is crash performance and thermal management. Modern battery systems provide optimal performance and service life between approximately 20°C and 40°C. Thermal management systems keep the batteries in this range. Speira materials for heat exchangers in battery applications guarantee efficient thermal management, whether it’s during fast charging or out on the road.tter
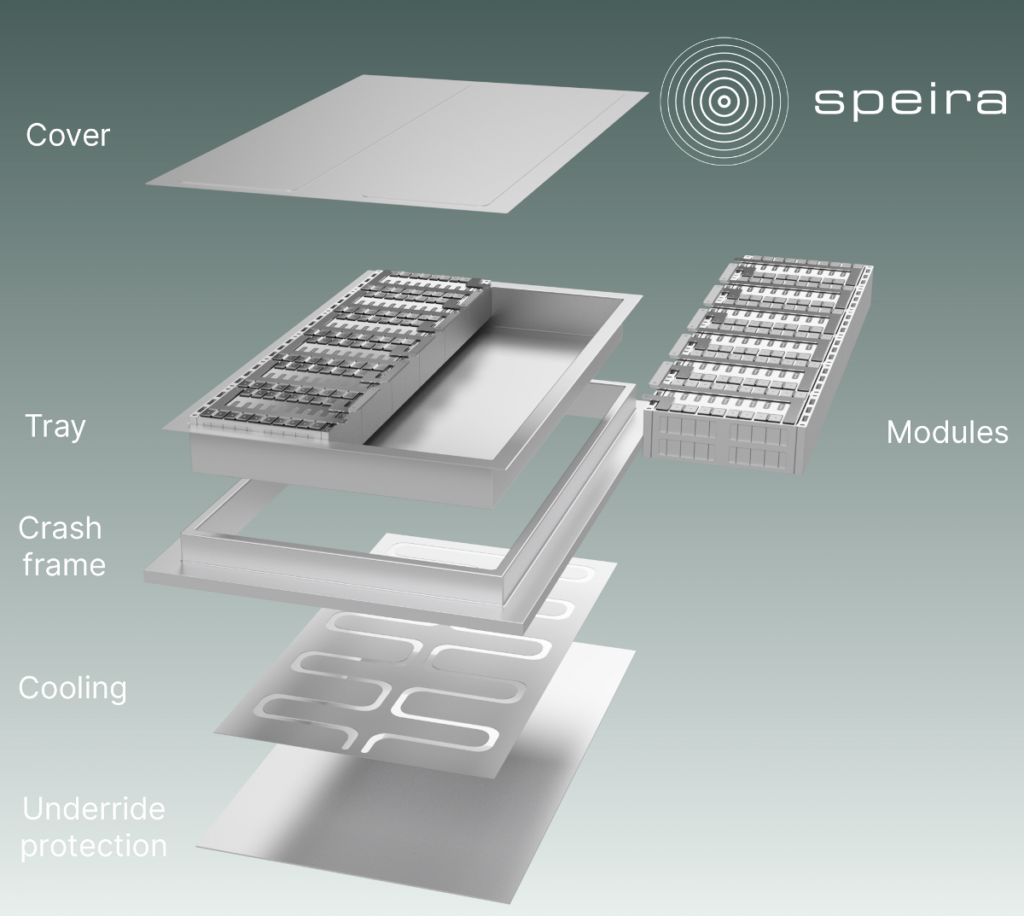
At cell and module level we have developed new materials like electrode foils, which serve as a carrier material for the active mass of a lithium-ion battery, connector materials, solutions for cell and module housings etc. Each of these developments has been guided by in-depth evaluation of the application and close cooperation with both industrial and scientific partners.
AI: What’s next for Speira?
Janssen: Mobility and battery technology represent the biggest technological transformation we have seen over the past 20 to 30 years. The next big challenge is energy in general, which will be with us for a number of years to come.
Do we still rely on oil and gas? How do we drive renewables? Does wind or solar technology old the greatest promise? Or is it liquid natural gas? Aluminum is used in all these applications.
Let’s not forget that we are living in a world where we currently face a two-degree Celsius increase in average temperatures. The Paris agreement aims to reduce this to 1.5 degrees. So, we are looking at the big picture where we are working very hard to provide solutions that support decarbonization to slow global warming. We want to do our part to contribute to meeting the goals of the Paris agreements as a responsible corporate citizen.
More Stories
With the right people and portfolio, Celanese is ready for present and future EV developments
BASF – Innovative chemistry for the mobility of the future
Hexagon Approach to New Product Development in EVs: Navigating Challenges and Innovations