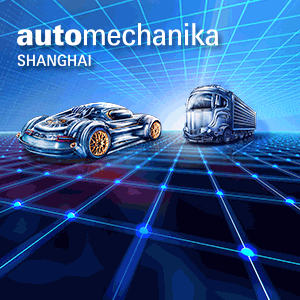
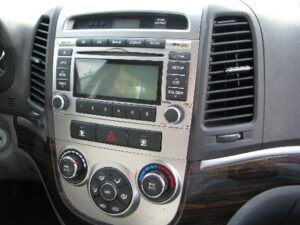
It should be no surprise that supply chains are out of balance, with the Covid health crisis largely to blame for the current volatility.
Recently I have had folks ask me if the automotive chip shortage is the fault of the automakers, and more recently still, I found an article espousing the same.
There seems to be a suggestion that an original equipment manufacturer (OEM) which does not adopt the latest integrated circuit – the smallest die for the integrated circuit (IC) – is part of the problem.
We reference that article in the content below.
It is seldom productive to blame the customer for our problems. The customer is purchasing something you provide. They are at least, in part, the reason you exist (if we look at singular customer or market segment).
To me this seems obvious, but maybe it is not. For example, I do not need to update my amp just because there is a newer model made with new ICs.
Why should automotive manufactures even care about Moore’s Law?
Moore’s law is a term used to refer to the observation made by Gordon Moore in 1965 that the number of transistors in a dense integrated circuit (IC) doubles about every two years.
It is more likely the events of the last two years, Covid, disruption of the electrical grid in Texas and other disasters that have caused the shortage.
In the first half of the year the primary cause of disruption was the shortage of front-end wafer fabrication for microcontrollers (MCU). This was the particular supply chain that was dented by the ice storm in Texas and the fire at the Renesas Naka 3 facility in Japan.
There are many reasons why OEMs do not update the silicon in the vehicle.
Performance not Technology
Customers buy our product because if fills a need or solves a problem.
In general, the automotive industry does not care about the silicon, or the manufacturing processes. In very few cases does the size of the IC matter. For the most part, the customer wants parts that work reliably and predictably. The OEMs are also sensitive the cost and change to these circuits over time. We will show why later in this article.
But in the interim, it was suddenly apparent that Moore’s Law of increasing miniaturization missed the boat when it came to the automotive industry. The many dozens of chips in structures from brake systems to airbag controls were revealed as chokepoints where obsolete technologies reigned supreme. The essentially ancient chips, comparatively simple transistors for the day, are far too primitive to be used in high-tech devices such as today’s smartphones and televisions.
What does it take to bring an ECU to market?
The supply chain for automotive products is complex.
There are multiple tiered suppliers, the material is required to be coordinated to be able to build the final product, and any change in one component, has an impact on the other components that are delivered.
These components often originate from around the world which does not make this coordination requirement easier.
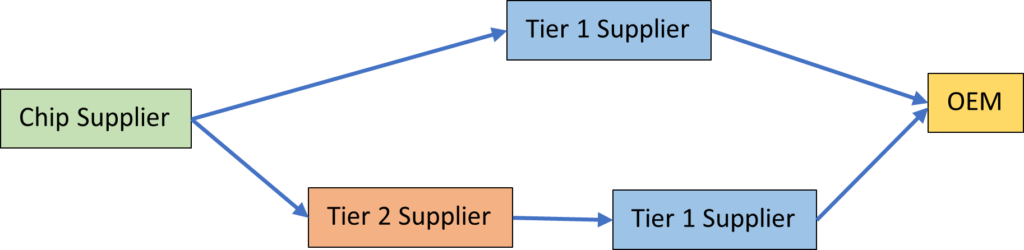
Development
Developing vehicles is complex. It is not just the vehicle, there is complexity in the supply chain system as well. To bring a product to the vehicle is essentially the coordinated efforts of the product development and the development of the supply chain simultaneously.
Any proposed change to the product or to the supply chain will come at varying degrees of expense, time, and risks.
A Short Tale
Here is an example of connecting new product development with integrated circuit development:
I once worked at an Original Equipment Manufacturer (OEM} and we were developing an Electronic Control Unit (ECU). We could use an integrated circuit that was off the shelf, but there was a better solution in pipeline at the integrated circuit (IC) supplier. Nearing the end of the project, the integrated circuit supplier reports it is terminating the development of this specific IC.
The OEM has spent tooling money, time and testing of the various levels of the product leading up to the production version of the product. This requires rework, retooling, and retesting, extending the project will beyond the expected or desired launch date.
The project extended for months longer, with increased costs.
I know this is anecdotal, but still today, I manage projects that develop electronic products for vehicles. The IC shortage impacts these projects. Additionally, I hear other project managers discussing the impact on their projects are impacted as IC development time slips from an original schedule. Specifically, the IC development is late.
Test and Verification
The development of the product consists of simulations and building prototype parts as close to the production version (in hardware) as possible.
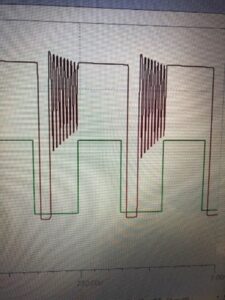
There are multiple iterations that increment the product (hardware or software) until the product is ready for launch. This requires stability in the IC (see A Short Tale). Prototype parts too far removed from the production intent will necessitate retesting, or accepting risk associated with this uncertainty.
Some of the testing can be expensive outside labs, for example electromagnetic compatibility, susceptibility and radiated. This testing uses expensive equipment that the OEM will likely not have, and the product might require certification depending upon the nature of the product. For example, a change in the radio, is not as scrutinized as the ABS, and airbags. The way the products are handled, depend upon the consequences of failure in that component.
Change Existing ECUs
Modern vehicles consist of a collection of ECUs, making a change to one of the components will often require some component and systems level testing. Let’s look at this from an existing platform and the IC supplier wishing the vehicle OEM to adopt the new integrated circuit for some of the ECUs. This will take resources from present development effort.
To change the product to this new IC will require the Tier 1 supplier, to redesign the product with the new one.
The change from the present IC to the updated IC might be significant the existing design (printed circuit board and more), meaning, retooling the existing design, set up the manufacturing line, qualify the part (test and verification), and validate the product within the entire vehicle system.
The latter may be multiple platforms with which will require testing not just on the single platform, but many others with combinations of different ECUs.
IC Grades
From personal experience, the parts employed in automotive applications are not the same as the commercial grade. The chip set that goes into a cell phone is not often the same that goes into automotive applications due to thermal considerations on the product.
The issue is that reliability is of enormous concern to automakers. The vast majority of chip-dependent systems in cars are crucial to their safety, and those chips are required to perform at peak efficiency without regard to conditions such as temperature, humidity, microscopic dirt and hellish vibration.
Effort over the Years
The automotive industry has invested heavily over the decades to control the cost and constantly improve the quality and reliability of the product to the customer.
To achieve this has meant controlled changes to the product, copious amount of testing of the product through the product development, and attention to the details in the manufacturing process.
This did not happen overnight, and it came at significant cost. The complexity of the product, and the supply chain necessitates we think things through and experiment.
That is how the automotive industry has gotten where it has over the years.
Rapid change in the environment can require a change in our method or typical response. However, that does not mean responding ad-hoc.
More Stories
Some Ways How Motorists End Up in Collisions at U-Turns
Maximise Margins with Proven PPF Tactics
Finding the Car Boot Release Button – Tips and Tricks