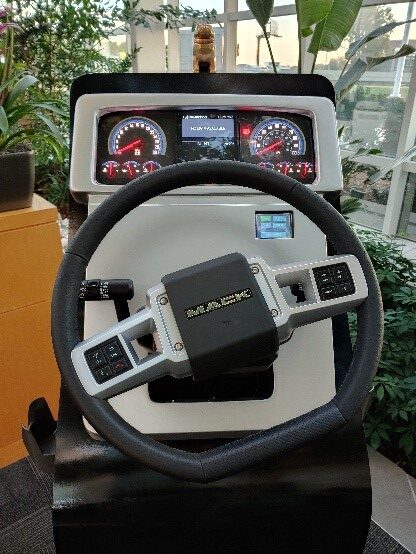
In this column Jon Quigley looks at some of the main technological changes he has seen during his working career.
ABS Tractor Trailer Communication
I have been in product development since 1990. My first automotive product development experienced happened at Vehicle Enhancement Systems Inc.
There I worked on the precursor to what would become the power line carrier ABS communication from the trailer to the tractor. This system would communicate the state of the trailer ABS over this power line carrier component, and is defined in SAE J2497_201207. It is amazing to see how things have advanced over the years.
Driver Displays
Another product I worked on was a heads-up display for a truck system. I designed the power conditioning circuitry. It takes considerable current (amperes) to project vehicle status onto the collector of the heads-up display.
For heavy trucks, there are conditions where the 12-volt electrical system can generate transients above 100 volts.
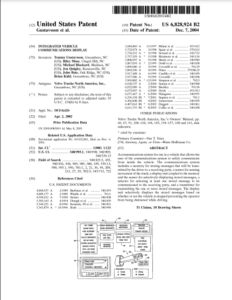
The products connected to this electrical system must be able to withstand a transient of this level. I used a FET to open circuit the supply voltage to the systems when that supply voltage exceeded a certain level. Today there is little thought of heads-up displays. The cost of flat panel displays is such that the heads-up display solution largely became irrelevant.
Air Gauges
Years ago, I worked at a heavy vehicle development and manufacturing company.
Heavy trucks still use air for the suspension components and brakes. It was also used for the pressure gauges in the cab. The driver should know the amount of air pressure in the brake tanks.
The primary and secondary brakes gauges are legally mandated. There is a third pressure that is optional and that is the application pressure.
Originally, these gauges were bourdon tube air gauges, that is not electrical but a tube routed air into the back of the gauge. There were manufacturing and reliability issues with these old gauges, but to be able to sense was expensive.
The advancement of technology eventually produced a reliable and cost-effective solution to sensing pressure and provide an electrical signal rather than air. The introduction of this pressure sensor improved instrument cluster reliability and made the interior of the vehicle quieter as there were no air hoses to leak or conduct noises from the external of the cab to the interior.
Telemetry Systems
When I started working in automotive product development, there were no telematics systems.
Initially, these systems were for security and used in the event of an accident to initiate the responders.
Then we saw these on vehicles as logistic (map features) systems. I worked at a company that developed other uses for these systems that include geofencing (ensuring a construction vehicle is not taken out of certain boundaries.
These systems are also part of maintenance planning. The vehicle self-diagnoses the state and will record information of performance drop-offs, or trends that indicated a component is on the way to failure.
The telemetry system broadcasts this to the fleet owner or repair shop, to allow them to order the parts and plan for the repair of the ailing system. These systems are also used for software updates to the vehicle without having to take the vehicle to the shop.
Brake Systems
In my career, I was also part of exploring the ability to detect brake stroke travel on trailers used in big rig shipping. These brakes are actuated by air, or more accurately, kept from actuating because of air. This is contrary to what you may have heard before, and the song by Jerry Reed in the Smokey and the Bandit movie, The Legend.
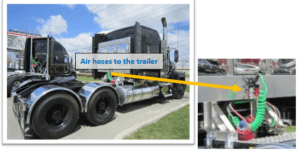
I like Jerry Reed, the song is good, and who am I to critique the writer’s creative license. To be clear, when you lose brake air, the brakes are entirely engaged. It has to be that way for system safety reasons. If you lose air, you should not lose the brakes.
We explored developing a product that would measure the brake strokes of the trailer. This indicated the state of the brake lining. The further the travel, the more of the brake lining has been worn, and at some point, the brakes become unsafe.
At that time finding an acceptable technical solution, was difficult.
Specifically, the sensitivity and range of travel made them cost-prohibitive. We worked with reed switches, and magnets but could not reliably monitor the stroke cost-effectively. Another example of how things have changed.
These brake systems exist today. TE Connectivity has a wide range of precision position detecting components, for example, the T40. Magnets are lower cost for stronger field strengths. We can expect to see more application as the vehicle becomes increasingly electrified and increasing reduction of driver cognitive load and automated controls.
Conclusion
It is funny when you are working on developing these new things, you do not necessarily notice the incremental technical improvements or changes that increase the range of product possibilities. I worked with an engineer, I believe his name was Rick B., that used to say the things we work on today, will be obsolete in a few years. The march of technology seems to be continuous. Maybe that is not a bad thing.
More Stories
5 Conclusions One Can Make by Analyzing Car Accident Statistics
Some Ways How Motorists End Up in Collisions at U-Turns
Maximise Margins with Proven PPF Tactics