New energy vehicles (NEV) present a range of new design challenges for developers and suppliers of noise damping materials and solutions.
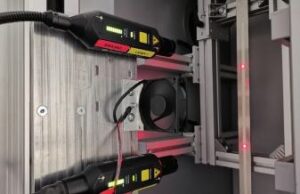
Lightweight multilayer products are required to build lighter vehicles without compromising acoustic comfort. Noises such as road-tire interaction, which is largely muffled by internal combustion engines, become much more intrusive in a quiet, electrically powered car. New composite materials and manufacturing techniques used in electric vehicles also introduce their own frequencies of structure-borne noises. One of the companies in the technological lead in this field is Sika, which has won multiple awards from OEMs for the quality and consistency of its products.
Automotive Industries (AI) asked Bernd Fuhrmann. Global Product Manager Damping & Head of Acoustic Center, Sika Automotive, to outline some of the specific challenges in damping electric vehicle noise.
Fuhrmann: The excitation characteristic shifts from the low[1]frequency combustion sounds of the internal combustion engine (ICE) to specific noise and vibration signature of the electric motor. Road and wind noise is not affected, but high-frequency vibration sources from the electrical system and drivetrain become more prominent, especially in the critical frequency range between 500 Hz and 2500 Hz.
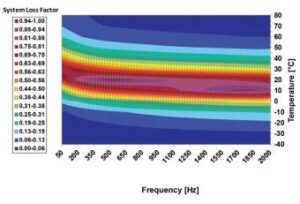
Additionally, the integration of the batteries as a vital structural component of car body design increases the overall body stiffness. The change shifts the structural resonance frequencies, which are higher than those of conventional ICE body design, hence the acoustic materials must be engineered to address this change.
AI: What products has Sika developed for electric vehicles?
Fuhrmann: Sika has developed multi-layer damping systems to address a wide frequency range. Some Sika solutions have up to four times higher damping properties than lower performing damping materials such as monolayer, magnetic bitumen or sprayable products of comparable weight. One aspect of electric vehicles that is often overlooked is that they tend to be heavier than their conventionally powered counterparts, mainly due to the weight of the battery system. When implementing damping solutions, low weight options should be considered in order to lower overall vehicle mass and ease range issue. Within Sika damping portfolio, there are very low weight systems such as SikaDamp-760 Ultralight, which provides twice as much damping performance at 25% of the weight when compared to monolayer damper with similar performance.
AI: How important is it to target noise as close to the source as possible?
Fuhrmann: At Sika we believe that it is the most efficient and least expensive approach to reduce interior noise. The vehicle body itself is the biggest radiator of airborne noise in the vehicle. When more vibrational energy is input to vehicle body, more airborne noise will be radiated. Highly effective damping solutions can greatly attenuate the vibrational energy leading to the lower airborne noise. Conversely if one chooses to use low performing damping materials or minimalistic damping packages, the resulting increased level of airborne noise will have to be countered with more interior NVH measures such as heavy carpet layers with thick foam absorbers or synthetic fleeces. These treatments would add additional weight and cost to the vehicle.
AI: Are your solutions saving weight?
Fuhrmann: Sika has a wide range of damping products within its portfolio. SikaDamp high performance constrained
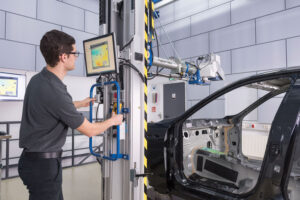
layer damping (CLD) system is engineered to reduce the overall damping package weight while significantly increasing acoustic performance. Consequently, there is a potential to double the weight saving. First, one can replace the conventional monolayer damping systems one-to-one with the CLD systems where weight saving of up to 50% is possible. Second, with the higher performance of the CLDs, it is theoretically possible to redesign the damping package to reduce material usage and still accomplish the same overall acoustic performance. Besides the material approach, Sika also follows a very straight forward philosophy: the right material with the right design at the right place. We design parts to avoid oversized layouts and to further reduce weight while addressing vibrational hotspots with appropriate material choice. Compared to the sprayable damper which is very limited in scaling performance, our approach opens a versatile and flexible layout of the acoustical damping package.
AI: What research and development and testing back your products?
Fuhrmann: The Sika development process incorporates various methods and tools for characterizing and quantifying material properties including mechanical and acoustical characteristics. We can respond in all customer regions, backed by R&D centers located all over the world, to meet customer specifications, regulatory requirements and sustainability targets. With a focus on holistic material characterization, Sika has also developed a method for measuring high frequency performance of the products, enabling us to compare acoustical performance on a much more detailed level. AI: What is the Optical determination of Loss Factor (OLF)? Fuhrmann: The OLF method was developed by Sika in order to overcome the restriction of material characterization methods, commonly used by the OEM’s acoustic engineers. These methods do not provide sufficient information about the loss factors of a damping material in either high frequencies or in the case of high loss factors. The OLF results represent the composite loss factors in a 3-dimensional, graphic way. The color-coded loss factor is plotted over the frequency band and temperature range. Beyond this, Sika’s worldwide acoustic development centers can also conduct laser vibrometer tests, which enable us to directly evaluate how damping materials can perform when applied on vehicle bodies-in-white.
More Stories
Some Ways How Motorists End Up in Collisions at U-Turns
Maximise Margins with Proven PPF Tactics
Finding the Car Boot Release Button – Tips and Tricks