OEMs and Tiers are looking for partnerships with aluminum producers in the quest for lighter components to extend the range of electric vehicles and to reduce the carbon footprint of internal combustion-driven vehicles.
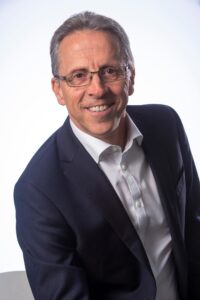
The carbon footprint starts with the production of components. Aluminum producer Hydro has certified all 42 of its extrusion operations in Europe against the Aluminum Stewardship Initiative (ASI) performance standard, which recognizes the responsible production, sourcing and stewardship of aluminum. “For our automotive customers that becomes a hygiene factor. You have to satisfy them that you have a sustainable sourcing policy to do the right thing and deliver on their expectations,” says Paul Warton, EVP Hydro Extrusions.
Automotive Industries (AI) spoke to Paul Warton and Piotr Chmielewski, VP Automotive for the Extrusion Europe business unit.
AI: What extruded aluminum components is Hydro supplying to its automotive customers?
Warton: Hydro Extrusions is very strong in crash management parts – both front and rear. Crash components are also needed for electric vehicles – side sills for example, battery box structures and increasingly on the main structure of the car. Our range includes products like struts and brackets – where aluminum is replacing steel. We also do ABS blocks, suspension parts, and anti- vibration components. In roof rails and trim, we are the clear Tier 1 leader in supply to OEMs. The rest of the business is in precision tubing which we supply again at Tier 1 level. One of the more interesting components is HV cabling and busbars, which are fitted between the
charger units and the energy source. This technology is helping aluminum to replace copper as a conductor.
Chmielewski: We are really strong in window trims, which we supply as a Tier 1. They are what we describe as our “jewelry niche product” because they are so visible. But, our main focus is on structural components.
AI: Do you see any change in the way you work with OEMs and Tier 1s?
Warton: There is always the fine line between going direct to OEMs and competing with our Tier 1 customers. It needs to be complementary. Our strengths include innovation and technology; product design and crash performance. The approach is to first see which Tier 1 supplier or suppliers we can work with. We follow the same
approach in Europe, the United States and China. There are some areas where the landscape is such that it is best that we work with OEMs on the design, development, simulation, testing and prototyping before serial production. Chmielewski: We are very careful about balancing our relationships with Tier 1s and OEMs. When working directly with an OEM the biggest advantage is that you are given access to strategic intelligence, which often leads to innovation and technology priorities.
AI: What innovations are you working on with regards to production and production technology?
Warton: The first priority is to ensure that you have your innovation and technology research close to your customers. Our hubs are in Finspång, Sweden and Troy, USA. We have other laboratories with similar competences close to the OEMs in Asia, South America, North America and Europe. Our OEM and Tier 1 customers expect us to be a material development partner, and not just an aluminum extruder or billet caster.In order to meet the challenge of replacing steel with aluminum components, OEMs need a material development partner which becomes part of the development team. This is particularly important in crash management systems. As important is the development of components which can be manufactured in serial volumes through casting and extrusion processes. Hydro is adding value by supplying fully finished parts.
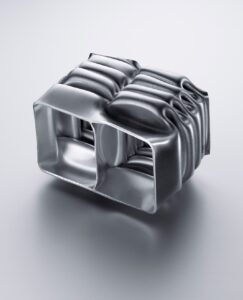
Chmielewski: It is quite amazing how the performance of a component or a system is dependent on each level of this process. So, it’s not just casting and alloys. It’s not just the extrusion process. It’s not just the end-fabricated part. You have to come up with the best solution at each step to solve the customer’s challenges.
AI: And in terms of new materials / aluminum alloys?
Warton: Our specialty is crash alloys, as well as high strength alloys of 320 MPa (megapascal) with really complex shapes. We have a full-size billet casting and an extrusion press for rapid prototyping at the I&T center in Sweden. Much progress has been made in the field of friction stir welding. This is linked to e-mobility where it
is used to connect components like battery frames to the floors. In e-mobility we see that the focus is moving away from use-phase emissions to production using low-carbon materials.
AI: How is Hydro positioned in the marketplace at present?
Warton: We are positioned as the firstchoice material development partner. Hydro is also very well positioned on the whole lightweighting, lower carbon emissions sustainability agenda.
AI: How are you keeping up with the growth in e-mobility?
Chmielewski: We have enjoyed significant growth in this market, supplying Tier 1s and OEMs with battery frames and other components linked to e-mobility. Strategically, we are positioning ourselves to potentially add more capacity in the European market. This is where we see aluminum extrusion consumption growing from 400,000 to 600,000 – 700,000 tons by 2025. Covid-19 has not had much impact on these projections be cause of the growth in e-mobility. There is also a growing demand for scrap recycling from the end-of-life vehicles – using standard alloys, simpler deconstruction and then of course moving that metal back into the recycling loop.
AI: What about your own carbon footprint?
Warton: Hydro offers two of the most sustainable aluminum alloys available on the market, the certified low-carbon products Hydro REDUXA and Hydro CIRCAL. The first guarantees a maximum carbon footprint of 4 kg CO2 per kg aluminum during its life cycle, while Hydro CIRCAL contains a minimum 75% postconsumer recycled content.
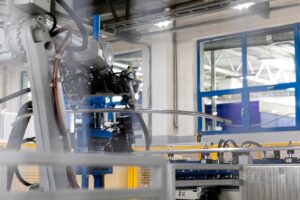
AI: What is next for Hydro?
Warton: We will retain our position as the preferred partner in the automotive aluminum space. It is going to be important that long-term partnerships are created in this area. Extrusions have proved to be the material of choice to solve problems in the design of components for structural members, crash management, high-voltage cables, air conditioning, roof track and decorative parts. It is important to be seen not just as a supplier, but also as a development partner with the right solutions. At
the same time, we need to be sustainable by minimizing CO2 emissions and recycling components from end-of-life vehicles. Despite the many global economic challenges, vehicles are still selling. We see growing use of aluminum in trucks and SUVs, with the fastest uptake in the high-end segment. So, you have market growth, then you’ve got the material substitution where we are able to demonstrate that aluminum can save weight by replacing steel and also achieve often better performance,
especially in the safety-critical areas. And then you’ve got what I see as the competitive strength of Hydro Extrusions as a supplier of raw materials. This will help us to
grow our market share.
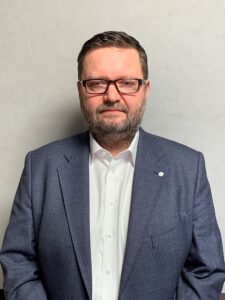
More Stories
LED Lighting for Heavy-Duty Applications: Durability, Efficiency, and Versatility
Celanese Materials Shine in Multiple Category Winners at 2024 SPE Automotive Innovation Awards
New future-ready single-slot PXIe controller for high-performance T&M applications from Pickering Interfaces