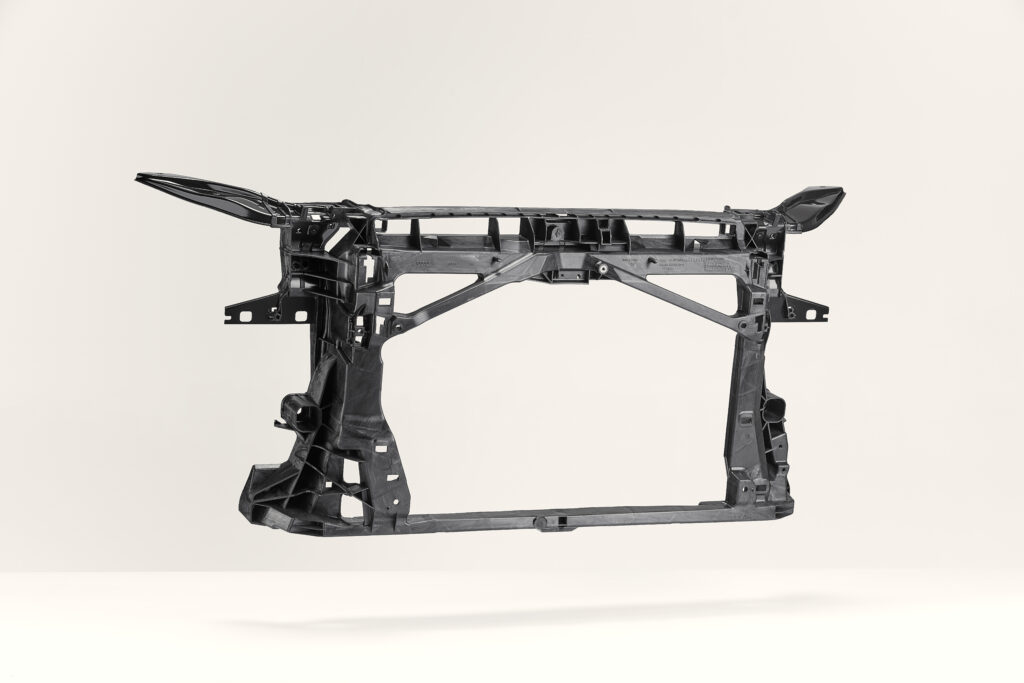
OEM: Audi Application: Frontend Car: Q7 Product: Fibremod GB477HP

Ongoing investment and expansion program by one of the world’s leading providers of polyolefin plastic (PP) materials is ensuring that there is sufficient supply to meet a growing demand by automotive manufacturers.
The Fibremod™ carbon and glass fiber-reinforced polypropylene (PP) technology is now being produced locally for the North American automotive market by the patent holder and manufacturer Borealis.
This follows the coming on stream of a new Borealis polypropylene (PP) compounding plant in Taylorsville, North Carolina. It added 30,000 tons to the annual global PP compounding capacity, and can also provide thermoplastic polyolefin (TPO) and short glass fiber (SGF) compounds. Located in the booming south-eastern region of the US, the site was designed to fulfil the growing needs of Automotive OEMs and Tier 1 customers for advanced PP solutions.
The 50,000 square foot (4,645 m2) facility offers potential for expansion in line with projected mid-term increases in customer demand, according to the company.
The new plant complements the Borealis compounding location in Port Murray, New Jersey, which was expanded in 2016 with the addition of a PP compound line. The line added capacity for the production of PP TPO compounds. The site produces compounds for use in energy transmission applications, including flame retardant wire and automotive applications.
Production capacity in the Americas is further supported by the recent expansion of the Borealis plant in Itatiba, Brazil. This included an additional production building, two PP compounding extruders, blending and raw material silos, warehouse facilities and a bagging line. Itatiba produces high performance, highquality PP compounds for the South American operations of leading automotive tiers and OEM partners.
Automotive Industries (AI) asked Michael Shoemaker, Marketing and Technical Director at Borealis, what is driving the demand for PP compounds.
Shoemaker: PP compounds are enablers for change in a future in which electrification, autonomous vehicles, and Mobility as a Service may prevail. They will remain indispensable when it comes to lightweighting, design freedom, and flexibility for future vehicles. Our own global expansion efforts are focused on supporting the industry in this period of rapid transformation.
AI: What is your expansion strategy?
Shoemaker: As global players in the automotive industry, our constant focus is on innovative products that address the increasingly demanding challenges of our customers. We are proud to be a trusted industry partner capable of offering a growing number of applications promoting lightweight construction and enhanced surface aesthetics. We are also connecting our global network by expanding capacity, hiring local teams, and adapting to regional business cultures while preserving our focus on safety and innovation.
AI: Please tell us more about the Fibremod™ range.
Shoemaker: The Fibremod™ family of products enables automotive manufacturers to achieve weight-saving and process cost-saving targets as substitutes for metal and engineered plastic components. Replacing these parts with energy-efficient and lighter weight PP grades leads to improved fuel economy and lower CO2 emissions.
Fibremod™ It is available in both short and long-fiber compounds.
Short glass fiber reinforced polypropylene (PP-SGF) products are usually converted to parts using various injection molding technologies, including complex processes such as injection compression molding or injection foam molding.
Long glass fiber reinforced polypropylene (PP-LGF) is a group of glass fiber reinforced products which are produced by pultrusion to achieve increased fiber length in both pellets and final parts.
Fibremod™ products also support energy efficiency in production by reducing process temperatures and energy requirements compared with alternative solutions such as polyamide (PA).
More Stories
Some Ways How Motorists End Up in Collisions at U-Turns
Maximise Margins with Proven PPF Tactics
Finding the Car Boot Release Button – Tips and Tricks