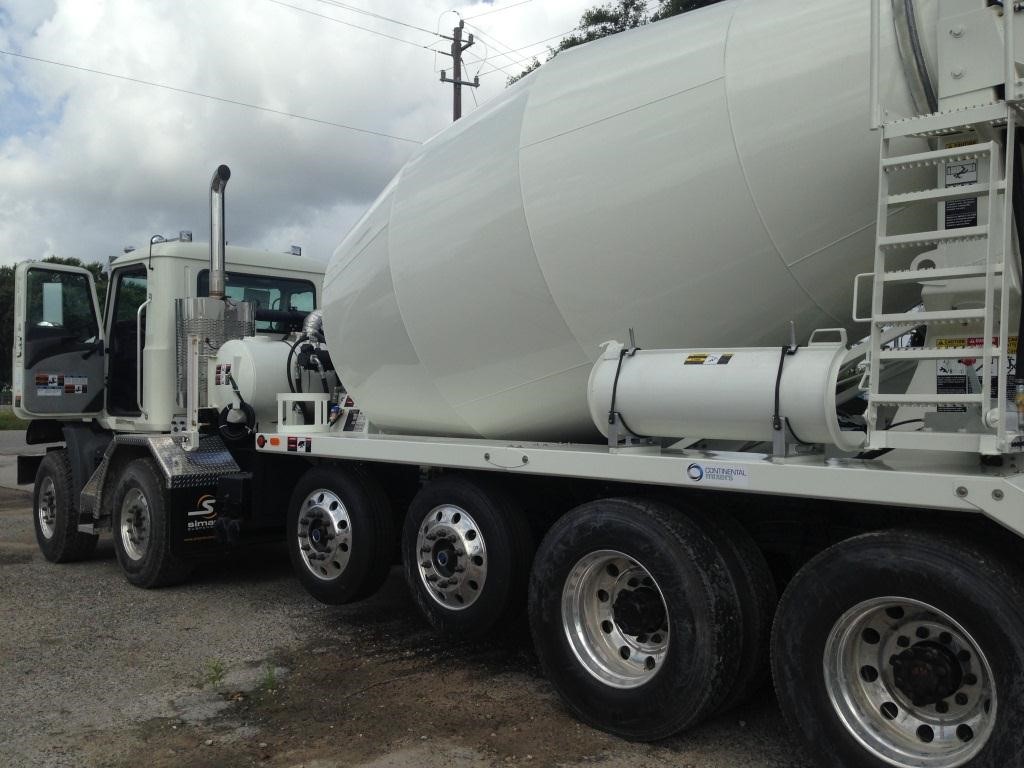
No matter the propulsion system – internal combustion or electric – the constituent parts for a vehicle will go through design and testing loops as well as manufacturing line set up and verification and validation activities.
Whatever the product, both it and the manufacturing processes would have been developed before the product is made available for purchase. To that end, we will take time to explore further the core of processes for developing a product and manufacturing that apply to the automotive industry (actually any vehicle – construction and heavy equipment for example, as well as aviation).
We have guest lectured at universities (master level degrees) with students from the aerospace industry, and more than one of these students noted their companies were adopting the automotive approach to orchestrating and ensuring product quality (APQP).
Our last article reviewed APQP (advanced product quality planning). Embedded in the article is a brief description of the PPAP (production part approval process). Now we will dig into the details of the PPAP as well as the culmination, the ISA (initial sample approval) and warrant.
The Road to Production
The APQP describes the phases of the work, from input from the customer, design and development of the product and manufacturing line, to the manufacturing output. Each phase has specific objectives, processes as well as artifacts.
Objectives are accomplished via the organization’s processes to reduce the risk intrinsic in the work. Along the way, artifacts are generated from that effort to both inform those performing the work, as well as evidence of appropriate level of due diligence.
The artifacts inform the team of the progress and risks, and therefore make prudent adjusting actions to be undertaken.
Waiting until the last minute to compare what should have been done and to what degree of success, does not allow for proactive measures to ensure the project meets the objective on time and at cost.
For example, consider this analogy: Imagine it is winter and you are in Maine. You have had enough winter, and plan to take a trip to a beach someplace warm. You buy tickets, pack, and hop on the plane. The pilot plans the route an takes off. However, the pilot does not take a heading or correction due to prevailing winds, and you end up in a place equally cold. The point is, our work should have metrics or measures, by which we are able to discern where we actually are, learn and take appropriate action to ensure we end up where we desire.
Toward the end of the effort, the artifacts provide proof that an appropriate level of diligence has been taken. Our discerning customers, especially the original equipment manufacturers and Tier 1 and Tier 2 suppliers, will require review of these artifacts as demonstration of level of detail or rigor, by which the product was developed and manufactured.
Tasks, Risk Reduction and Artifacts
The work of developing a product through to manufacturing contains roughly four categories. Those four categories are color coded below:
1. Engineering of the product – these activities are focused around developing the product to ensure the product meets the customer needs and brings value and that we are able to trace changes to the instantiations of the product due to learning through the development effort, or from the customer’s need for a change.
2. Production development – these activities are focused on the developing the manufacturing line and processes to ensure that the designed product can be built off the manufacturing line, that produces a cost effective, quality product at the production rate needed by the customer. This includes ensuring the product can be built to the prescribed quality at the desired rate cost effectively.
3. Evaluation of the product and process – these activities are focused around understanding our manufacturing line design and associated capability, by understanding the natural variation of the manufacturing line processes (process capability). These activities provide feedback to the engineering and production development efforts.
4. Quality – demonstration of achieving key attributes of the product intentions. The part submission warrant (PSW or warrant) connects an instantiation of the product, present design incarnation, with specific production line, all of which has been vetted and tested.
The work performed and subsequent artifacts generated, support some objective metric, resulting in a risk reduction in one or more specific areas below in the columns. For example, engineering the product, includes design records, and design records impact product quality and cost a well as aftermarket cost. Poorly kept design records can produce rework, as well as impact the product in the field as errant built parts make it through to production and aftermarket.
Figure 1 PPAP artifacts and impact
But why?
Product quality is emergent. There is no single action (magic bullet) that results in a quality product. Moreover, there are interconnections or dependencies in the tasks and artifacts that compound risk. In other words, not accomplishing or poor execution of the preceding task, will have an impact on the subsequent task. A quality product emerges from initiating and successful completion of actions.
This potentially long stream of actions to the parts coming off of the assembly line. Many of these actions, depend upon the preceding and is expressed succinctly in the phrase “garbage in, garbage out.” One failing of this approach, any systemic approach actually, is the possibility of pursuing this approach as if it were a check list, checking our collective brains at the door.
• Provides a baseline of product and process from which the next iteration or product adaptation (product or process) can be built
• Easy to identify the product and connect to manufacturing process
• Connects requirements, iteration of the product with the manufacturing processes
• Effectively describes the connection between requirements, product incarnation, and manufacturing method
• Reduces complications in root cause analysis
• Ensures level of capability and quality of products shipped to the customer
PPAP Levels
There is a difference in risk between a minor product change, modification or update, and an entirely new product development and introduction. The larger the number of tasks required to successfully accomplish, the greater the risk. In this way the PPAP is influenced by the customer, the supplier, and the scope of the effort.
The table below provides an overview of the levels, for example, level 5 would be almost certainly undertaken for a new product and new line. The lower the number, is the response to smaller scope or change to either the product or the manufacturing line. In the most extreme incarnation, the PPAP documents will be reviewed at the manufacturing facility, after having watched the run-at-rate (R@R).
The run at rate, is a run of the manufacturing line to produce production parts at the full volume rate. This is a stress of the manufacturing line, while the customer quality engineer is present and sometimes other engineers from the customer.
There are likely other runs from the line to produce prototype parts for some prototype vehicle builds and perhaps other testing that may include early vehicle integration testing. At this point, all early runs (if there was a need) have happened and these partial production run, that is some of the production processes were ready and some were burgeoning to be assessed.
Table 1: Derived from Production Part Approval Process (PPAP). (2000). Automotive Industry Action Group (AIAG).
Level 1 Warrant only. For appearance parts, appearance approval report submitted to the customer.
Level 2 Warrant with product samples and selected supporting artifacts to the customer.
Level 3 Warrant with product samples and supporting artifacts to the customer.
Level 4 Warrant and artifacts as defined by the customer.
Level 5 Warrant with product samples and complete supporting artifacts reviewed at the suppliers manufacturing location.
The Warrant
Parts are not allowed to be shipped from the supplier into any OEM manufacturing site without having provided the PPAP documentation and sign off or acceptance (no matter the level), and when defined, the ISA (initial sample approval) parts.
These parts usually undergo dimensional evaluation and perhaps some other customer evaluation like systems integration testing. The ISA parts will be shipped with what is referred to as a warrant (or part submission warrant – PSW).
This certificate is attached to an iteration of the product, in this case, for a P level (per either supplier or customer’s agreed upon description) part. Essentially the warrant identifies a specific part, and will be connected to a specific material, design and processes to manufacture.
In the event there is no customer review during the run at rate, all PPAPs lower than a level 5, the parts will be sent to the customer with a tag that clearly identifies the product and iteration. Below is a tag that will be connected with the individual part (a set of different part number) along with the identifying purchase order number.
This allows for quick traceability of the product received to production iteration, eliminating confusion. This is necessary because these parts may be used for appearance, and perhaps integration testing.
Figure 2 Example of product PPAP tag.
Summary
Any product, electrical, electronic or purely mechanical can benefit from a comprehensive approach that facilitates learning during the product conception, as well as manufacturing development. This applies whether the vehicle is powered by an internal combustion engine, or from batteries and electric motors. It applies equally in the automotive and aerospace sectors.
Developing a competent product and manufacturing line and being able to trace a specific instantiation of the product to the production processes are fundamental to controlling the system. Besides providing a mechanism that illustrates the key areas of the work by which the actual work can be measured, it provides a baseline for process and product from which continuing improvements are possible.
We know tangible things about the product and the processes, not just guessing and assuming. This continuity provides a baseline for continuous improvement, and, a point for problem resolution should we find a defect as we are able to hold with some confidence the chain of events that brought the product to that point.
The individual project’s situations and circumstances vary, so the approach must also be able to adapt to this variation to ensure our response is not overly burdened and complicated.
More Stories
Cybord TCI – The Future of Manufacturing Integrity
Getac on AI’s transformative impact on automotive production and aftersales
New Infineon Bluetooth range designed to meet OEM needs