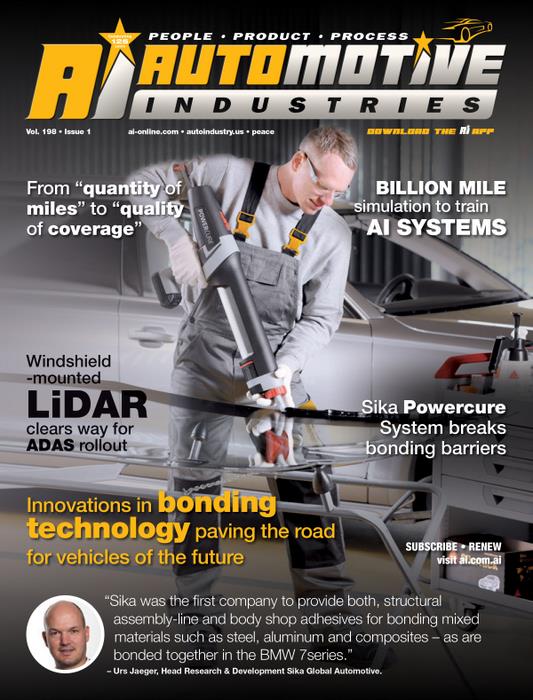
Breakthroughs in the formulation of automotive coatings are helping OEMs to use less energy, increase throughput and reduce emissions. New coatings are also essential for the successful introduction of autonomous and semi-autonomous vehicles, as well as for lithium-ion batteries.
A recognized leader in the field of coating development is Pittsburg-based PPG, which provides industrial coatings for automotive parts and accessories such as rigid and flexible exterior trim systems, steel and aluminum wheels, body panels, bumper and break systems, hitches, shocks, axles, coil springs, under hood/body parts, and sway bars.
Automotive Industries (AI) asked David Bem, PPG Vice President, Science and Technology and Chief Technology Officer, how the new paint shop technologies help “green automotive manufacturing. Bem: Our award-winning B1:B2 Compact Paint System cut out an entire step in the coatings process by eliminating the primer layer. The B1 and B2 layers are applied wet-on-wet, which reduces the time to paint a vehicle by up to 90 minutes. This increases vehicle throughput while simultaneously reducing emissions and energy consumption. Some PPG customers have reported energy savings of up to 30%, a 40% drop in carbon dioxide emissions and a 7% reduction in volatile organic compound emissions. In 2018, we introduced technology that eliminates the curing step after the polyvinyl chloride (PVC) is applied to a car’s exterior and underbody.
This 4-Wet sealer technology allows for the sealer, two coats of paint and clearcoat to be applied wet-on-wet with just one final curing step. We recently introduced a low-energy paint process which was developed through Project LEAPP™. The process uses PPGdeveloped waterborne crosslinking chemistry that cures at 80% degrees Celsius – compared to 140% C for current systems. This significantly lower curing temperature which, combined with faster flash and dehydration times, can help reduce energy consumption by up to 39%.
AI asked Jean-Marie Greindl, President EMEA, PPG, to tell us about PPG’s Supplier Added Value Effort ($AVE) process. Greindl: The $AVE program provides customers with innovative solutions at all levels. This includes driving value within ongoing business process improvements in areas such as logistics, operations, inventory management and general business administration practices. Technological innovation helps customers to differentiate their products in the marketplace.
AI: What is your presence in China? Greindl: PPG is the leading automotive OEM supplier in China. We are currently building a new R&D/technical facility in Tianjin that will further our positioning and preparedness for taking on the emerging area of new electric vehicles (NEVs), which have heavy emphasis in China.
AI asked Dr. William L. Brunat, Technical Director EMEA, Automotive Coatings, what new processes are in the pipeline. Brunat: With the switch to electric vehicles (EVs), coatings go beyond providing protection and beauty to also powering the vehicle. Lithium-ion batteries use coatings to store and transfer their electric charges. We have developed a binder and resin system that eliminates N-Methylpyrrolidone (NMP), a toxic solvent currently used in all electrode binders.
AI: How is PPG’s low-cure system changing the OEM automotive paint processes? Brunat: We were able to completely reinvent paint technology through an 18-month Project LEAPP-supported partnership with Ferrari to provide the full spectrum of required colors at a 100 o C. This provided Ferrari with significant benefits, such as energy savings, reduced emissions and the ability to coat low temperature substrates like polypropylene or carbon fiberreinforced plastics (CFRPs).
AI: What other trends and technical breakthroughs in automotive is PPG working on? Brunat: Automotive innovation is being driven by the push for improved sustainability and the development of autonomous and electric vehicles. Smart coatings will be fundamental to the effective and safe functioning of these new vehicles and surrounding infrastructure. Some of the key technologies will be LiDAR technologies, battery coatings and easy-to-clean coatings. The latter may just seem like a convenient function, but it could become fundamental to the safe running of an autonomous vehicle by keeping the sensors and cameras clear of obstructing dirt that could result in unsafe ineffectiveness. Â
More Stories
Lakshmi Prasad Bhatta on the quest for zero road deaths
Cybord TCI – The Future of Manufacturing Integrity
Flexible Magna Manufacturing Solutions: The Key to Success in the Automotive Industry