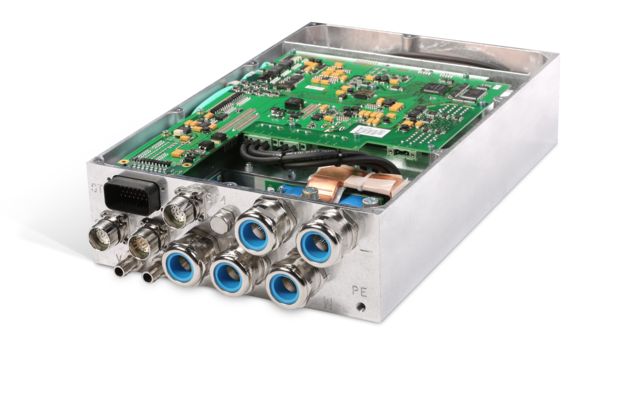
Economic efficiency is one of the central challenges of electrical mobility. Often, technically outstanding solutions ultimately cannot be manufactured in series because of the comparably high costs. How do power electronics offer a potential here?
The basic purpose of power electronics is to convert electrical current efficiently without mechanical parts and to adjust the voltage level. This process takes place in nearly all electrical devices. In an electric or hybrid drive train, the voltage is adapted between the electric motor and the battery, for example, or in the charging device. This makes it possible to adjust and optimize the energy management among the respective electric components within a drive system, which can considerably improve the efficiency of the entire drive train.
Distribution of costs in the drive system
The purchasing cost of power electronics is around one percent of the entire cost of an electric vehicle – relatively little, considering that the battery often represents up to 50 percent or more of the cost. An efficient use of battery capacity is thus an important criterion for an economically efficient drive train. The purchasing costs of a motor and a suitable high-quality inverter are therefore less than the savings potential of the battery size – with the right inverter, a smaller (and thus lighter and less expensive) battery can be chosen without having to sacrifice range.
The right inverter
The overall system configuration, in other words, the coordination of the individual drive components with each other and the optimization to the load profile of the application, has a significant effect on efficiency and economic feasibility. Parasitic current fluctuations with an amplitude of several hundred amperes can result especially in the case of load changes, in other words, changes in driving behavior. These “side effects”, among other things, cause efficiency losses. However, such losses can be greatly reduced by a well thought-out, coordinated drive train synthesis.
The contribution of power electronics
But how does this work? Effective inverters smooth out the PWM frequency very precisely, which reduces harmonics when voltage changes occur. The result is a very high reduction in excessive waste heat, which prevents efficiency losses. An active smoothing of these voltage ripples can sometimes also be achieved by interconnecting a DC/DC converter. Good inverters also have a fast current control time. A very closely timed amplitude sampling allows a smooth and thus low-loss motor rotation. An efficiency advantage of up to 10% can be realized for the entire system with a good inverter, such as, for example, the VECTOPOWER from ARADEX, compared to a configuration with conventional inverters.
High outputs and economical drive train dimensioning
A particular challenge for traction drives is providing maximum torque from a standstill, for example, when starting on a hill. This can be counteracted by an additional coupling or overdimensioning of the drive train, which also covers such power peaks. However, this entails correspondingly higher costs, which would require considerable reductions in order to be economical. It would also require additional installation space, which is always a sensitive factor in vehicles. ARADEX offers another solution for the power electronics of the VECTOPOWER family: This is based on the common solution of realizing PWM frequency to control the current of the power electronics with MOSFETs or IGBTs. It uses the fact that the basic limiting factor in the IGBT is its operating temperature and IGBTs normally have a time delay in the temperature increase. Using a very precise simulation model for temperature measurement in semiconductors, IGBTs can be operated so that up to 20% more current is available during starting. This usually eliminates the need for larger and more expensive IGBTs as well as an overdimensioning of the drive.
As a result, the extremely precise simulation model for temperature measurement in semiconductors allows a high utilization of the IGBT capacity. The boost function used by ARADEX also makes a high power during starting possible with smaller and thus more economical IGBTs. The implemented semiconductor simulation model for calculating the IGBT temperatures prevents the IGBT from overheating and the lifetime of the inverter from decreasing.
Economical configuration of drives
The most important parameters for an economical drive train are effective power electronics and a precisely coordinated overall system. System suppliers such as ARADEX offer clear advantages for this; they not only provide all drive components but also numerous services such as planning, dimensioning, and configuration of the drive train. The components can be precisely coordinated with each other, and any interactions can be identified early on and precisely prevented. The ARADEX team will be happy to make you an offer for an efficient drive train configuration of your electrification project.
More Stories
Sika – where battery storage technology for EVs, wind and solar meet
Battery pack solutions from PPG
Flexible Magna Manufacturing Solutions: The Key to Success in the Automotive Industry