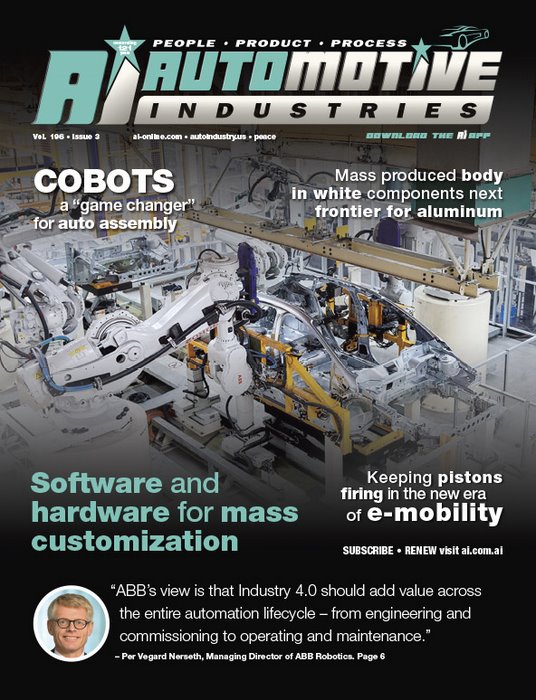
Mass customization of vehicles is changing the way production lines are configured and managed – the Henry Ford model of pushing out identical products is becoming obsolete as customers demand vehicles tailored to their personal preferences.
“The trend towards manufacturing in smaller lots of greater mix means people are coming closer to production equipment in more sporadic and intermittent ways – changing programming, bringing different materials or inspecting new processes. It is simply not productive to stop a line every time a person steps in,” says Hui Zhang, Head of Product Management at ABB Robotics.
In response to this need ABB Robotics developed the safety-certified monitoring and control software SafeMove2, which enables people to work safely alongside moving ABB robots with payloads ranging from 6kg to 800kg. “SafeMove2 allows robots and operators to work more collaboratively and closer together by restricting robot motion to precisely what is needed for a specific application,” says Zhang.
The company is also digitizing production processes. “Welding whether in a large automotive plant or in a smaller machine shop will need to include vision-integrated solutions and flexible automation systems that are interconnected to everything else. ABB provides solutions to digitalize every step along the automation life cycle,” says Nigel Platt, Business Line Manager, Welding and Cutting, ABB Robotics.
In March 2017 ABB launched ABB Ability, its portfolio of more than 180 digital solutions and services. ABB Ability helps customers in utilities, industry, transport and infrastructure develop new processes and advance existing ones by providing insights and optimizing planning and controls for real-time operations. The results are fed into control systems to improve key metrics such as factory uptime, speed and yield.
Automotive Industries (AI) asked Per Vegard Nerseth, Managing Director of ABB Robotics, how the company’s products and services help the automotive industry to customize assembly operations.
Nerseth: Robotic automation is providing greater flexibility for OEMs to make more models on the same lines, from framing car bodies to assembling cylinder heads. Often these allow the elimination of work stations dedicated to one model or variant. If we take axle assembly, ABB has a solution which can accommodate many different axle types in the same cell. In the past automakers often would have needed separate and dedicated assembly stations for each type of axle.
This robotics solution can also do previously sequential steps in parallel – such as preparing the axle bearings and lubrication for pressing while at the same time seating the differential case into the axle housing. This reduces the cycle time, so automakers get more flexibility and at the same time higher throughput with a smaller footprint. Robotics automation is also allowing manufacturers to accommodate many new materials like carbon fibre and high-tech laminates than need different joining processes to welding. As welding takes a smaller role, new automation applications are needed such as gluing and dispensing. This is where robots can provide quality and reduce cycle time.
AI: How important are smaller batch sizes with higher flexibility important to automotive manufacturers?
Nerseth: Very important. Consumers today expect to customize every aspect of their car, from the paint finish to the entertainment system. The number of possible combinations has increased exponentially. This is a huge shift for such a capital-intensive industry that has traditionally been set up around economies of scale and large runs of the same product.
AI: How do your robots help OEMs make the shift?
Nerseth: In a word: “flexibility”. They are far more adaptable and easy to change that the assembly line concept Henry Ford pioneered. Today an ABB body-in-white gate framer solution lets Ford make six different vehicles on the same line, and can switch between models in just 18 seconds. And it is not only the robots – software has made huge advances in recent years. Today we can do a lot of the troubleshooting and optimization in the virtual world before disrupting factory production. This means greater engineering efficiency and faster production ramp-ups.
AI: Tell us about ABB and Industry 4.0.
Nerseth: ABB has been a digital pioneer for a long time. Over a decade ago we started offering a remote service to monitor the health of robots and proactively prevent downtime. This was long before the term “the Internet of things” was even coined. Today we have some 7,000 connected robots in over 750 factories, and are doing advanced analytics to optimize the performance of entire robot fleets.
AI: How is automotive manufacturing being impacted by digitization/Industry 4.0?
Nerseth: One great example is the acceleration of the industry towards electric vehicles. As we shift more towards EVs we will see powertrain components disappearing in favour of electrical motors, batteries and control modules. These require a lot more complex automation. Industry 4.0 gives us the opportunity to mass customize these “smarter” components far more than we can with today’s powertrain presses and spot welding processes.
Industry 4.0 is helping us do new tasks like small parts assembly with greater productivity and flexibility and to get beyond the learning curve for EVs. That means we arrive faster to sustainable transportation and reduced environmental impact. Industry 4.0 is not only having a big impact on manufacturing, it is also opening new doors for greater innovation of automotive business models. Think of all the different or emerging business models we have today compared to a just few years ago, from the OEMs all the way to Uber. These are all unlocked by connecting intelligent devices and vehicles to the cloud – self driving vehicles, increased use of sensor data and telemetry, EV power grid schemes, it really is a transformative time for the way we look at transportation.
AI: What role does ABB Ability play in keeping all aspects of manufacturing cohesive?
Nerseth: One key area is that many parts of manufacturing are moving from the physical world to a virtual world. This means that we can design and build processes offline, before we disrupt production on the factory floor. Better software simulation tools allow us to optimize a line and train operators, so new production can ramp up faster and with fewer surprises. Many industries such as electronics and food and beverage are seeing much shorter cycle times, but this agility to launch new products is also of great value to automakers and their tiers.
Another important area is the ability to look at the performance of robots over an entire fleet, across several plants. Through our ABB Ability Connected Services, our customers can get answers to questions such as “Which are the hardest working robots that we should prioritize for maintenance?” Or “which are our best performing robots that should set our KPI benchmarks?” ABB’s view is that Industry 4.0 should add value across the entire automation lifecycle – from engineering and commissioning to operating and maintenance.
AI: How has SafeMove2 being made available to robots of all sizes benefited automotive OEMs?
Nerseth: It allows people and robots to safely share the same workplace without compromising productivity. Even our IRB 8700 with a handling capacity of 800 kg can become a collaborative robot with SafeMove2. The robot can lift an automobile body! Volvo is using SafeMove2 in its roof hemming and aluminium fender assembly stations – it allows people to safely walk into the robot operating area to load and unload parts without stopping the robot, and to easily change parts for different variations. So, collaborative automation is about productivity and flexibility, not only safety!
More Stories
Mosaic Click board from MIKROE delivers global coverage multi-band and multi-constellation tracking ability
Current transducer from Danisense selected for DC charging station testing device demonstrator at TU Graz
New Click board from MIKROE helps develop and train ML models for vibration analysis