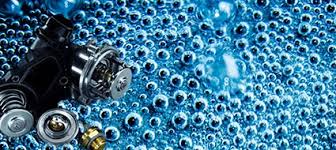
MAHLE Engine Components has developed an innovative lead-free bearing system combining highly engineered polymeric coatings with robust lead-free bearing linings for heavy-duty truck engines.
Â
The new system delivers improved performance compared to existing bearing linings that include lead.
Â
“Polymer technology is well established in the light- and medium-duty market for engines under 10 liters in displacement,” said James George, head of product technology at MAHLE Rugby, U.K.
Â
George explained that the need to adopt the technology for loaded bearings on heavy-duty applications in North America reflects changes in bearing operating conditions and a market need for alternative solutions.
Â
Improvements in wear resistance will help engine manufacturers cope with newly released low-viscosity engine oils which are required to help improve fuel economy, he noted.
Â
MAHLE research shows that compared to lead-free bearings with electroplated coatings, MAHLE’s polymer-coated bearings offer increased resistance to both wear and fatigue.
Â
Customer testing of polymer-coated crankshaft main bearings and connecting rod bearings also has shown remarkably improved performance compared to more commonly used electroplated leaded bearings.
Â
MAHLE’s polymeric coatings offer a variety of other benefits as well. Removing lead from the bearing improves corrosion resistance and allows for extended oil-drain intervals. Lead-free bearings also are environmentally safer and easier to dispose of.
Â
Overall, industry testing indicates the new bearing system will offer significant owner-operator cost savings as well.
Â
Comparative testing by a major commercial-vehicle engine builder, for example, showed polymer-coated bearings (shown above right) delivered distinctly better post-test wear results.
Â
Production of the new bearing system began this summer at a MAHLE facility in Atlantic, Iowa.
Â
The first heavy-duty diesel engines using MAHLE’s polymeric lead-free bearings will appear on vehicles being introduced during the second half of 2016. Product development programs for additional applications currently are underway with two major engine manufacturers.
Â
“Our new bearing system provides a great combination of proven cast-bronze bearing technology with a polymer overlay that features high load capabilities, as well as seizure and wear resistance,” said Dr. Joachim Wagenblast, head of Product Development for MAHLE Engine Components USA.
Â
About MAHLE
MAHLE is a leading international development partner and supplier to the automotive industry. With its products for combustion engines and their peripherals as well as solutions for electric vehicles, the group addresses all the crucial issues related to the powertrain and air conditioning technology–from engine systems and components to filtration to thermal management. MAHLE products are fitted in at least every second vehicle worldwide. MAHLE components and systems are also used off the road–in stationary applications, for mobile machinery, rail transport, as well as aerospace and marine applications.
Â
In 2015, the group generated sales of approximately EUR 11.5 billion with around 76,000 employees and is represented in 34 countries with over 170 production locations. At 15 major development locations in Germany, Great Britain, Luxembourg, Slovenia, the USA, Brazil, Japan, China, and India, about 6,000 development engineers and technicians are working on innovative solutions for the mobility of the future.
Â
More Stories
Battery pack solutions from PPG
Huntsman Polyurethanes introduces a new range of polyurethane-based products developed for battery enclosures, battery cell potting and underfloor protection
Lakshmi Prasad Bhatta on the quest for zero road deaths