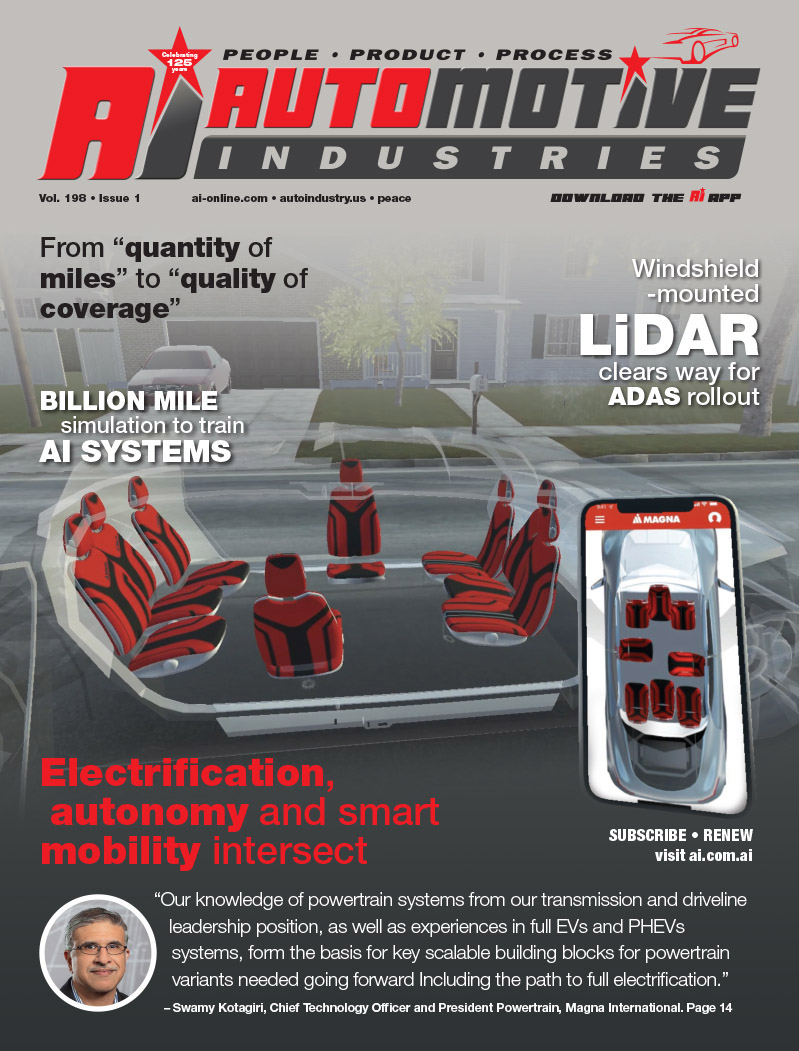
Numerous automotive manufacturers are finding new ways besides engine downsizing to minimize the fleet consumption of their vehicles. A useful and sustainable concept includes intelligent thermal management, and OEMs are increasingly taking note of this approach in particular. With its innovative, multilayered encapsulation technology based on low-weight reinforced thermoplastics (LWRT), Röchling Automotive provides improved insulation of the engine compartment. In combination with active grille shutters, the solution offers crucial ecological and acoustic advantages alongside optimized heat management. Röchling Automotive demonstrates its expertise in the field of thermodynamics at the International Suppliers Fair (IZB) in Wolfsburg in hall 6, booth 6208, from October 14 to 16, 2014.
Perfectly Packed
Encapsulation close to the engine makes especially good sense where the engine has the largest thermal and acoustic radiation surface. Noise reduction directly at the source makes secondary weight savings of up to 12 kilograms possible. In addition, the lightweight design allows pollutant emissions to be reduced. As a result of the principle on which they work, many components belonging to the engine peripherals, such as water pumps and turbochargers, cannot be isolated and act as a thermal bridge when the engine is off. This is why Röchling Automotive pursues the strategy of encapsulation away from the engine. This type of encapsulation allows virtually the entire periphery of the engine to be effectively isolated by closing various openings. The result is a lower cooling rate. Active air flaps which additionally improve aerodynamics are an essential element of the concept. “To achieve a higher degree of closure and maximum efficiency, the air flap is becoming the crucial component of engine encapsulation as it allows the front of the vehicle to be sealed off more and more,” explains Ludwig Huber, General Manager Innovation and Business Development, Röchling Automotive. Measurements revealed potential savings with regard to fuel consumption and CO2 emissions of up to two or three percent. As a result, there are less and less cold-start situations in everyday operation and the engine works more energy-efficiently and produces fewer emissions thanks to its lower fuel consumption.
Lightweight and yet Dimensionally Stable
To achieve effective thermoacoustic encapsulation, Röchling Automotive uses the latest generation of fiber-reinforced thermoplastics. Because of its sandwich structure, the 15 millimeter thick LWRT material provides high thermal and acoustic isolation and is as light as a feather but stable at the same time. Additional blocking or aluminum foils allow customer-specific modification of the components. Another benefit of the extremely thin aluminum surface coating is that LWRT components do not absorb inflammable liquids, so they can be used for applications located beneath the powertrain without any problems whatsoever. The single layers have proved their worth in numerous tests, and they do not peel or catch fire even after being exposed to flames for relatively long periods.
Fresh Breeze
Engine encapsulation reaches its optimum thermal and energetic efficiency when combined with air flaps controllable according to the requirements. Open air flaps allow high cooling capacity through maximum air flow. In the closed position, they reduce the time which the components need to reach operating temperature by up to 30 percent. This technology has proven to be very effective in urban traffic and over short and long distances
More Stories
Some Ways How Motorists End Up in Collisions at U-Turns
Maximise Margins with Proven PPF Tactics
Finding the Car Boot Release Button – Tips and Tricks