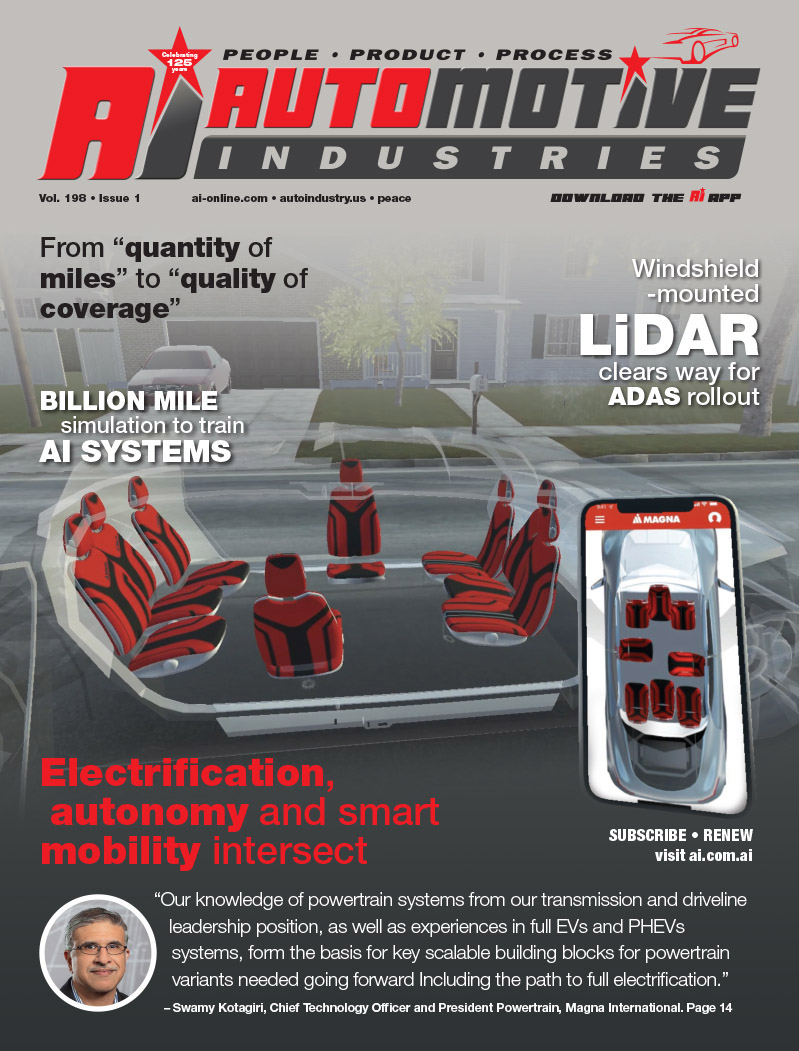

Electromagnetic simulation is becoming an increasingly vital part of the automotive design process as vehicle electronics become more complex and development cycles shorten.
Many new technologies such as automotive radar, intervehicle communication systems and on-board computers are developed using simulation from the beginning of the design process. Tasks that were traditionally done by experimentation, such as electromagnetic compatibility (EMC) and electromagnetic interference (EMI) analysis, antenna placement and cable harness layout, can be made more efficient by using simulation to create “virtual prototypes”.
Computer Simulation Technology (CST) has been leading the development of electromagnetic simulation tools for the industry, both through its own CST STUDIO SUITE® software, and by cultivating connections with both other leading software developers and with auto manufacturers.
Automotive Industries (AI) asked Dr. Matthias Tröscher, KAM and automotive expert at CST how 3D electromagnetic simulation with CST STUDIO SUITE® has helped optimizing the EMC and EMI performance of automotive multimedia systems.
Tröscher: Modern automotive multimedia systems include a large number of functions, such as HD video players, touch screens, wireless interfaces, Internet connections, the display of data from sensors and cameras, telecommunications, and more. Future generations of mobile phones or other consumer electronic devices have to be supported over a car’s lifetime, even though their technical details are usually not known during the development phase. As a consequence, multimedia systems must include leading edge technology, and have to be robust with respect to EMC and EMI. Classic 2D simulation approaches are not able to predict the mutual transient electromagnetic coupling between the currents on the PCB and the fields outside the PCB. Here, 3D simulation plays a major role, as thorough analysis of emission or susceptibility effects has to take into consideration the three-dimensional environment including enclosures, connectors, cables, antennas, and parts of the chassis – or even the whole car geometry.
For example, even if a multimedia system has passed all SI and PI checks, there are often common mode currents induced on the PCB due to imbalances or manufacturing tolerances which are not compensated by filters or other measures in the first prototype. If such currents propagate to connected cables they may find a resonating structure that supports radiated emission effects. In the worst case, the emitted fields may directly couple back into the multimedia system and cause interference, malfunctioning, or even breakdown.
AI: What are some of the challenges of automotive EMI simulation?
Tröscher: Two of the biggest challenges are definitely the difference in the scale between different electronic components in the car and the increasing frequency of the installed antennas, such as those used in car-to-car-communications (5.9 GHz) or radar systems (77 GHz). Considering that the difference in scale between the length of a car and the thickness of coating materials, varnishes, PCB metallic layers or planar antenna structures is 10 to the power of 6 or so, the required number of mesh cells for the numerical calculation would be in the billions if brute force 3D full wave simulation approaches were applied. The situation would be even more challenging for simulations of car-to-carcommunications in real-world scenarios.
CST has been involved in a number of partner projects with automotive suppliers and OEMs for many years to develop simulation methods and tools for EMI simulations in both the time and frequency domain, for electrically large and small structures, and for broadband and highly resonant systems. Today, a user can select single parts of a complete system and apply the most appropriate (hybrid) simulation technique to each of them. The results of these single parts can be combined in a system-level analysis in order to investigate their mutual interference and overall electromagnetic behavior, using the System and Assembly Modeling (SAM) framework in CST STUDIO SUITE® and our strong links to partner products such as Antenna Magus, EMIT and Savant.
AI: How do these partner tools contribute to a smooth simulation workflow?
Tröscher: When designing new antennas, or when using standard antennas, engineers often spend too much time redoing work that has already been done, due to ineffective information management. With Antenna Magus you can simply choose an antenna, select the design target, enter objective values according to the design specification, and get a design that meets the objectives – within seconds. When antennas are located close together, seemingly insignificant emissions or susceptibilities of transmitters and receivers can result in interference due to high coupling levels.
Cosite analysis is best performed concurrently during the development process. The EMIT software from Delcross allows users to start working on the cosite problem at an early stage with approximate models that can be updated at any time for antenna-to-antenna coupling, RF systems, cables, filters, radios, amplifiers, and so on. A one-step import of CST STUDIO SUITE® models into EMIT allows for a tightly integrated workflow. By combining CST’s Complete Technology with Savant from Delcross, users have got a tool box that allows for time-efficient and highly accurate electromagnetic simulations in electrically large and complex structures.
AI: Tell us a little bit about automotive radar simulation
Tröscher: Car design and aesthetics are as important as technical functionality. As a consequence, radar frontends for car environment monitoring have to be hidden behind bumpers. Radar that performs perfectly in free space can have its electromagnetic field behavior altered tremendously when situated behind the bumper due to the multiple reflections of the signal within the bumper itself and between the bumper and the car chassis. Radar engineers need to investigate different mounting scenarios, the influence of material properties on the radar beam, the optimum feeding of the radar patch antennas, and the perfect matching network. These are all tasks that can easily be handled with CST STUDIO SUITE
AI: Give us an idea of what CST’s EDA solution is for a typical automotive application.
Tröscher: Modern multimedia systems have a number of microcontrollers and memory modules inside, and include quite challenging technologies like USB 3.0, DDR3, Ethernet, and others. CST STUDIO SUITE® fully supports pre-layout and post-layout analyses of these devices and provides a smooth workflow all the way from concept phase through component placement, PDN definition, signal net routing and finally to 3D EMI analysis. Because these simulations typically run in seconds or minutes, a great many “what if?” analyses can be easily performed and the PCB design optimized at an early stage of development.
A very useful new feature of CST PCB STUDIO® is the decoupling-optimization tool. This helps to find the optimum position and value of decoupling capacitors with just a few mouse-clicks. There has never been an easier way to find the right decoupling concept in order to fall below the target impedance threshold in the frequency range of interest. As an extra check between PCB development and EMC simulation, CST offers a rule based SI and EMC analysis tool called CST BOARDCHECK™. The “old way” of applying best-guess design practices then fixing the EMI problems after the product is built is no longer acceptable in today’s market place. Designs must be cost-effective and must pass regulatory requirements the first time through the design cycle.
AI: Where do you see simulation trends in the near future?
Tröscher: The vehicle electrical distribution system or cable harness in modern vehicles like cars, trucks, or airplanes is still an underestimated component. It is both one of the heaviest and – due to the high amount of manual fabrication – one of the most expensive parts in the car. With respect to CO2 emission regulations and new challenges regarding e-mobility and high voltage systems, the automotive cable harness is part of a technological revolution, with the strongest demands on weight reduction, topological restructuring, and transmission of high-speed signals.
Furthermore, due to the fact that the traditional metallic car chassis has been partly replaced by composite materials, there is no longer a closed common mode current return path which requires substantially new concepts in cable harness design.
CST has been involved in technical discussions and development projects with automotive OEMs as well as Tier 1 and Tier 2 suppliers for many years in order to fit numerical cable simulation solutions into place for the future. The main topics that we expect to see more of are weight reduction by means of new materials, cross-sectional miniaturization, shielding improvement, bus architecture, and the attempt to implement electronic design automation (EDA) also for the cable harness
More Stories
Some Ways How Motorists End Up in Collisions at U-Turns
Maximise Margins with Proven PPF Tactics
Finding the Car Boot Release Button – Tips and Tricks