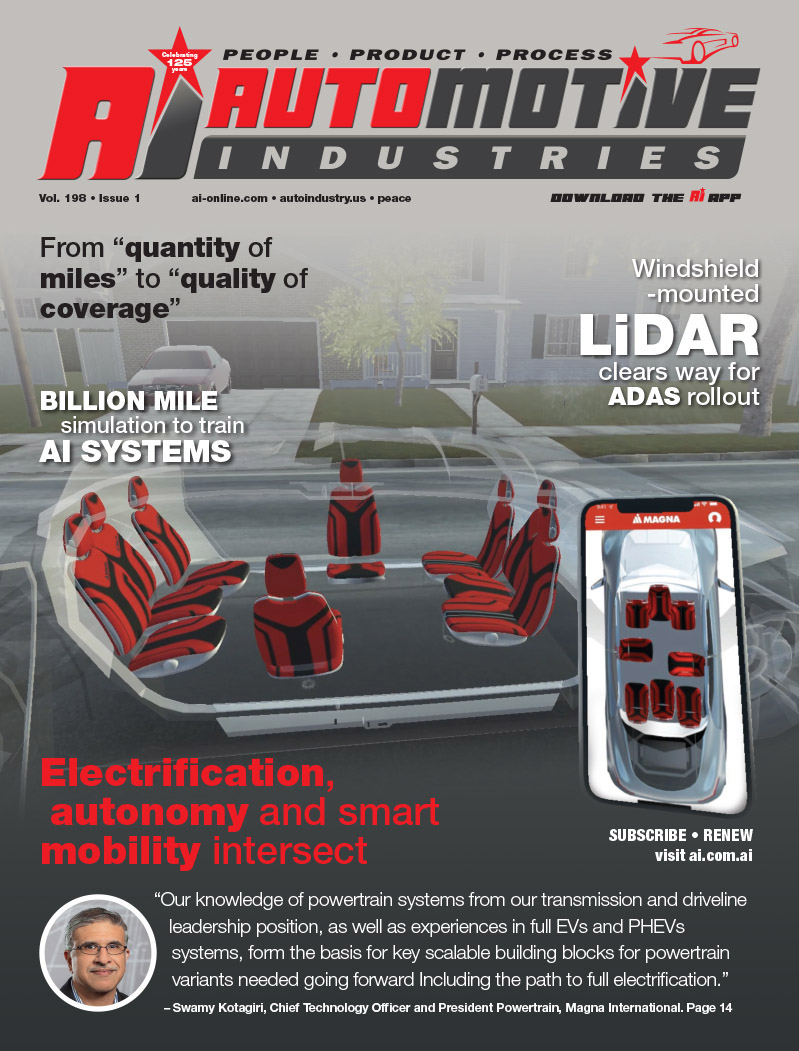
Paving the way for innovation in automotive materials
A car has thousands of rubber and plastic components, but none is more highly engineered, and highly complex than a tire. During World War II there was rapid innovation in tire technology, due almost entirely to the urgency of the war. Only incremental changes have occurred on an industrial level since. Recent achievements in research labs give hope for a new generation of tires that are as significant to progress as what we saw in the 1940s.
I have spent more time inside rubber factories and labs than would be recommended. I grew up with rubber in my DNA in Akron, Ohio, where my family had worked for both rubber companies, chemical suppliers to rubber companies, and instrumentation companies for testing rubber. The importance of this old material in modern cars was never far out of my mind whether I was working on my Ph.D., reading about cars of the future, or participating in projects to make a more environmentally friendly car. Akron is no longer the center of rubber innovation for tires, but the history of discovery, progress and the successes of the industry have inspired me to continue to look for improvements.
“Nanotronics Imaging” – the company which I head – is a name that sounds more futuristic than nostalgic, yet history and nanotechnology are linked. We often say at Nanotronics: “To build the future you have to see it.” This is usually a technology comment that is a challenge for us and industry to enable nanotechnology to grow in scale. Building and seeing, however, are also more personal. It is seeing our world and our technologies in ways that we normally don’t.
The success of tire technology during World War II ranks as a triumph of industrial and scientific collaboration equal to the betterknown Manhattan Project. The only available supply of natural rubber was from Hevea trees in Southeast Asia, which fell under the control of the Axis forces. When the United States entered the war, they would need a new source for rubber, and new plantations in the west were not a viable option.
In the 1930s, a chemist named Waldo Semon worked for BF Goodrich in my home town of Akron, Ohio. BF Goodrich was not only a tire company but also a major chemical company and early pioneering aerospace company. Waldo Semon is well known among chemists for the invention of the first functional plastic, PVC. Before the United States entered the war, Semon visited Bayer, Germany’s largest chemical company, where he was shown an invention that had not yet made its way to America. Buna N was a synthetic elastomer that provided many of the same beneficial properties of natural rubber. Semon’s study of the process and the inspiration it provided made him a kind of ambassador of technological possibilities back home. The highly competitive tire industry was united by the more imminent competition of war.
The United States Synthetic Rubber Program brought BF Goodrich and all of the major tire companies together in an effort to develop a synthetic tire tread. The result was styrene butadiene rubber (SBR). Without it, there would not be the airplanes, tanks, or cars that fought for victory in World War II.
SBR is still the primary elastomer used for tread compounds in tires. Tire treads alone are a blend of up to thirteen different chemicals, while the remainder of the tire includes various other rubber compounds and components made of metal and textiles. One of the chemicals in the tread rubber formula is the filler. The filler is critical for determining the durability, flexibility, rolling resistance and life expectancy of a tire. Traditionally these rubber fillers were carbon black, which not only gives the tire color but also reinforces the strength of the tire when it interacts with SBR.
Carbon black has been used since the beginning of tire manufacturing with great success. The structure of carbon black, as the particles decrease in size, allows for many of the performance characteristics associated with a good tire. Carbon Black does present challenges as compromises are made in certain properties when the particle size decreases, but improve for others. It is a difficult balance that requires a unique specialization. Even more immediate in a world of high energy costs and worries over climate change is the large amount of burned oil that is carbon black itself.
It was clear to many of us that the next step in improving tires would be in looking at both performance properties, and maybe even more importantly environmental sustainability. It was the politics of the 1940s that made synthetic tire treads possible, and the seeds of innovation for the 21rst century also came from a political will. I was lucky enough to step into this with my small involvement with a European project that was part of an effort to make “The Green Tire”, to replace carbon black filler with something more environmentally sustainable. It has been known that silica provides better rolling resistance and overall tire efficiency without using petroleum. However the integration of silica into the tire, as well as the adjustments to the process were a challenge. Most tire treads in Europe use silica over carbon black as a reinforcer. In the United States, we still use mostly carbon black but silica use is increasing. Silica is almost a nanoparticle but carbon nanotubes, graphene and nanoclays are even smaller. These nanoparticles improve quality.
Nanoparticles are only used in small batch and lab settings because the size is on a level that requires an ability to inspect for quality that has not been available. For researchers who have discovered these materials and want to use their properties in tire manufacturing, I want to provide the inspection and control of traditional machinery so that we can take advantage of using nanofillers in traditional parts on a car to provide improved energy efficiencies, smoother rides and longer lasting parts.
Enabling imagination and creation at a smaller scale in the automotive will jumpstart innovation just as World War II did for SBR. This is where Nanotronics could fit in. I hope that we can enable much of this great work that has progressed in labs, see it transferred to factory floor, and onto all of the cars we drive. We will have won a different kind of war, which is one of stagnation and complacency. It will show that a war is not the only political motivation for building the future
More Stories
Some Ways How Motorists End Up in Collisions at U-Turns
Maximise Margins with Proven PPF Tactics
Finding the Car Boot Release Button – Tips and Tricks