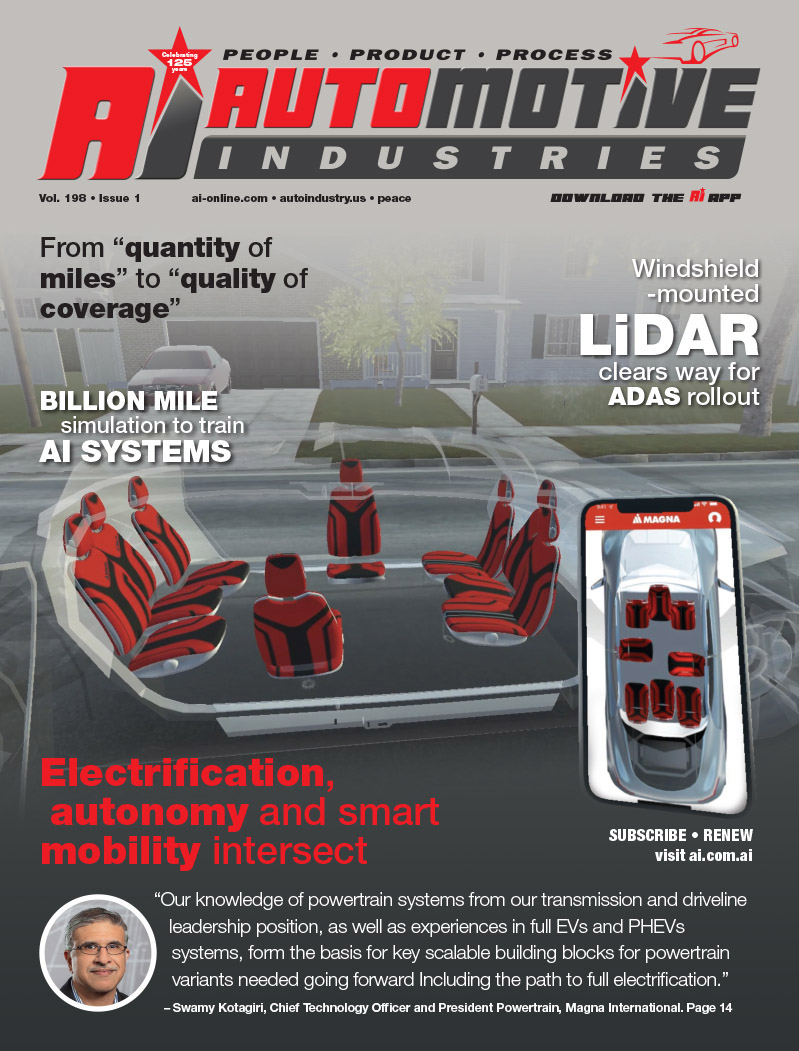
Low-torque bearings are helping to reduce the carbon footprint of vehicles. At present only about 12.6 % of the total energy produced in an automobile is used for moving the vehicle whereas 62% is lost to engine friction, engine-pumping losses and waste heat, 17% idling, 2% in powering accessories and 5.6% in the drive train due to friction and slippage.
Automotive Industries (AI) asked Rohit Saboo, president and CEO of India-based NBC Bearings, how the company is making breakthroughs in low-torque bearing technology.
Saboo: By setting up different teams dedicated to understanding the various torque contributors to the bearing such as grease, the seal and internal bearing geometry. After extensive research and a lot of experiments we finally arrived at low-torque bearing technology. In addition, we developed a low-torque grease along with a low-torque seal and optimization of internal geometry to further improve efficiency. These fuel-efficient bearings were engineered for transmission and wheel bearing application of two wheeler segments, and now for other automotive segments (cars, trucks, tractors, etc.).
AI: What has made you the leading exporter of bearings from India?
Saboo: Our products have found widespread acceptance in 25 countries around the world. NEI reported export revenue of US$35-million in FY13-14 contributing 16% to its top line, and beating all other major players in India. NEI’s export journey started with US$5-m in 2009 and has multiplied seven times in five years. This journey has helped NEI to meet the expectations of global OEMs present in India and to be benchmarked and be compared against the best. The Company has taken an aggressive growth trajectory to have 25% share of revenue from exports by FY17-18.
AI: How closely do you work with OEMs and Tier suppliers to develop new solutions?
Saboo: Around two years back, our company underwent a rebranding exercise, one of the results of which was conception of the 4Ds approach and inclusion of a positioning statement (‘Flexible Solutions’) to the new company logo. The 4Ds (Dialogue, Design, Develop, and Deliver) is our methodology to try and anticipate the market’s needs, to work with and understand our customer’s requirement, and to give them an appropriate product. There are several ongoing projects for new and improved versions of products we are already supplying which, if approved by our customers, are then sent into production. With our new R&D and technological capabilities we have found that many OEMs, including international OEMs, would like to work directly with us. In fact in the last two years we have completed 30 partnership projects with OEMs, and this number is continuously increasing. We get a lot of feedback from OEMs and Tier I suppliers, and we try and best to incorporate it into our products, in keeping with our “flexible solutions†philosophy.
AI: How will the Indian auto components sector keep up with other emerging markets in Asia?
Saboo: I can’t help getting an optimistic outlook about the future. Recent studies by respected industry bodies such as the ACMA (Automotive Component Manufacturers Association) place the industry on a Compound Annual Growth Rate (CAGR) of over 17% over the next three years. The domestic auto industry will bounce back, and that, along with the favorable position the Indian auto components industry has in the global market will help us keep abreast of other emerging markets in Asia, Africa and Latin America.
AI: Tell us a little about the innovations NBC has made on its shop floor.
Saboo: We are well aware that it is the shop floor that ultimately defines any manufacturing company. We have implemented 21 new practices, like a new drive for Daily Work Management, which is a fusion of TQM and TPM. We have also implemented new techniques for learning, which we call LUTI (Learning Understanding Teaching and Inspection). However, the most important change that we can implement is cultural. Our manufacturing team has come up with an innovative new approach to attitudinal change called PANCHAS (Participation, Noble Sense, Commitment, Harmony and Self-Motivation). The system has even been published in a book.
AI: What work is NBC doing in the hybrid and electric vehicle sectors?
Saboo: We are working with an iconic German luxury car manufacturer on their electric car project. Our bearings are used in the electric motor. These are specially designed low noise bearings with high performance seals and grease for better performance.
AI: Tell us a little about the positive feedback you have received from satisfied overseas clients.
Saboo: We take any customer feedback, positive or negative, very seriously and take pride in mentioning that several of our overseas clients have given us positive feedback. A key customer of ours – Amsted Rail, for instance, has expressed appreciation for the fact that they have never had an issue with any of our supplied units. ConMet is another highly satisfied overseas customer who has, among other things, singled out our strict adherence to our delivery commitments. In fact, ConMet has recently partnered with us to introduce the revolutionary PreSet® Hub technology for the Indian heavy commercial vehicle market.
AI: How does NBC’s investment in R&D help your customers?
Saboo: The thrust on R&D is helping us address customer requirements better, open new markets & segments and consolidate our position in the established ones. Further, it’s a massive boost to the brand image. The world loves companies that innovate and invent, and we’re slowly pushing ourselves into that category. Our company has filed 13 patents in the last one year. Many new products have been developed and several of the existing ones are being constantly improved. And finally, it has also made us a more attractive employer, not just because of the improved brand image, but because we can offer talented engineers cutting-edge facilities for R&D, something most of our competitors can’t match.
AI: Please tell us more about your R&D Capabilities.
Saboo: Our R&D center employs over 118 highly qualified professionals from reputed universities in India and abroad. Our engineers work on the latest tools to carry out rigorous theoretical analysis and modeling, including FEA, backed up by latest product testing capabilities in a dust-proof environment, including the Simulation Rigs, Endurance Life Test Rigs & Seal Performance Test Rigs. To speed up the entire development process, a prototype shop has been installed. There is sophisticated equipment for advanced material technology, tribology and advanced manufacturing technology. Some of these include a Scan Electron Microscope, a CETR – Tribotester, Ultrasonic Steel Cleanliness Tester and an X- Ray Diffraction machine with features for stress analysis. In addition, we have an in-house Machine Building Department which we use to manufacture and customize special purpose machines.
AI: What technological breakthroughs have you made?
Saboo: They include the low-torque bearing, the Generation-3 Hub Bearing, specially coated bearings for various applications, and versions of the one-way clutch. The Gen-3 Hub Bearing has been made for the rear wheel application. It is precision assembled with a reduced number of components, which reduces chances of failure and increases life. There is also a reduced time in assembly, which drives cost down and improves efficiency. The One-Way clutch is used in two-wheeler self-starting system. Again, it is composed of fewer components as compared to a normal system. It also completely disengages, which increases life and indirectly reduces fuel consumption.
AI: Are there any new materials being used or in the pipeline?
Saboo: We are developing a number of specially coated bearings, which have special properties for specific uses. For example, our bearings with Tungsten DiSulfide coatings are wear and corrosion resistant. Our metallurgical team has their hands full, with several exciting projects on material sciences underway. For instance, we’re doing preliminary research on a new type of material, which has high nitrogen for better corrosion resistance, for making bearings with better life and performance. Then we’re also constantly trying to improve our products/processes by using existing material combinations. One of our endeavours in this regard is evaluating induction hardening heat treatment for Gen-3 bearing with medium carbon steel.
AI: What percentage of revenue does NBC invest in R&D?
Saboo: In the year 2012-13, NBC spent around 2% of its total revenue on R&D, which is more than the industry average of about 1%. There is a growing realization now that to be a relevant player you need to have a great technological base, so more and more Indian manufacturers are increasing their spending on R&D, especially with our multi-national counterparts opening several R&D centers in India. We have raised our R&D spend from 0.7% in FY 10-11 to just under 2% this year. The target is to raise it to 3% in 2016.
More Stories
Lakshmi Prasad Bhatta on the quest for zero road deaths
Cybord TCI – The Future of Manufacturing Integrity
Flexible Magna Manufacturing Solutions: The Key to Success in the Automotive Industry