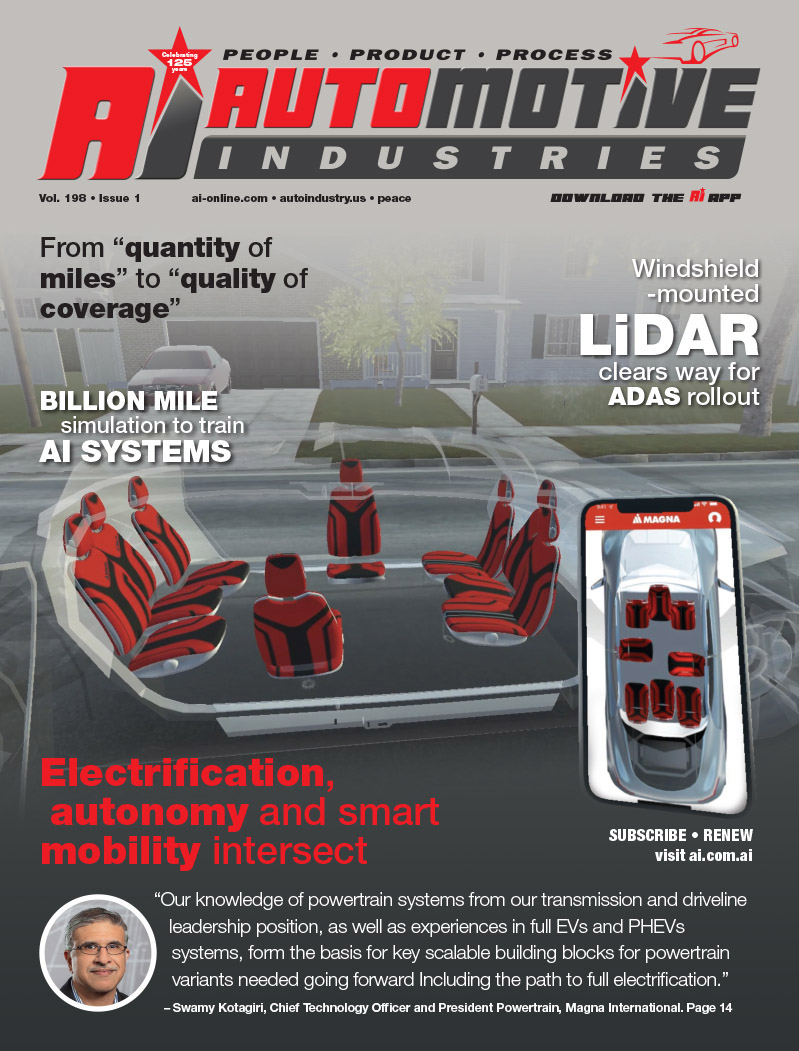
When introducing the redesigned flagship 2014 Mercedes-Benz S-Class, the OEM said the design revolved around three engineering priorities: Intelligent Drive; Efficient Technology; and the Essence of Luxury. Mercedes defines the Essence of Luxury as “perfection to the last detail. The S-Class is not just a technological spearhead for Mercedes-Benz but for automotive development as a whole,” says Mercedes-Benz in its promotional material. One of the technologies the S-Class is spearheading is the use of aluminum. It is built on a hybrid aluminum body shell and formed with aluminum outer body panels.
Automotive Industries (AI) asked Roland Harings, Novelis Vice President for global automotive, what the company’s role had been in the development of the new Mercedes- Benz S-Class.
Harings: Novelis supplies aluminum solutions for all the hangon parts of the new Mercedes-Benz S-Class. For the critical outer hang-on panels such as hood and door outers and fender, Novelis is supplying its Ac-170 PX alloy, which was especially designed for the automotive industry for complex hemming requirements. For the hood inners multifaceted requirements like high formability, good hemming characteristics and pedestrian safety are achieved with Novelis’ Ac-118, a highly formable alloy for inner applications. The achievement of a high pedestrian safety through Ac-118 is especially significant since safety is Mercedes-Benz’ top priority. The company is setting new standards with the S-Class with an entirely new range of extraordinary safety features.
AI: And in terms of innovation?
Harings: One of the latest Novelis’ innovations applied in the new Mercedes-Benz S-Class is the remote weldable alloy Ac- 200 RW, which is a unique multi-layer aluminum sheet product based on Novelis Fusion™. This breakthrough remote weldable alloy delivers a solution to the industry’s long-time challenge of joining aluminum in automotive production. With Ac-200 RW customers can weld without using filler material, which is typically required in welding conventional sheet. This improves customers’ welding speeds. Components can be welded using higher-speed remote welding methods used for steel panels. (Improves welding speed three-fold (from 5m/min to 15m/min)) Ac-200 RW also offers car manufacturers significantly greater design flexibility by allowing them weld one-side components instead of using a C frame (where limited space is a problem) and therefore, makes assembly easier. This remote laser welding technique can lower customers’ joining costs similar to the level of the costs for joining steel, while still delivering the benefits of lightweight aluminum. (Reduces customer joining cost from €1/m (conventional aluminum) to €0.3/m.) Novelis is the only supplier to provide a multi-layer aluminum sheet product for remote laser welding and the only supplier of a fast-welding aluminum solution developed specifically to meet automotive industry production needs.
AI: Can you tell us about your co-operation with ThyssenKrupp Tailored Blanks?
Harings: In cooperation with ThyssenKrupp Tailored Blanks Novelis has developed Tailored Aluminum Blanks. With this innovative technology, individual aluminum sheets of different grades, thicknesses and coatings can be joined to produce customized stamping blanks used by car makers for the production of lightweight body parts such as doors and hoods, and structural components including cross members and longitudinal members. The targeted use of materials in the tailored blanks allows for the elimination of reinforcements and overlapping joints that would otherwise be required, thus saving material, reducing total weight and cutting cost. The gains in process efficiency and the reduction in vehicle weight will further contribute to reduced CO2 emissions for car manufacturers. Tailored aluminum blanks can also contribute to improved crash performance through the selective use of high-strength aluminum alloys. Tailored aluminum blanks extend the possibilities for advanced and economical lightweight solutions in vehicles. Material expertise with aluminum and know-how in tailoring of lightweight solutions are coming together in a unique way to provide this cost-effective technology on a global scale.
AI: What are you expansion plans for the future?
Harings: Demand for aluminum sheet for Body in White is rising by about 25% on average per year globally, not just in North America. Novelis is investing US$200 million to add 200,000 metric tons of annual capacity for automotive sheet in our Oswego, NY plant. Additionally, we are investing US$100 million to add 120,000 metric tons of automotive sheet capacity in Changzhou, China. To meet our global commitment to increase the amount of recycled metal input Novelis is expanding its recycling capabilities worldwide, including a new recycling operation in Nachterstedt, Germany. The new facility is currently being constructed adjacent to the company’s existing aluminum rolling mill and will annually recycle up to 400,000 metric tons of aluminum, including automotive sheet, annually to help feed the Novelis manufacturing operations across Europe.
AI: How do you determine Novelis’ global footprint?
Harings: Novelis is the world leading producer of aluminum flat rolled products for the automotive industry and constantly bringing new levels of weight reduction, innovation and sustainability to the market. With a global market share of more than 50%, Novelis holds a very strong supplier position with all major equipment manufactures and auto makers. Through Novelis’ strong global presence and availability, the company serves the individual needs of customers in key markets in Asia, Europe and North America. In addition to our global expansions to respond to the escalating demand for automotive sheet, Novelis has opened its first Chinese offices in Shanghai and has put in place a Global Automotive Organization to reinforce our commitment and service to automotive customers.
AI: What are your recycling targets and what efforts do you make to achieve them?
Harings: The company’s goal is to dramatically increase the recycled content of its products across its global operations to 80% by 2020. Not only did we make a substantial step towards our goal of 80% recycled content in our products with an increase of 6% (from 33% to 39%), but we also achieved reductions in our four primary environmental targets. In addition, we began investments totaling approximately $1.4 billion in operational expansions and increased recycling capacity needed to help both meet expected demands in the aluminum market and fulfill our recycling target. This is a challenging target particularly for automotive due to the long life of vehicles. It’s absolutely something we are working on from an innovation perspective. Novelis works to include agreements to buy back scrap metal not used during the stamping process and facilitate closed loop recycling. Jaguar is an example of a customer with this arrangement.
AI: What are the new trends on the horizon and what will they bring to multi-materials body structures?
Harings: We believe that the future for automotive is a multi-material design. Given the unique properties of aluminum—particularly in sustainability, light weighting, high performance and durability, we see a major growth trend in the use of aluminum in particular. Materials such as aluminum, steel, plastics and magnesium not only need to co-exist but need to work together in vehicle design. Multi-material joining and forming are areas that will continue to grow in importance in the future. Much progress has been made to date, with more to come. So what will the automobile of the future look like? It will be lighter, safer and greener. To get there, the materials status quo will give way to a changing mix of old and new materials and aluminum will continue to grow in vehicle applications.
More Stories
AUO Returning to CES Showcase Next Generation Smart Cockpit 2025
Donaldson Ultra-Web technology aims to set the standard in industrial filtration for cleaner air and cost-savings
Hydrogen’s Role in Decarbonising Sports and Entertainment Events