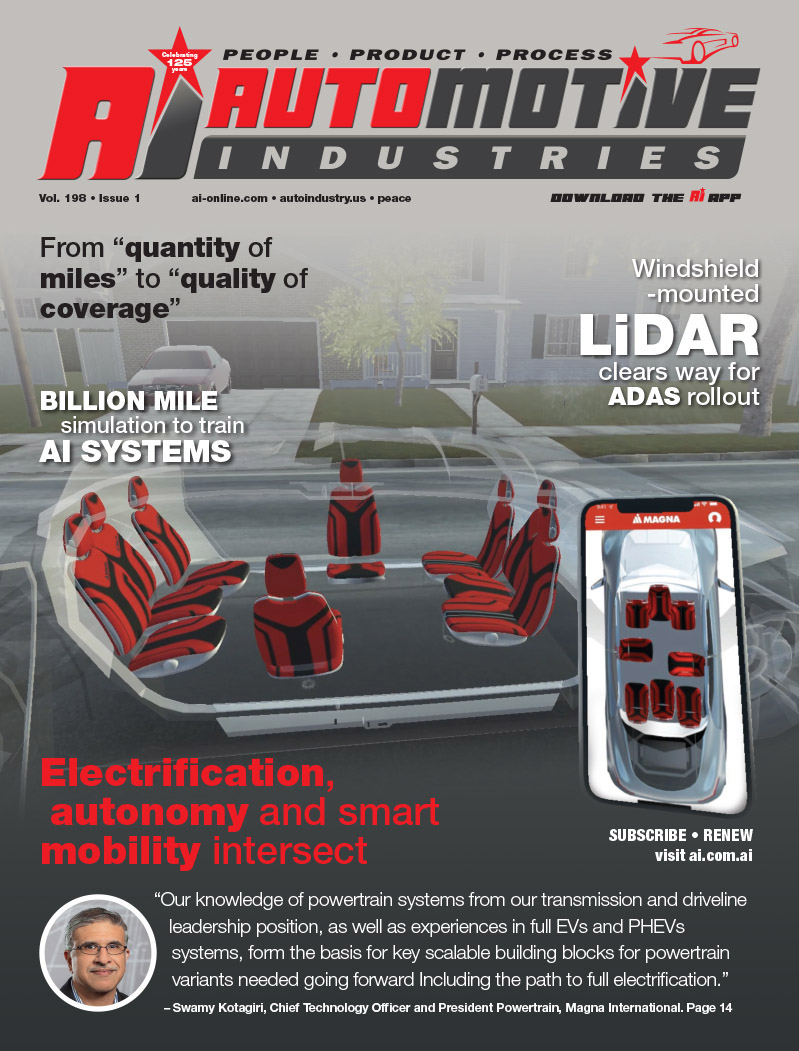
Automakers are accelerating their shift to aluminum away from other materials for new car and light truck construction, as they seek to safely and cost-effectively lower the weight of vehicles according to a new survey of North American automakers conducted by Ducker Worldwide. The survey of automakers indicates that since lighter vehicles get better fuel economy with fewer emissions, aluminum is already the leading material in the engine and wheel markets and is fast-gaining market share in hoods, trunks and doors. The survey estimates automakers will increase their use of aluminum from 327 pounds in 2009 to 550 pounds in 2025.
The survey also shows continued growth in automaker’s overall use of aluminum reaches an all-time high of 343 pounds per vehicle in 2012 – up five percent from 327 pounds in 2009. Aluminum usage has increased every year for nearly 40 years. Longer term, the report predicts aluminum is expected to double its share of the average automotive materials mix to 16 percent by 2025(1) with future cars and light trucks reaching a predicted average of 550 pounds of automotive aluminum per vehicle. As the Obama Administration considers stricter fuel economy regulations, automakers are expected to lower the overall weight of vehicles by approximately 400 pounds per vehicle, and as aluminum use increases, the mix percent is expected to double.
“This new survey of automakers makes clear that in terms of new vehicle designs to greatly step up fuel economy…aluminum’s time has come,” said Randall Scheps, Chairman of the Aluminum Association’s Aluminum Transportation Group and Marketing Director at Alcoa, Inc. “Cars and trucks will get lighter and more efficient, but thanks to aluminum, they won’t have to get smaller or less safe.”
“We are fast-entering a transition stage to more holistic vehicle design approaches premised on greater use of lighter, stronger and more crash absorbent aluminum alloys replacing less efficient iron and steel. Vehicles with their size maintained, but downweighted with aluminum are inherently more efficient than heavier ones,” said Scheps.
“Most importantly in this holistic approach, downweighting is actually an enabler of cost savings across the vehicle by accommodating downsized powertrains and parts consolidation – all without sacrificing safety or performance. A lighter car can allow for a smaller, less expensive drive train and generate the same performance as the original vehicle…more cost-effectively, safer and most importantly in a more fuel efficient manner,” added Scheps.
Aluminum Hoods, Trunks, Doors and Bumpers Drive Growth
Aluminum is already the leading material in powertrain and wheel applications and the survey indicates it is quickly gaining market share in hoods, trunks, doors and bumpers. Body, bumper and closure content grew by 58 percent from 2009 to 2012, with 30 percent of all hoods on 2012 vehicles being aluminum; saving a total of 100 million pounds of vehicle weight across the entire fleet. Twenty percent of all bumpers in 2012 will be aluminum.
According to the report, future growth in auto aluminum usage will be primarily driven by these and other applications being converted from steel. For example, the trend line for aluminum hood penetration predicts a minimum share for aluminum of 41 percent by 2017 and 53 percent by 2025.
Consumer Demand and Regulatory Guidelines on Fuel Economy Drive Growth
Based on consumer demand and a desire to increase fuel efficiency, this past July the Obama Administration announced an agreement with the nation’s automakers, supported by leading environmental groups to increase fuel economy standards nearly 100 percent by 2025, from the 2008 base year 26.3 miles per gallon to 54.5 mpg. The yet to be finalized plan calls for a 5 percent average annual increase in fuel economy for cars and a 3.5 percent annual increase for light trucks through 2021. After 2021, both cars and trucks would face a 5 percent annual increase.
“New, stringent federal fuel economy regulations, coupled with consumer angst about high and unstable gas prices, is leading automakers to move quickly with a total rethinking of vehicle design as they also push ahead with alternate power trains, new technologies and advanced materials. In terms of boosting fuel economy and cutting tailpipe emissions, aluminum offers automakers the fastest, safest, most environmentally-friendly and cost-effective way to get the job done. Low-density aluminum is a game-changer and automakers are moving quickly to take full advantage of all the consumer benefits it provides,” said Scheps.
GM Leads in Aluminum Usage
The survey also looked at average aluminum content by North American automakers, declaring General Motors the content leader at 366 pounds per vehicle. Honda leads aluminum content as a percent of curb weight at 10.7 percent in 2012.
The latest model vehicles boasting above average aluminum content (more than nine percent of vehicle curb weight) include the Chevrolet Malibu, Cadillac CTS, Ford Explorer, Ford Focus, Ford Escape, Lincoln MKZ, Chrysler C sedan, Honda Civic/CR-V, Honda Accord, Nissan Altima, Toyota Avalon and Fiat 500.
“These real world examples complemented by a significant body of research confirms aluminum can take out significantly more weight safely than even newer steels, while remaining cost competitive and having a lower overall carbon footprint than any other competing material, doing it safely and in many instances helping to lower costs,” Scheps says.
On a segment basis, the survey points to future growth areas in mid-size and large sedans as well as full-size full frame vehicles (i.e. light-duty pick-up trucks) mainly due to the comfort, safety and functionality requirements expected from the customer.
Cost Competitive Weight Savings
As automakers apply aluminum to reduce the weight of their vehicles, the focus is increasingly toward the system cost, which allows aluminum to compete successfully with other materials because of the advantages it brings in primary and secondary weight savings, fuel savings, structural performance and design flexibility. In fact, secondary cost savings that come from using automotive aluminum can offset cost premiums helping make aluminum a more cost-effective solution. According to the report, the cost of the materials upgrade is estimated at less than $500, even before secondary cost savings from downsized components are factored in.
“Downweighting will be at the core of whatever other technology, design and powertrain changes are coming,” said Scheps. “Using aluminum will extend the efficiencies of other technologies, while enabling secondary cost-savings from downsized powertrains without sacrificing performance.”
Other Highlights from the Report
The average increase in aluminum content since 1975 has been seven pounds per year per light vehicle.
Automakers will, on average, seek to lower the weight of cars and light trucks by at least 10% by 2025.
Market factors already in place are projected to push aluminum content to 400 pounds per vehicle in 2015/2016.
Aluminum is gaining market share at the expense of both traditional and high strength steels (HSLA), which are declining as a percentage of vehicle makeup.
Advanced High Strength Steels (AHSS) also are growing at the expense of inferior steels, but gauge reduction with AHSS provides limited weight savings potential compared to using lower density aluminum. Pound for pound, aluminum replaces more than twice as much weight as AHSS.
“This is an exciting time for the auto industry and for aluminum,” concludes Scheps. “We are at the leading edge of a large scale conversion from heavy steel to aluminum and the consumer and the environment will be the ultimate beneficiaries.”
A webinar to review the detailed results of this survey, commissioned by the Aluminum Association, Inc., will be hosted on Friday, September 23, from 12-1 p.m. Eastern. To register for the webinar or for more information on the survey and the overall advantages of automotive aluminum, visit www.aluminumintransportation.org or call (248) 975-2800.
(1) Using the Environmental Protection Agency’s (EPA) 2008 baseline vehicle in which aluminum components totaled eight percent of vehicle curb weight.
About the Aluminum Association
Through its Aluminum Transportation Group (ATG), the Aluminum Association communicates the benefits of aluminum to help accelerate its penetration in ground transportation applications through research programs and related outreach activities. The ATG’s mission is to serve member companies and act as a central resource for the automotive and commercial vehicle industries on aluminum issues. Members of the ATG include: Alcoa Inc., Novelis Inc., Rio Tinto Alcan, Aluminum Precision Products Inc., Kaiser Aluminum Corporation, Hydro and Sapa Group. Visit the ATG online at www.aluminumintransportation.org.
More Stories
Meet Rita Case – recipient of 2024 NAMAD Lifetime Achievement Award
Automotive Industries (AI) Newsletter October 2024
New Infineon Bluetooth range designed to meet OEM needs