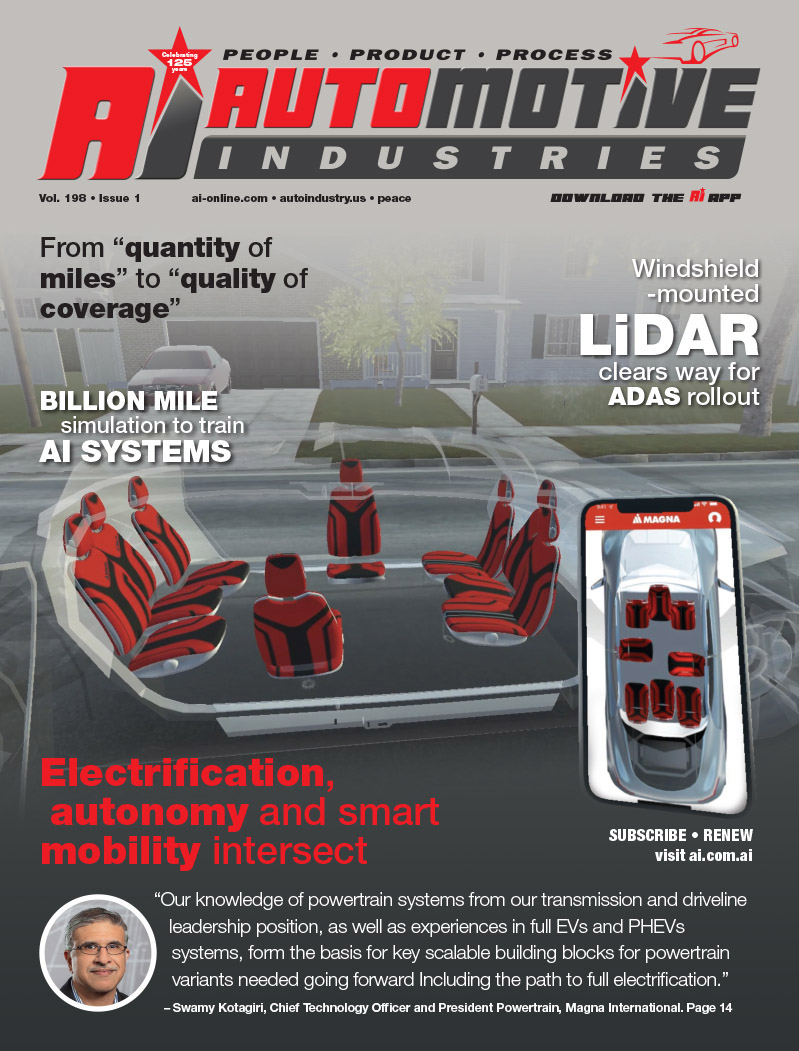
GKN Driveline has nearly 40 electric and hybrid-electric vehicle projects currently underway for major automakers around the world, signaling a major push within the industry to speed development of electric cars and light trucks.
“Interest is especially high among vehicle manufacturers hoping to convert an existing front-wheel-drive platform to an all-wheel-drive hybrid program,” said Dr. Ray Kuczera, vice president of engineering for GKN Driveline Americas. “This type of conversion has the potential to increase fuel economy by up to 35 percent.”
He noted that GKN Driveline has furnished more than 250,000 electric rear-drive axles to Nissan and Mazda in Japan over the past 10 years, giving the company considerable experience in this rapidly growing market segment.
“In parallel with hybrids, interest in electric cars and vehicles with extended range capability has been apparent at auto shows for several years,” Kuczera added, reporting that GKN Driveline also has developed eTransmissions for three electric-car programs scheduled for production in Asia and North America.
The company relies on two competitive strengths for its rapidly growing electric axle and transmission business:
— For hybrids, the company has a patented disconnect system that turns its
eAxle (electric-drive axle) off in less than 80 milliseconds to improve
efficiency when the axle is not needed. When torque is required, the
axle turns back on in about 100 milliseconds.
— For electric vehicles, GKN Driveline has developed three families of
ready-made eTransmissions that can be inexpensively tuned to meet
different vehicle requirements.
“What counts for our customers is our ability to complete development projects quickly and at a relatively low cost,” said Max Owen, president, GKN Driveline Americas.
Owen said GKN Driveline currently has several major electric and hybrid-electric development programs with U.S. automakers and expects to add more before year-end.
In Europe, the Peugeot 3008 HYbrid4 equipped with GKN Driveline components goes on sale this year followed by two other Peugeot-Citroen vehicles with GKN Driveline solutions – the Peugeot 508 HYbrid4 and Citroen DS5 HYbrid4.
The Peugeot 3008 HYbrid4 — a crossover with a 120 kW diesel engine to drive the vehicle’s front wheels and a 27 kW electric motor for its rear axle — can travel short distances on electric power alone. It also can operate in four-wheel-drive for maximum performance and road grip and can run on the highway for hours with an efficient 2.0-liter diesel equipped with a particulate filter. Fuel consumption for the Peugeot hybrid is about 35 percent less than for vehicles of comparable size and performance.
GKN Driveline’s axle business for pure electric vehicles began with a modular approach, as engineers created three standard families of eTransmissions to drive front and/or rear axles on small city cars, standard mid-range cars, large premium sedans, SUVs and sportscars.
Within each transmission family, the company only needs to change two gears inside a common gearbox to adapt to different motor speeds, power levels and wheel speeds. Standard products can be customized to meet individual vehicle manufacturer requirements, helping to reduce both cost and development time. GKN Driveline can provide prototypes in three months and be in series production within 18 months.
GKN Driveline’s ability to meet aggressive production schedules helps automakers reduce product-development costs and introduce new products ahead of competitors. Its eTransmissions are compact, lightweight and 96-percent efficient, offering the final consumer vehicles with greater range at lower cost.
“We are currently developing eTransmissions for 15 different projects and have confirmed eTransmission orders for electric vehicles in Europe, Asia and North America,” said Kuczera.
GKN Driveline currently supplies more than 40 percent of the world’s standard front- and rear-wheel sideshafts and is introducing new driveline-system technologies to take advantage of all-wheel-drive safety and handling features while minimizing the impact on fuel economy.
For conventional (non-hybrid) vehicles, for example, GKN Driveline has designed a “disconnecting” all-wheel-drive system that completely decouples a vehicle’s rear driveline when not required. The system reconnects swiftly and seamlessly when needed.
Through the use of synchronizers and clutches, the propshaft and elements in the rear-driveline module can stop rotating when all-wheel-drive is not required. Eliminating unnecessary driveline motion can lead to significant improvements in all-wheel-drive fuel economy.
“Although the concept sounds rather simple, making it happen represents a major challenge,” Kuczera explained. “Accelerating the vehicle driveline from zero to several thousand RPM in a fraction of a second is only one part of the equation – it also must be silent and completely transparent to the driver and passengers alike.”
In addition to its market-leading positions in eDrive Systems, GKN Driveline’s product segments include: CVJ Systems; AWD Systems and Trans Axle Solutions.
About GKN Driveline
GKN Driveline is the world’s leading supplier of automotive driveline systems and solutions. As a global business serving the leading vehicle manufacturers, GKN Driveline develops, builds and supplies an extensive range of automotive driveline systems – for use in the smallest ultra low-cost car to the most sophisticated premium vehicle demanding the most complex driving dynamics.
GKN Driveline is a leading global producer of CVJ systems, AWD systems, Trans Axle solutions and eDrive systems.
www.gkndriveline.com
About GKN Group
GKN plc is a global engineering business serving mainly the automotive, aerospace and land systems markets. It has operations in more than 30 countries, around 38,000 employees in subsidiaries and joint ventures and had sales of 5.4 billion pounds in the year to 31 December 2010. GKN plc is listed on the London Stock Exchange (LSE: GKN)
www.gkn.com
GKN Driveline’s product segments include:
CVJ Systems
— GKN Driveline’s constant velocity joint systems provide space, weight
and fuel savings with greater all round efficiency.
— GKN Driveline supplies the most extensive range of CVJ systems – used in
the smallest ultra-low cost car through to the most sophisticated
premium vehicle.
AWD Systems
— GKN Driveline has full all-wheel drive systems capability.
— GKN Driveline’s all-wheel drive couplings improve vehicle handling,
stability and traction by intelligently distributing power, and
disconnecting technology can supplement low drag and inertia for
ultimate efficiency.
Trans Axle Solutions
— GKN Driveline produces highly durable open differentials and has the
most extensive range of limited slip differentials (LSD), from the
smallest super LSD to the largest electronically controlled axle locker.
— For the ultimate capability, GKN Driveline’s torque vectoring solutions
provide the answer.
eDrive Systems
— GKN Driveline’s pioneering electric drive technology is used in 250,000
vehicles today.
— GKN Driveline’s eDrives are designed for the new generation of fuel
efficient, low emission electric and hybrid vehicles.
More Stories
Flexible Magna Manufacturing Solutions: The Key to Success in the Automotive Industry
Automotive Industries (AI) Newsletter October 2024
Automechanika Shanghai 2024