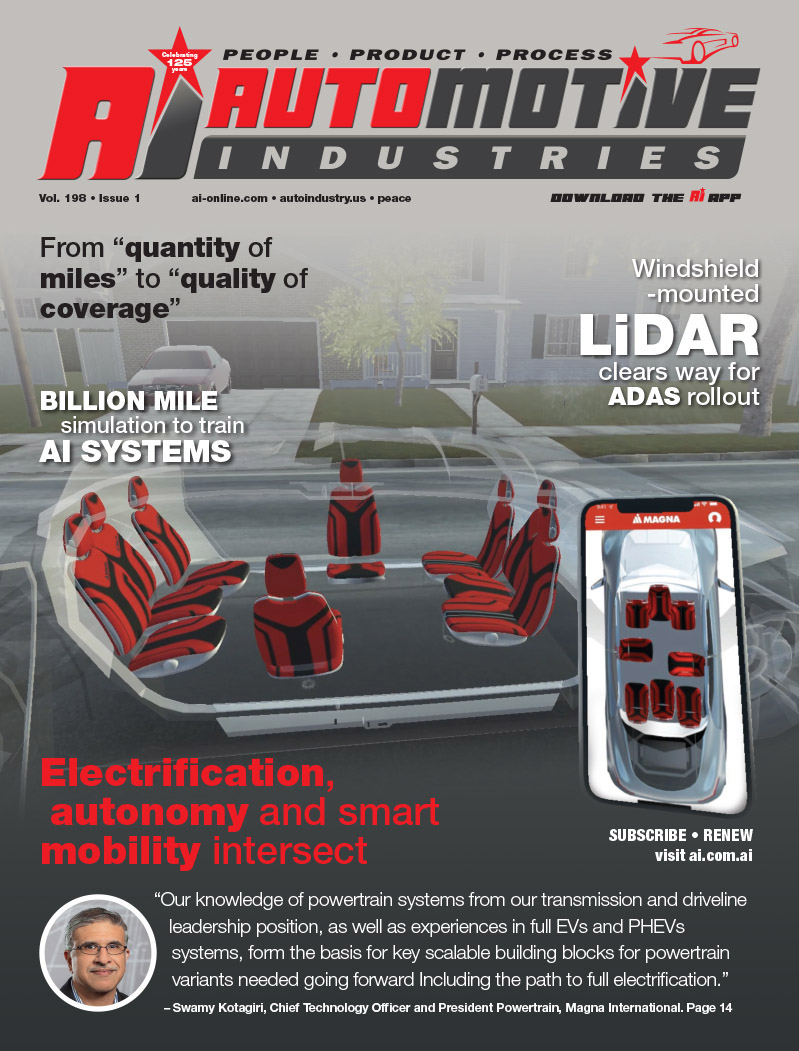
The nectar of internal combustive invention is generally milked from the dangerous swagger of pace, not the pedestrian commute to curtail it.
It often seems braking technology is acceleration’s unwelcome side project, attracting scant concern from automotive engineers who appear infinitely more interested in the rakish transfer of sheer horse power to physical momentum. And who could blame them? Speed is Elvis, after all, and braking is for squares, man.
One only has to examine the development of the technology involved in these diametric endeavours to understand where the historical impetus of automotive R&D lay. In the zealous quest for speed, stopping is apparently an afterthought, as if life’s dowdy, fastidious administrator stubbornly tugged the automotive manufacturers’ sleeve and tiresomely asked: “I know you don’t care if you die in a squealing high-speed crash, but what about me and the kids?!”
(This would, I imagine, inspire a Doh! moment Homer Simpson could justly pursue to copyright litigation. Thereafter the sheepish gearheads would reluctantly shoehorn in a couple of extra seats and, muttering, bolt on a brake or two.)
As the technology that drove cars to go faster progressed, advances dwindled from great lunges to micrometric increments: refinement sharpens the cutting edge that shaves itself ever thinner. Especially in motor sports, where mere hundredths of a second can so easily describe first place from, well, death. By comparison, brake technology advanced inversely, with little change occurring in the early days of motoring to increasingly rapid improvements over the last thirty or forty years. One only has to drive a sports car from the 50s or 60s into a corner at anything approaching an athletic velocity to experience the difference between then and now: every bodily orifice startlingly puckers uncontrollably the first time you stamp on the relatively useless brake pedal. This vigorous full-body alarm viscerally demonstrates how urgently brake systems have evolved in more recent years.
Ye Olde Drum Brakes
In the world of brakes, the day of the drum is done, even though the drum brakes of today are more efficient than the discs of the 70s. There aren’t many (if any) automakers that still use drums on the front wheels, where more efficient disc brakes are usually employed to do the lion’s share of braking. The main reason they are still used on rear wheels is a result of cost: drum brakes are much cheaper and easier to implement as a parking brake (rear discs require a separate parking brake facility to be installed). Although cheaper to produce, their main failing is their comparatively inadequate heat dissipation, which is essentially what brakes are designed to do: convert kinetic energy into heat energy and disperse it as efficiently as possible.
Discs
In order to aid heat dissipation, disc designs have for years incorporated cross-drilled holes (increasing surface area), especially in performance designs where regular replacement due to wear isn’t such an issue, and have moved from being solid cast iron units with opposing contact surfaces to two relatively thin contact discs separated by fins or vanes (often still a single piece of cast iron). This allows air to flow magnanimously around the unit, vastly increasing the cooling efficiency.
Racing Discs
Racing applications often include slotting the contact surface, where shallow channels are machined into the disc at an angle to the direction of motion that aid in removal of debris, gas and water. This technique is not often used for road cars as the wear on the pads is obviously quite rapid. Air ducting is often introduced (usually to the underside of the car) to channel airflow to the centre of the disc in further effort to increase cooling, as is the addition of dedicated electric brake disc fans.
Brake Pads
A brake pad’s effectiveness is measured by the dynamic friction coefficient “µ”, which is the ratio of the friction force compared to the force pressing the two surfaces together. Most standard automobile brake pads range from 0.35 to 0.42, while high performance brake systems can reach up to 0.62. The best materials have a coefficient that remains fairly constant as temperatures change. If the material’s coefficient changes too much when hot or cold, the brakes may fade or grab: both undesirable results when either travelling at speed and/or sipping a hot cup of coffee.
The dissipating of heat, therefore, is the primary impetus behind brake development, both in design and materials technology. The main evolution has been in brake pad and disc materials and configurations, primarily driven by the racing industry, where efficiency translates directly into dollars.
The higher the coefficient of dynamic friction rating for the material, the better brake pad it makes, which led to asbestos being used extensively for decades, largely because of its toughness and heat-resistant properties. As the health dangers of asbestos dust became apparent, however, aramid began to replace it; a synthetic fibre asbestos substitute often used in ballistic body armour. Kevlar or fibreglass can also be used.
Composites
Composite brake pads generally consist of a material, such as aramid, infused with copper or iron fibres/dust to provide increased heat dissipation and increased friction for greater braking power. This does tend to make braking louder, however, and is more abrasive on iron discs.Â
Want to learn more about current technologies and developments in braking systems?
Visit our download centre for more articles, whitepapers and interviews: http://bit.ly/braking-articles
More Stories
Flexible Magna Manufacturing Solutions: The Key to Success in the Automotive Industry
Automotive Industries (AI) Newsletter October 2024
Automechanika Shanghai 2024