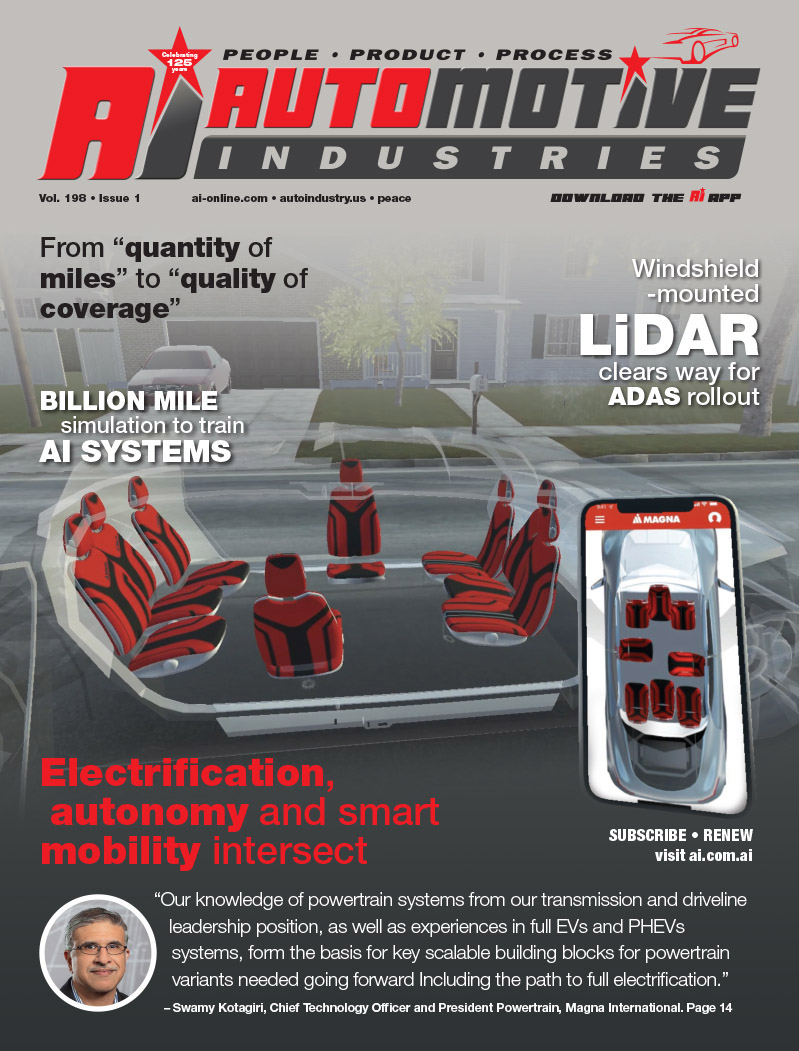
Working together with LMS Imagine.Lab engineering services, Delphi engineers use LMS Imagine.Lab AMESim multi-domain system modeling software to efficiently develop advanced HiL simulators to design and test electronic control units for tomorrow’s fuel-efficient, clean-running diesel engines.
Carmakers, engine manufacturers and companies across the automotive supply chain are scrambling to keep up with the rapidly expanding market for diesel-powered vehicles. About half the cars sold in Europe are diesel powered, and global demand is expected to increase by more than 80% in the next ten years – from 16 million vehicles to 29 million. Up to 40% more fuel efficient than gasoline engines and sixty times cleaner than engines made twenty years ago, diesels are selling like never before.
One of the major design challenges focuses on efficiently developing hardware-in-the-loop (HiL) systems that simulate car and engine behavior. With accurate HiL systems, engineers can calibrate and test the engine control unit (ECU) early in the cycle before vehicle prototypes are available; engineers can also perform more comprehensive tests reducing the use of prototypes. Normally software programmers would spend months updating the entire code along with each new engine and vehicle prototype.
There were a few glitches in this process. It took enormous amounts of time and model completion depended on a final detailed vehicle design and available CAD models. Not to mention, every time the ECU, engine or vehicle design changed, the HiL system programmers could start again from scratch. Even then, the solution wasn’t foolproof. Many conventional control-system models fail to provide real-time simulation response and often do not fully represent all the behavioral aspects of the subsystems. To be certain, engineers still performed several rounds of prototype testing on vehicle mock-ups to fine-tune the ECU’s final design.
Stopping the bottlenecks
How to eliminate the bottlenecks and speed up the process? One of the largest and most diversified suppliers of automotive parts in the world and a global leader in diesel fuel injection equipment and engine management systems, the Delphi Corporation selected LMS Imagine.Lab AMESim system modeling software. Suitable for multi-domain usage, this technology let engineers perform mechatronic simulation of systems with electronic and mechanical hardware, including hydraulic, pneumatic, combustion and thermal physics.
Delphi selected LMS Imagine.Lab AMESim for HiL development because of its track record. The company had a previous successful experience using the software to modeling fuel injection systems. Delphi trusted the proven expertise of the LMS Imagine consulting services and the background of the highly-skilled engine control applications team.
In addition to its advanced modeling functionality, one of the LMS Imagine.Lab AMESim’s greatest advantages is that you don’t need to be an expert programmer to build models and run simulations. Engineers themselves create system simulation models by graphically selecting and connecting pre-defined components from the different libraries. Based on these selections, LMS Imagine.Lab AMESim automatically generates a working physics-based model of the system. Because a highly accurate HiL model is created so quickly and completely early in the development cycle, engineers have time to work out problems and optimize the design up front. This means less prototype testing and fine-tuning later in the process.
Building accurate models in record time
Delphi decided upon the LMS Imagine.Lab AMESim Engine Control solution specially configured for modeling engine and vehicle systems. To kick off the implementation, the company turned to LMS Imagine consulting services to develop a model specifically for HiL applications. The complete model contains representations of the diesel engine, fuel injection system, thermal aspects and driveline. All parameters are represented in a single model for the ECU functional tests and calibration of engine control codes.
The engine model developed with the LMS Imagine.Lab AMESim IFP-Engine library consists of a Mean Value Engine Model (MVEM) associated with a complete air path including the intake circuit with turbochargers, the exhaust circuit and the EGR loop. Delphi engineers could simulate the complete cycle-by-cycle engine behavior. With a manageable computational load, they obtained highly accurate results regarding engine performance without waiting days to get results. The engineers could also access more detailed high-frequency engine models available in LMS Imagine.Lab AMESim to represent combustion chamber behavior (including thermal exchanges and the action of valves, connecting rods, etc.) in minute steps through the complete engine cycle. The model for the fuel injection system represents the engine’s HP pump, a rail volume and a high pressure valve. Thermal aspects of the engine are modeled with the thermal library. The driveline model is built using components from the IFP-Drive library, including the flywheel, engine friction torque, clutch, gearbox, braking system and main auxiliaries.
The close collaboration between LMS Imagine engineering services and Delphi led to the implementation of a complete engine control and HiL process. The first vehicle simulation was developed for an OPAL platform. Delphi noted that the LMS Imagine.Lab AMESim models met their requirements completely in terms of performance, flexibility and real-time compatibility.
Know-how for future work
Introducing more detailed physical representation in the HiL simulators enabled Delphi engineers to save considerable time in modeling and simulation, increase the simulation accuracy compared to previous methods, run many more simulations for studying specific system behavior, and enhance the quality and robustness of models in representing engine components and control strategies. More broadly, the LMS Imagine.Lab AMESim model and associated simulation processes developed with the LMS Imagine engineering services can be readily adapted by Delphi as a methodology for future ECU and HiL projects.
In the long term, the LMS Imagine.Lab AMESim modular approach to creating engine and vehicle system models makes it possible for Delphi engineers to seamlessly develop controls when implementing new technologies in their engine control systems while reducing costs and eliminating delays in maintaining and updating engine and vehicle models as these advances are incorporated in the design. This new process enabled Delphi to satisfy customer expectations and helped to provide ECU with reliable engine control strategies. Delphi was able to answer to the growing stringent demands of car manufacturers regarding safety, reliability and costs control.
“The implementation of LMS Imagine.Lab AMESim and its multi-domain approach for our new-generation HiL simulators significantly helped us to reach Delphi’s strategic objectives,†explains Olivier Lanoux, Development and Validation Tools Team Leader at Delphi. “The new generation of engine models and the comprehensive new methodology made it possible to drastically reduce maintenance operations and development time, and provide reliable and high-quality ECUs and related engine controls.â€
More Stories
Celanese Materials Shine in Multiple Category Winners at 2024 SPE Automotive Innovation Awards
New future-ready single-slot PXIe controller for high-performance T&M applications from Pickering Interfaces
US Army Awards ANELLO Photonics Contract Phase II SBIR Topic “xTech Search 7 SBIR Finalist Open Topic Competition”