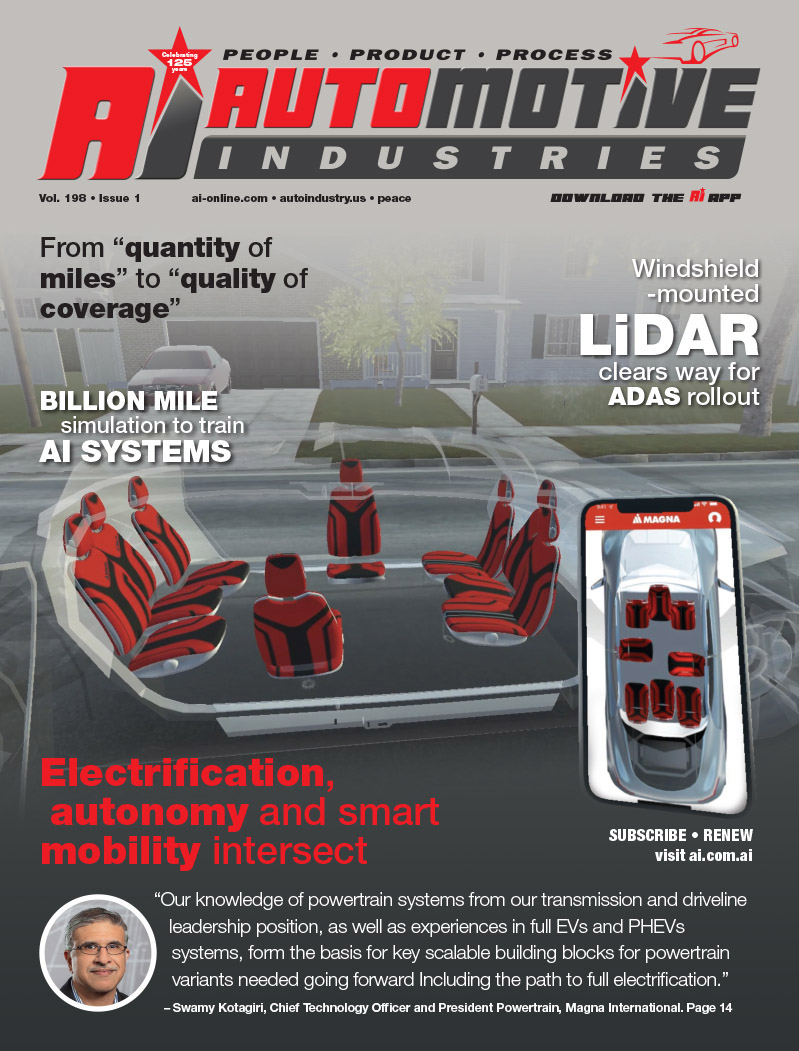
If your company manufactures camshafts and crankshafts for the automotive industry, you know that production tolerances will continue to tighten as the demand for greener vehicles increases. The need to improve engine life performance, fuel economy and reduce emissions will continue to evolve, resulting in the need for more precise measurement equipment.
Today, more than 500 major automobile and supplier companies in 31 countries worldwide employ Adcole computerized inspection gages for quality control checks on camshafts and crankshafts. These companies include General Motors, Ford, ThyssenKrupp, VW, Chrysler, Toyota, Fiat, Nissan, Renault, Hyundai, Volvo, Suzuki, Caterpillar, Daimler, BMW, Honda, Cummins, FAW, Tata, MAN, John Deere, SAIC, FAW, and Dong Feng.
Founded in 1957, Adcole has manufacturing facilities in both Massachusetts and Florida and offices around the world, maintaining close relationships with their customers. The company’s success, to a large extent, is based upon responding to their customers’ requests for further refinements based upon their real-world experience. Most of these refinements have dealt with the need for higher accuracy and the need to measure more parameters including radius, profile, taper, crown, timing angle, diameter, velocity, acceleration, runout, and roundness and concentricity. Another key reason for Adcole’s success is their exemplary commitment to R&D.
Adcole maintains its expertise in the critical core competencies of high accuracy optical-mechanical measuring technologies and company know-how by investing 10 percent of revenues in R&D. In addition to manufacturing special purpose machines that measure engine components like camshafts, crankshafts and pistons, the company also makes digital sun angle sensors for spacecraft. Nearly 60 per cent of the company’s business is generated from automotive OEMs and manufacturers of agricultural and construction equipment, motorcycles, outboards, and other small engine manufacturers, while the remaining 40 percent comes from the spacecraft hardware industry. Both market segments share the need for ultra-high accuracy and reliability.
To assure that their measuring instruments live up to their 50 plus year earned reputation for innovation and quality, Adcole gages are assembled, tested, and certified at the company-owned, custom-designed building in Marlborough, Massachusetts. Built in 1983, this facility was expanded in 1998 to accommodate its 200 employees. Adcole’s Florida plant specializes in the production of the high-precision ball-bearing spindles used in their gages.
In response to the ever-tighter tolerances necessitated by developing greener technology engines, Adcole recently introduced the Model 1300 High-Speed Crankshaft Gage. This gage was developed to increase the production of good parts, minimize troubleshooting time, and significantly reduce warranty expenses. “The Adcole Model 1300 high-speed crankshaft gage will virtually eliminate the risk of delivering a bad crankshaft. Designed for operating two or three shifts per day, this rugged measuring machine has a granite base and incorporates a touch-screen operator interface, linear motors, air bearings, and dual optical linear scales for end-of-line accuracy,” said J. Brooks Reece, Adcole vice-president.
Another world class measurement machine enhanced and reintroduced is the Adcole 1310 High-Speed Camshaft Inspection Gage which is an end-of-line machine that can measure up to 200 parts-per-hour for rise error and chattermark detection. Fully automatic, this gage uses individual measuring heads for each journal and cam lobe, with 0.1 micron resolution, taking one data point each 1/10th degrees, or 3600 data points per revolution.
Capable of measuring simultaneously many parameters including radius, profile, taper, crown, timing angle, diameter, velocity, acceleration, runout, and roundness and concentricity, the Adcole 1310 High-Speed Camshaft Inspection Gage is easy to program, Windows compatible, and adjustable followers permit fast changeover for inspecting different camshafts. This machine provides gage room accuracy at production line speeds. Over the past 25 years and through continuous design upgrades, Model 1310 Gages have measured tens of millions of camshafts and helped improve engine performance and longevity for many manufacturers.
These two additions to their family of measuring machines illustrate why Adcole gages have become recognized as “The World Standard” in the engine camshaft and crankshaft quality control world. The firm’s large OEM customers have Adcole gages in their powertrain development labs, plant gage rooms or nearby on the production floor, in addition to 100% in-line production measuring. It may seem incredibly simple, but the advantage to these companies is they know they are manufacturing what they designed and that their end-users are getting the intended product; assuring its intended performance. As the automotive industry continues to become greener, this assurance will become ever-more critical.
More Stories
AUO Returning to CES Showcase Next Generation Smart Cockpit 2025
Donaldson Ultra-Web technology aims to set the standard in industrial filtration for cleaner air and cost-savings
Hydrogen’s Role in Decarbonising Sports and Entertainment Events