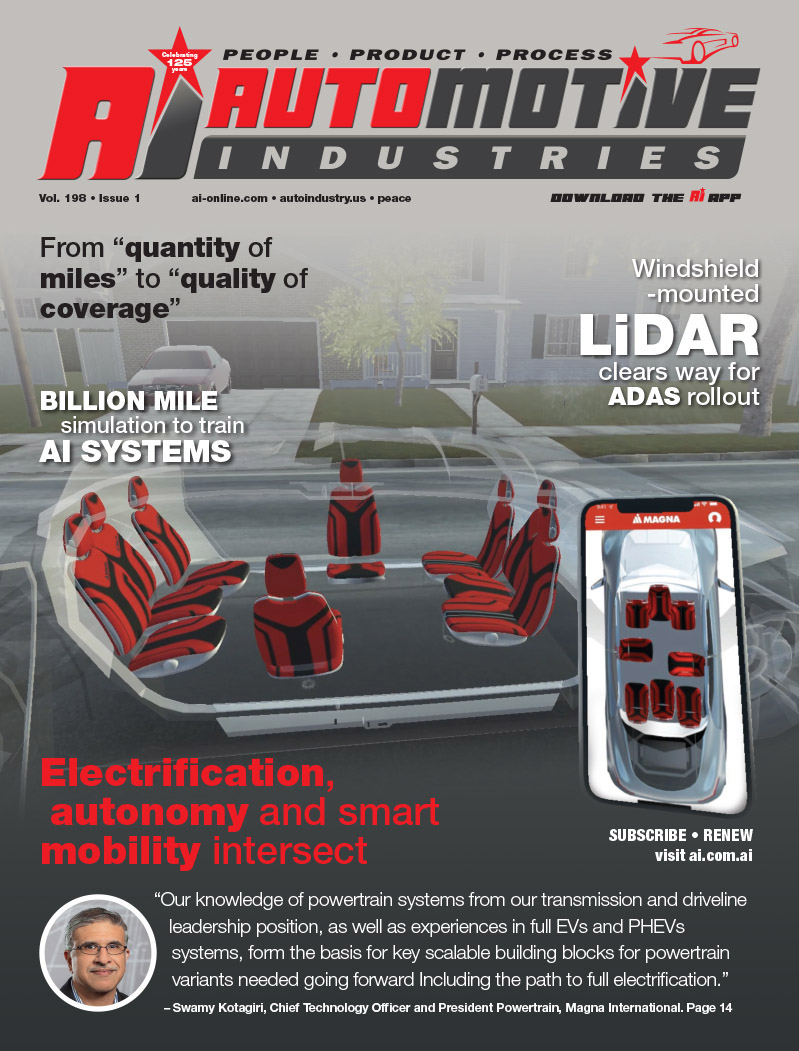
Since the invention of the CCD sensor 40 years ago, the role that digital imaging devices play in process monitoring and quality control has increased steadily in the manufacturing industry as image processing hardware and software has become more powerful and less expensive. The range of products that are available has expanded significantly, while the ease with which such devices can be implemented has increased. The result of these trends is that imaging devices have become ubiquitous in the modern manufacturing operation.
In many cases these devices are not even viewed as imaging devices, but rather as simple sensors. Laser micrometers and 2-D barcode readers are good examples of imaging sensors that have been purpose-built for a specific task, are very simple to implement, and are widely deployed in manufacturing operations. A background in lighting, optics, or image processing software algorithms is not required in order to successfully design and deploy a solution based on these devices. All of that is built into the device itself.
Other applications are more challenging, however, and while the maturation of industrial imaging technology has helped to simplify some aspects of design, construction and deployment, many fundamental challenges remain. These challenges apply not only to systems that utilize visible light imaging techniques, but also to systems that utilize other techniques for non-destructive testing, including ultrasound and x-ray imaging.
Motivation for expanding the implementation of machine vision devices is strong because in many situations they can increase the cost effectiveness of quality control processes, in addition to reducing the potential costs associated with poor quality. It is well understood that human manual inspection is often unreliable. While human inspectors have remarkable detection capabilities and can be very flexible, they are subject to inconsistent detection of defective product. If the cost of allowing poor quality product to reach the end customer is high, then implementation of automated systems can produce a rapid return on investment.
Alignment of inspection techniques and specifications
While automated imaging techniques have become increasingly prevalent in the manufacturing industry, the business and engineering processes that must accompany these techniques have lagged behind in modernization. Many firms that look to implement imaging-based automated solutions are utilizing previously developed specifications based on manual techniques. In some cases, in-house expertise may not be available for aligning product specifications with automated testing techniques. In other cases there may be a reluctance to change protocol and revise a long-standing design or process specification for a product to accommodate a new testing technique. This is understandable, as a great deal of work is often invested in defining and validating such specifications.
Due to the interaction between specification and testing technique, it is important that when a new testing process is implemented, the specification is reviewed and adjusted to accommodate the new protocol. In many cases the inclusion of a specification originally defined around a manual process into an automated system may not be appropriate. In such situations, the overall process should be optimized and aligned based upon the advantages offered by deploying digital imaging technology. In most cases the alignment of inspection techniques and specifications can be accomplished without compromising the manufacturing process.
Application Examples
A product containing a large number of open channels has a specification for the minimum opening size of each channel. The specification states that the opening must be such that a pin gauge of a certain diameter must fit through the opening of each channel. This specification is designed around a manual quality control process in which an operator checks the product by eye, identifies openings that may be partially blocked by debris and which may not meet the specification, verifies each with the pin gauge check and handles appropriately depending on the result of the check.
A machine vision system is capable of inspecting the openings in such a product with a high degree of accuracy and robustness. The system relies on optical rather than mechanical techniques so there are some important differences. Since the specification is defined around the manual technique, it is purpose-built to produce a reliable pass/fail result under those conditions. Utilizing the automated optical technique to produce the same result with the same level of certainty would be inconsequential. Consider the reverse situation, where the specification is written in such a way that it fits the automated imaging approach. In this situation, the specification would most likely be written to control the total open area of each channel. The algorithms behind such a measurement are simple and robust, and can be performed very quickly and accurately with a camera-based system. Such a measurement does not lend itself to a manual process, as there are no hand operated tools that allow an operator to precisely measure the area of an opening. For a specification to be practical to implement, it must take into account the methods that will be used to evaluate conformance.
Manual inspection techniques often rely on the remarkable human ability to quickly and accurately identify objects and patterns against a variable background. In many specifications for defect detection, the specification relies on some degree of such qualitative discrimination by a human operator. Consider the example of a specification for surface damage in a material. Such a specification could read “gouges in the material greater than 25mm in length, 5mm in width or 2mm in depth are not allowed.” At first glance, this specification seems reasonable. An operator can look at a piece, locate any gouges on the piece, and compare them to that specification using a caliper or other measuring device to determine if they exceed the minimum standard. On closer inspection, however, the applicability of the specification becomes less clear. What if there is a feature on a part with dimensions of 0.1mm depth, 0.1mm width, and 30mm length? That exceeds the specification due to the length, but may be considered a “scratch” rather than a “gouge”. What if there is a feature on a part with a dimension of 200mm in width and length, and 0.1mm depth? That also exceeds the gouge specification, but may be considered a surface flatness issue rather than a “gouge”. The specification as written relies on the ability of a human to qualitatively identify the type of defect and make the correct interpretation. This becomes important when considering the implementation of an automated system. In many cases an automated system does not lend itself well to discriminating qualitatively between different types of similar defects. Configuring an automated system to detect defects strictly on the basis of such a specification could result in large numbers of parts being rejected due to detection of features that are not gouges, but fall within the strict interpretation of the specification. Conversely, the automated system may not detect gouge defects that exceed the specification in one dimension, for example length, but which fall below the minimum capability of the measurement system in another dimension, for example depth or width.
It should be noted, however, that in most cases the specifications can be written so that the required discrimination is properly achieved.
Design and inspection compatibility
Intelligent design practices dictate that design of products account for more than simple functionality and robustness. It is also important to include manufacturability, consistent reproducibility and serviceability in the design. One additional aspect that is becoming more important as automated inspection equipment is deployed is inspectability. Designing products for inspectability means taking into account the features that will require automated inspection, and making accommodations to facilitate those processes in the design of the product. As a simple illustration, consider a product that is composed of multiple pieces that are fastened together using cement. For such a product, a critical manufacturing parameter is the seam width. If the bonding cement is the same color and consistency of the pieces that it bonds together, then locating the edges of the seam may be challenging, even for a human operator. Design for inspectability may dictate that the product designers consider adding a colorant to either the base material or the cement that would allow an automated imaging system to consistently locate the edges of the bonds to produce an accurate seam width measurement.
Design for inspectability may also include adjustment of production processes to require that inspection processes occur at stages of production where the evaluation can be more effective. For example, if a material is to be inspected for detection of cracks in the surface, it is much more effective to inspect the material prior to application of any coating material such as paint that may cover the cracks. This may seem like an obvious point, but in situations where there are multiple handoffs between various business units that may be involved in the overall manufacturing campaign, it can be difficult to implement. Consider a situation where a product is produced in one facility, and then sent to a separate facility for coating, and then to a third company where it is installed in a larger assembly. Mechanical failure of the item due to cracking can occur at any stage of the process. If the product is not adequately inspected for cracking at each stage of the process, then defects may slip through the process and cause subsequent failure. If the product fails due to cracking at final assembly or after being placed in service, determining the origin of the manufacturing flaw may not be possible. In addition, there may not be a high level of motivation at the front end of the process to inspect for defects if those defective parts can pass through to subsequent processes undetected. If the end customer for the product specifies that it be inspected for cracking prior to the coating step, it is much more likely that defects that occur as a result of that process will be detected and identified as having come from that process. This allows for feedback into the process to prevent such defects from occurring in the first place. If inspection for cracks only happens at the end of the process, then cracks covered in coating material may easily pass undetected, and those cracks that are detected may be of indeterminable origin. Coordination at the inter-facility level is often necessary to implement sensible inspection policies that ensure consistent, high quality production at every step in the process. This not only ensures higher quality at the end of the production process, but also contributes to higher production efficiency.
Conclusion
The installation of an automated inspection system into a production environment is generally feasible without compromising existing manufacturing processes and protocols. In situations where the role of the system is expanded beyond the simple sensor, consideration needs to be given to the specific attributes of the system so that specifications and processes supporting it are appropriately designed and properly aligned. To maximize the effectiveness of inspection systems it may be necessary to accommodate the design of the product itself to enhance the ability of the system to inspect it. A properly designed implementation plan will also ensure that the maximum return on investment is achieved. In most cases the deployment of a comprehensive automated inspection system can result in a significant benefit to the user.
About the author
Scott Graber earned his master’s degree in environmental engineering from Montana State University and is currently employed as technical sales manager for Reflect Scientific – Miralogix located in Bozeman, Montana. Miralogix is a provider of integrated non destructive testing systems
More Stories
Some Ways How Motorists End Up in Collisions at U-Turns
Maximise Margins with Proven PPF Tactics
Finding the Car Boot Release Button – Tips and Tricks