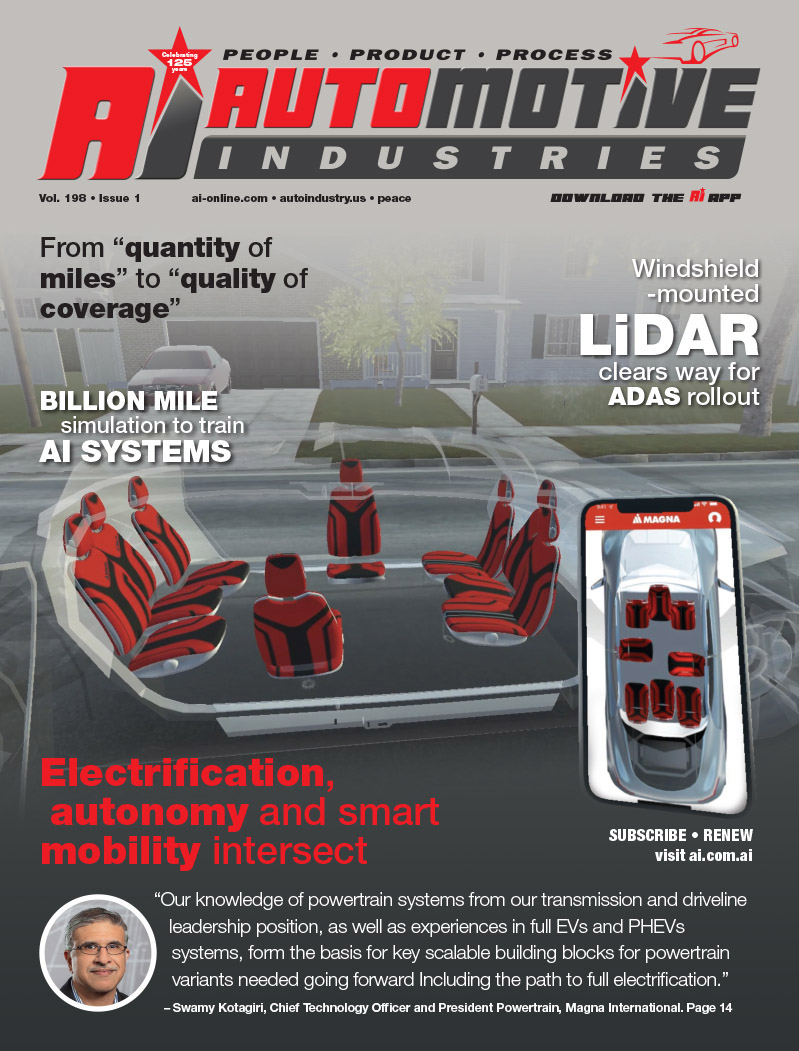
Raser Technologies develops advanced plug-in hybrid electric powertrains through its transportation and industrial business unit. The company incorporates its Symetron™ technology, to improve torque density and efficiency of electric motors and drive systems that are used in electric and hybrid-electric vehicle powertrains. The technology is also used to improve performance in industrial applications. In addition to its work in powertrains, Raser Technologies also develops clean, renewable, geothermal electric plants through its Power Systems business unit. Together these two business units form a “Well-to-Wheels” zero emissions energy strategy for transportation providing cleaner generation and use of electric power for transportation.
In April of 2008, at the 2008 SAE World Congress in Detroit, Raser Technologies introduced its Series PHEV PowerTrain also referred to as an Extended Range Electric Vehicle or E-REV power train. It was developed with system integration partner FEV Inc. in Auburn Hill, Michigan. The prototype Series PHEV demonstration vehicle is expected to be launched 1st quarter 2009. The new drive system is designed to enable larger vehicles such as sports utility vehicles (SUV’s) and light trucks to achieve over 100 miles per gallon or mpg in typical daily driving with the first 40 miles under full electric power with near zero emissions while maintaining four wheel drive operation. Initially, the vehicles will be used in utility and government fleets.
The extended-range electric vehicle architecture integrates Raser’s Symetron™ technology in an advanced 200 kilowatt (kW) peak, 100 kW continuous AC induction motor traction drive system and a 100 kW PM synchronous generating system. The 700V system architecture uses lithium-ion batteries and power management system that is expected to enable 100 miles per gallon fuel consumption in full-size fleet SUVs and service trucks. A full-size plug-in series hybrid SUV with this new powertrain is designed to drive 40 miles in all-electric mode under battery power, with near zero emissions and better acceleration than the stock vehicle. Fleet versions of this extended range electric vehicle are expected to offer up to 50 kW of exportable power from the onboard generator, a feature highly-valued by utility and other fleets.
Raser Technologies began development of Symetron technology in 2003 and has been awarded the Technology Innovation of the Year Award and Drive System Innovation of the Year Award by Frost & Sullivan. Raser was also awarded a contract for development of an integrated starter alternator for the U.S. military. The Symetron™ family of products contains several Raser innovations in motors and controllers that increase power, torque and efficiency while eliminating or minimizing the use of exotic materials, such as permanent magnets, to reduce manufacturing costs. Raser’s Symetron™ motor and drive technology enhances the performance of these powertrain components, providing increased value to the end customer.
Raser also developed a high output brushless alternator and patented intelligent voltage regulator (IVR) for the high current and heavy duty truck market and licensed this product for mass production to Wilson Auto Electric Ltd. in Winnipeg, Canada in August of 2007. “The increase in power generated by the Symetron™ alternator provides an opportunity for a significant increase in value to alternator manufacturers and automakers. The alternator provides up to 56 per cent higher output to handle increased electrical loads with minimal impact to size, weight and cost. It also provides up to a 10% efficiency improvement which means better fuel economy for the vehicle. The OEM market for high output alternators is estimated to be approaching USD 600 million annually,” says the company.
Automotive Industries spoke to Jim Spellman, Vice President of Business Development at Raser Technologies Inc.
AI: What has the reaction been to your new series PHEV drive system?
We have seen a tremendous amount of excitement over the idea that now larger SUVs can soon get over 100 miles per gallon while maintaining great performance and four wheel drive capability. There is also tremendous excitement to adapt this electric powertrain over to full and mid-size trucks which historically have been the best selling vehicles in he U.S. Utility and other fleets have also expressed great interest to purchase these vehicles to understand the impact on the total operating costs, emissions reduction, charging impact to the grid and to have high onboard emergency power generation capability.
AI: Which OEM is implementing this drive system into their vehicles?
Raser has teamed with a global OEM to build a 100 mile per gallon plug-in hybrid version of one of their popular well known SUVs using Raser’s plug-in series hybrid electric powertrain, also known as an extended range electric vehicle. The details of the project are held closely until the vehicle’s unveiling due to competitive reasons.
In addition to the SUV project, Raser is also working with a couple of large OEMs on a 140 mpg light truck demonstration vehicle powered by Raser’s ER-EV powertrain. The first two of these vehicles will be purchased by Pacific Gas & Electric for demonstration in their commercial utility fleet. Raser plans to offer 140 mpg fleet trucks that drive their first 40 miles on battery power with full performance and zero emissions.
AI: Please tell us how your Symetron™ technology has evolved over the past few years?
As the automotive industry moves from combustion to electric propulsion and from mild hybrids to full power plug-in electric vehicles with range extenders, Raser anticipated the need for high performance electric drive systems that were could be manufactured using low cost materials while minimizing or eliminating magnetic material to reduce manufacturing costs without compromising performance. This proved to be a good choice as we have seen rare earth material prices used in most permanent magnet motors increase over 400% in just less than 18 months. In the SUV project, Raser developed a 200 kW AC induction traction motor and drive to fit the application and meet the aggressive vehicle targets. In addition, Raser is demonstrating a permanent magnet synchronous generator that was custom designed to match the most efficient torque & speed of the OEMs combustion engine to produce a very efficient onboard genset to extend the vehicle range. Raser has continued to develop and apply the Symetron™ control algorithms for both traction motors and generators to provide improved performance and efficiency.
For the SUV electric powertrain, Raser is developing a liquid cooled integrated controller combining the traction and generator drive inverters and controllers into one compact power control unit (PCU) device using the latest power electronic components and cooling technology. This highly efficient PCU is sealed; EMI protected, and uses a CAN networking protocol to communicate with the vehicle hybrid master control unit.
AI: Please tell us a little about your partnership with FEV.
FEV Inc., headquartered in Aachen, Germany provides a wide range of engineering services world wide. Their U.S. team located in Auburn Hills, Michigan has been a great partner for Raser to work with because of their engineering expertise and experience. FEV has made an ideal systems integration partner implementing Raser’ hybrid electric powertrain technology in a near production ready vehicle. For thirty years, FEV has been a leader in engine and vehicle technology working with many OEMs world wide to develop systems for high volume manufacturing. As with any development project, there are always unforeseen problems. FEV and Raser have worked closely to provide practical solutions to these problems as they arise. We look forward to completing this project with FEV and working with them in the future.
AI: What are some of the new automotive technologies Raser is working on?
Raser is also working on a variety of smaller electric powertrains and components to apply these same concepts to smaller vehicles. We have expanded our engineering team and continue to challenge them with providing immediate solutions while developing intellectual property for new designs. These diverse international teams of PhDs are currently working on concepts to achieve or exceed current IPM machines using reduced amounts of permanent magnet materials. To extend the range and reliability of our products, we are also working on improved cooling designs for both the motor and drives. We hope to apply these concepts to our next electric powertrain project.
More Stories
Automotive Industries (AI) Newsletter October 2024
How Modern Equipment is Reshaping Automotive Production Standards
Automechanika Shanghai 2024