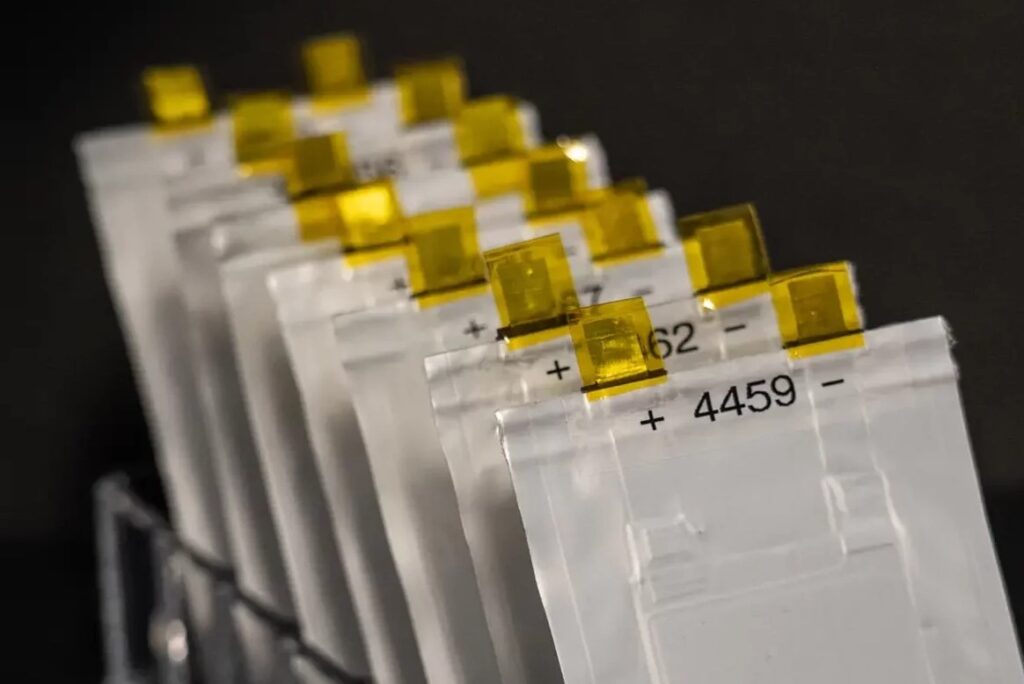
Blue Current is driving a revolution in the battery industry with its safe, energy dense, solid-state battery.
Lithium-ion battery technology has reached the point of diminishing returns in terms of energy density and performance. Historically, energy density has trebled since Sony commercialized the technology in 1991, while costs have dropped by over 97%, but the innovation curve has flattened.
Energy density is the deciding factor for raising the performance of the next generation of mobile devices and Electric Vehicles (EVs). Breakthroughs in silicon technology will, it is believed, enable the next advance in energy storage.
Silicon (Si) is the second most abundant element after oxygen. Its storage properties enable the design of the thin electrodes required for high energy density.
Automotive Industries (AI) spoke to Susan Stone, the recently appointed CEO of Blue Current, and co-founder and Chief Technical Officer Kevin Wujcik, to find out more about Si technology. Blue Current is driving a revolution in the battery industry with a safe, energy-dense solid-state battery which, the company says, provides a high-performing alternative to lithium metal and other battery types.
AI: How close is Blue Current to bringing solid-state Si batteries to market?
Stone: Blue Current is moving from the R&D phase into commercialization of a full stack cell which includes a ground-breaking silicon anode. And as far as our business model goes, our intention is to partner with customers and existing manufacturers to bring the full stack cell design to the market.
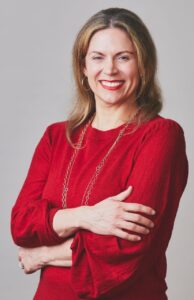
As part of our commercialization phase, we are building a pilot manufacturing line to produce cells at our 22,000-square-foot headquarters in Hayward, California. The pilot will be used to prove our batteries can be scaled economically using high-volume Lithium-ion battery (LIB) manufacturing equipment.
AI: What resources do you have for the rollout?
Wujcik: Hayward is in the middle of the Bay area, so we have access to some fast-paced machine shops in the area. The 22,000-square-foot facility includes a 3,000-square-foot dry room, which will house the pilot manufacturing line.
We have close to 1,000 channels for cycling and testing batteries, as well as a wide range of characterization tools, including scanning electron microscopes to analyze the electrolytes that we manufacture.
AI: Why the focus on solid state batteries?
Wujcik: Solid state batteries can enable safety that is far superior to liquid electrolyte-based batteries and can enable high energy densities that surpass state-of-the-art lithium-ion cell capabilities. Historically, solid state batteries have been primarily built with lithium metal anodes. The first big difference about the Blue Current approach is that we use silicon materials in the anode instead of lithium metal.
Silicon is an amazing material that can store around 10 times more lithium per gram compared to graphite. The challenge with silicon is that the material expands and contracts while the battery is cycled. This causes the material to continuously react with liquid electrolytes. We have discovered that if you use silicon in a fully dry, solid electrolyte environment, instead of liquid electrolyte, it can cycle very stably for 1,000 plus cycles with over 80% capacity retention.
Where we have spent a lot of our time as a company is developing composite electrolytes and composite anodes that have the elasticity and flexibility that silicon needs to cycle.
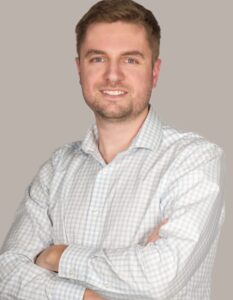
One breakthrough was developing a way for silicon to expand and contract while maintaining good contact with the solid electrolyte through advanced polymers. You cannot prevent silicon from expanding and contracting in either liquid or solid form due to its thermodynamic properties.
The polymers we have developed have elasticity that allows silicon to expand and contract while maintaining good contact with the solid electrolyte. That’s what we refer to as the silicon elastic composite.
AI: What are the main benefits of the silicon elastic composite battery solution?
Wujcik: The first benefit is our ability to lower the required operating pressure for cells. It’s not uncommon for solid state batteries to need operating pressures of 10 to 50 megapascals. We cycle at between one to three megapascals of pressure, which is very low for the industry and is in line with OEM targets.
Another advantage relates to the challenge of eliminating dendrite formation that is common in lithium metal batteries, and difficult to prevent when manufacturing at high volumes. Silicon does not suffer from dendrite formation the way that lithium metal does.
You still need to anticipate and prevent lithium plating, but you don’t have the same dendrite formation risk that comes with plating lithium every single cycle as you would with a lithium metal anode. This adds up to longer life and durability.
And then there is a safety advantage as you do not have any liquid electrolyte present. Extensive crush overcharge, nail penetration, and thermal abuse testing by an external third party has demonstrated that there are significant advantages for multi-layer solid state cells.
AI: What has prevented the commercialization of solid-state batteries up to now?
Wujcik: We believe it starts with having the right materials. You must have materials that can be scaled. You cannot use electrolyte materials that are comprised of exotic chemicals or rare earth elements. We are using earth abundant materials in our electrolytes.
Secondly, it comes down to how you manufacture a cell. There are techniques where, for instance, in the lithium metal world manufacturers will vapor deposit one to five microns of lithium on a copper foil, to make the first charge easier for an anode free cell. We don’t see that as being a scalable technique.
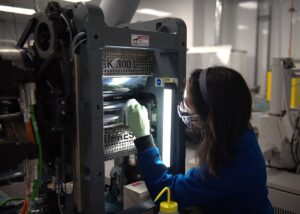
Then there are techniques to prevent dendrite formation in a lithium metal cell using quality control and characterization tools taken from the semiconductor industry to make sure that the separator is completely defect-free in the millions of square meters of material you are going to manufacture. We don’t believe that that is totally scalable, either.
Our approach is to start with the right materials that are simple in design, which means that we do not have those kinds of challenges which have to be solved at scale. We want to start with a simple material set that we feel is designed for manufacturing.
Stone: This is such an important point and was one of the key deciding factors for me when I was thinking about joining Blue Current. It may be simple, but it is not easy to find a very elegant solution to something that we’ve all been trying to solve, which is how we get to the next generation battery that unlocks so much potential for the whole world.
What Kevin and the founding team have achieved is to make sure the Blue Current cells can be made using the same equipment that is currently in service to make lithium-ion batteries. This de-risks the scaling of manufacturing and helps our customers and partners see how they are going to manufacture the new generation of batteries without massive capital investment.
AI: Does Blue Current manufacture its own active materials?
Wujcik: No, we have taken a strategic approach to not be an active material manufacturer to ensure scalability. We work with materials that are commercially available so that they can be scaled quickly.
AI: Does Blue Current release performance data?
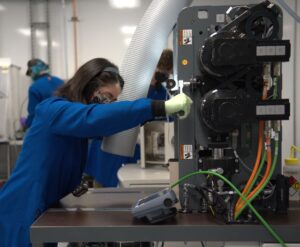
Wujcik: Yes, we regularly present this information at conferences. If interested parties want to reach out and set up a call to learn more about the technology, we would be happy to schedule that.
AI: What intellectual property does Blue Current have around solid-state batteries?
Wujcik: We have a lot of IP around the composition of the electrolyte and electrode compositions, in particular the composition of composites involving inorganic electrolyte combined with advanced polymers. We have intellectual property around electrode-composition, especially for the anode.
We also have important IP around lowering the required operating pressure for solid state cells.
AI: Why do you believe you are ready for pilot phase production?
Wujcik: The validating performance that we have achieved with our hand-built stack cells warrants moving to the next step, which is manufacturing at scale. It is never easy to scale anything and there may be unexpected challenges along the way. But, we have reached the development point where we are ready for the next phase.
AI: What is next for Blue Current?
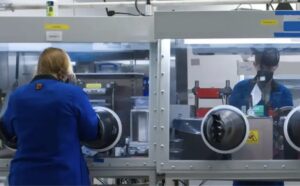
Stone: The priority is commissioning that pilot line and being able to ship samples off that pilot line to our partners and customers.
That is a big unlock for the next step for this company, and I think a big unlock potentially for solid state silicon batteries. We are quietly working with a couple of partners, and we are hopefully going to be expanding those relationships.
They are pretty important relationships to us, so we will work on growing and deepening them, and potentially bringing another automaker into the fold.
There are adjacent lower volume or smaller form factor markets which we could be serving without distracting us from the auto sector. So that is another place where we are working on a few opportunities.
A goal for 2025 is to just diversify our market and the types of partners that we’re working with.
More Stories
Wales’ “biggest ever business event” to take place in December
Global autos industry under strain amid China export restrictions – BMI
What to Do If Your Truck Accident Claim Is Denied