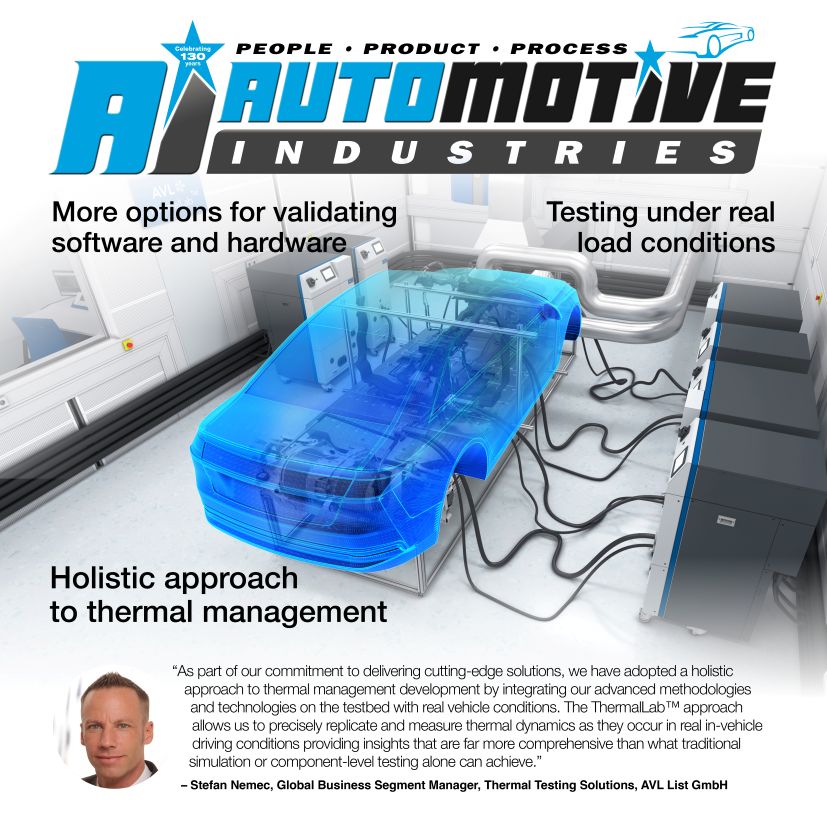
Testing of vehicle thermal management (VTMS) systems has become more complex with the advent of electric vehicles.
Complexity is introduced through the variation of the temperature range of electric propulsion system components under different operating and environmental conditions. Optimizing VTMS is essential as it has a significant impact on the energy efficiency of the entire vehicle and the durability of all components in the propulsion system, such as the battery and inverter.
Highly efficient systems require extensive calibration and testing time at the vehicle level, which has a huge impact on development cost and time.
AVL ThermalLab™ has developed a range of model-based tests to simulate all coolant circuits under dynamic conditions to help optimize the entire VTMS system in a vehicle.
Automotive Industries (AI) asked Stefan Nemec, Global Business Segment Manager at AVL List GmbH, to describe the company’s unique approach to testing VTMS systems.
Nemec: AVL recognizes that effective thermal management is essential not only for enhancing vehicle efficiency and performance, but also for ensuring durability and meeting increasingly stringent sustainability standards.
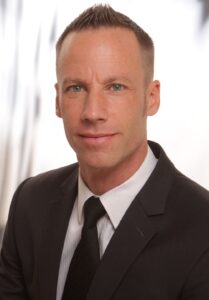
As part of our commitment to delivering cutting-edge solutions, we have adopted a holistic approach to thermal management development by integrating our advanced methodologies and technologies on the testbed with real vehicle conditions. By continuously expanding our methodologies and integrating emerging technologies, AVL is well-positioned to support the industry’s shift toward sustainable mobility with robust, future-oriented solutions.
AI: How does the AVL ThermalLab optimize the development process for complex cooling circuits?
Nemec: The AVL ThermalLab™ approach allows us to precisely replicate and measure thermal dynamics as they occur in real in-vehicle driving environment, providing insights that are far more comprehensive than what traditional simulation or component-level testing alone can achieve.
By testing under real vehicle conditions, we gain an accurate picture of how different components interact thermally across a range of operating conditions. This enables us to optimize not just individual elements but the entire thermal system, ultimately improving energy efficiency.
Our goal is to empower our clients across a wide range of thermal management applications by delivering customized testing environments that align with the highest industry standards. This modular approach allows us to offer tailored solutions that not only meet the precise needs of our customers but also ensure a mature and reliable product experience. By working closely with our clients, we aim to support innovation and efficiency in every aspect of thermal management testing.
AI: How does the AVL ThermalLab simulate real-world driving conditions?
Nemec: Our dedication to our customers is to deliver early-stage validation of hardware components and initiate sensor calibration for cooling and heating, ventilation and air conditioning (HVAC) systems during the concept phase of vehicle development. By integrating these processes early, we help mitigate the risks of late-stage changes, enabling engineers to focus on optimizing energy efficiency in complex thermal management systems.
This approach includes both hardware and software advancements to tackle the complexities of modern thermal systems, especially in the context of electric and hybrid vehicles, where thermal management plays a critical role in extending battery life and optimizing energy consumption.
AI: What are the key challenges in managing temperature variations across EV propulsion components?
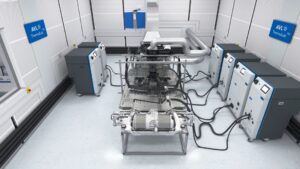
Nemec: EV propulsion systems produce around five times the power-to-weight ratio compared to internal combustion engines (ICEs), with notably high peak loads. To maintain optimal performance, these systems require a more complex thermal management strategy, with multiple temperature levels to ensure each component remains within its ideal comfort zone.
This complexity leads to sophisticated cooling circuit architectures, incorporating an extensive network of piping, valves, and control instrumentation, as well as software-intensive calibration for different operating modes.
Our research indicates that conventional steady-state testing is insufficient for capturing the full range of critical scenarios encountered in standard driving cycles, real-world conditions, extreme situations, and transitions between operating modes.
To mitigate risks such as overheating and power degradation, a more dynamic approach is essential. We are committed to developing testing methodologies that simulate these varied conditions, ensuring that EV thermal management systems perform reliably across all operational demands.
AI: Can you discuss how AVL’s conditioning systems enhance the accuracy of VTMS testing for electric and hybrid vehicles?
Nemec: Our advanced coolant and oil conditioning system, AVL ConsysCool Dynamic, provides vehicle and system engineers with the ability to precisely emulate the thermal behavior of components within vehicle cooling systems. This is especially crucial for EV powertrain cooling, which demands greater dynamic response. The Conditioning Emulator offers a remarkable temperature change rate of 6K per second with an accuracy of ±0.5K, meeting the high precision needs of modern powertrain development.
Our patented Interface Module integrates directly with the vehicle’s cooling system – the Unit Under Test (UUT) – enabling temperature control that is fully independent of the UUT’s flow rate, which ranges from 0 to 90 liters per minute, with an adjustable pressure drop. This flexibility and precision make ConsysCool Dynamics a powerful tool in developing and validating advanced thermal management solutions, empowering engineers to optimize performance and reliability under diverse operating conditions.
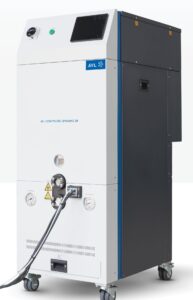
AI: What role does Hardware-in-the-Loop (HIL) technology play in the AVL ThermalLab’s testing capabilities, and why is this technology important?
Nemec: OEMs and system suppliers are transforming traditional development processes to tackle challenges like increased system complexity and accelerated timelines – all while aiming to achieve higher energy efficiency in powertrain thermal management.
HIL testing empowers our customers by providing a broader range of options for developing and validating both hardware and software control functions, particularly during the concept phase of vehicle programs.
Through HIL, physical hardware or environmental factors within cooling circuit components can be replaced with our emulators, enabling the thermal behavior of these components to be accurately represented using either real-world measured data or advanced simulation models.
This modernized development approach requires engineers to integrate simulation, physical testing, and software calibration, offering a more in-depth understanding and yielding solutions that significantly advance energy efficiency.
AI: How does AVL’s modular design approach benefit clients with diverse testing needs for different propulsion architectures?
Nemec: Traditionally AVL, like many specialized engineering test service and equipment providers, has offered highly customized solutions tailored to individual client needs. However, with advancements in thermal management, we recognized an opportunity to adopt a new approach.
From the outset of the ThermalLab concept, we chose to pursue a modular product design, creating a flexible and adaptable toolset for our customers. This modularity enables us to deliver reliable, high-performance test systems with reduced lead times and costs, empowering our clients with streamlined, effective solutions for their thermal management challenges.
AI: How do AVL’s climatic chambers simulate extreme conditions, and what advantages do they offer over traditional test environments?
Nemec: AVL offers specialized climatic chambers designed to integrate seamlessly with a variety of test systems, with a primary focus on battery testing solutions that are standardized for specific applications.
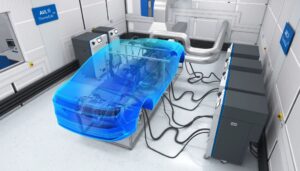
Leveraging this expertise, our climatic chambers for ThermalLabs are precisely engineered to meet the unique demands of thermal management development. They are optimized for airflow applications, facilitate quick exchange of test rigs, and support the testing of real EV batteries, among other advanced requirements. This capability underscores AVL’s commitment to delivering adaptable, high-quality solutions that address the evolving needs of thermal management and powertrain innovation.
AI: How do you see AVL ThermalLab contributing to the efficiency and reliability of future EV thermal systems?
Nemec: Our benchmark studies reveal that many EVs on the market allocate a significant portion of their stored battery energy – around 30% – to thermal management needs, including cabin conditioning, fast charging, and maintaining optimal temperature zones for powertrain components.
AVL’s ThermalLab enables our customers to develop robust VTMS hardware and functionality early in the process, ahead of complete vehicle testing in climatic wind tunnels or on the road. This engineering frontloading approach reduces the risk of costly hardware changes later in development, allowing engineers to concentrate on software calibration. The result is more energy-efficient, reliable thermal management systems that enhance overall EV performance.
More Stories
Industry-standard switching & simulation systems from Pickering Interfaces on show at Space-Comm Expo
Bangkok International Motor Show 2025 – The Talk of Sensuous Automotive
SEPA and Bidgely Release Report on the Power of AI for Transportation Electrification