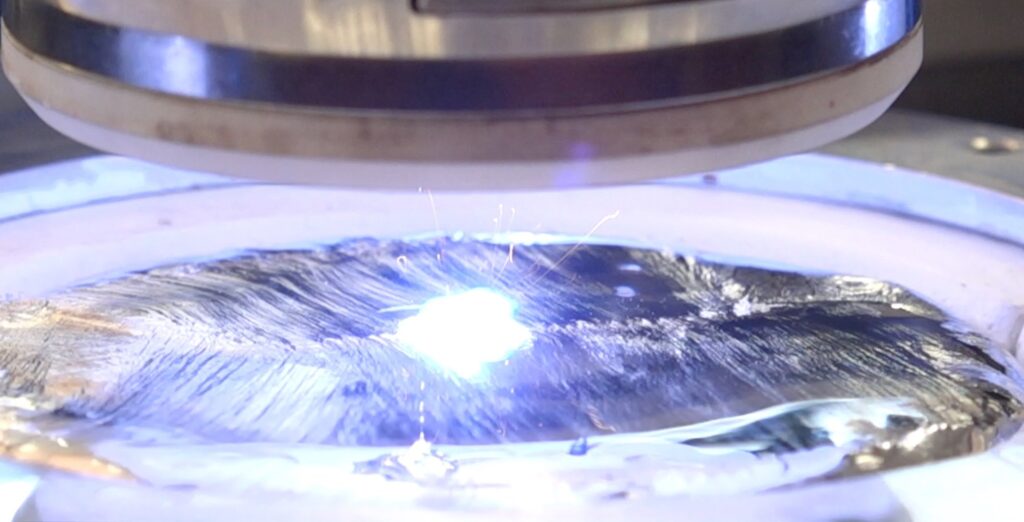
In a recent conversation with Automotive Industries, Karl Ágúst Matthíasson, CEO of DTE, shared insights on the shifting landscape of the aluminum industry and the significant challenges facing automakers reliant on this versatile metal. As demand for lightweight materials rises, aluminum has become a cornerstone for automotive production, particularly in electric vehicles (EVs), due to its strength-to-weight ratio and recyclability. However, as Karl explains, disruptions in supply chains, compounded by high energy costs and geopolitical instability, are making it increasingly difficult for manufacturers to secure consistent aluminum supplies, placing new pressures on automotive production and prompting innovative solutions from companies like DTE.
A recent example of these challenges is seen in Porsche’s struggle to source aluminum following a flood that temporarily halted one of its European suppliers. This situation is emblematic of a broader issue, as automakers across the globe confront supply vulnerabilities. With aluminum being essential to many automotive components, from body panels to critical battery housings, any interruption in its supply can have wide-ranging impacts on production continuity, costs, and even vehicle design. Karl points out that while some manufacturers may turn to alternate sources or materials, this approach has limitations, as not all aluminum is created equal. Aluminum used in automotive applications demands specific compositions, tailored to each component’s unique requirements. Producing such high-quality aluminum is an energy-intensive process that requires meticulous control over the metal’s chemical composition—a factor that DTE is addressing through cutting-edge technology.
At the forefront of aluminum composition analysis, DTE leverages its Liquid Phase Laser-Induced Breakdown Spectroscopy (LP-LIBS™) technology to provide real-time insights into the composition of molten aluminum. Traditionally, composition analysis is a labor-intensive, time-consuming process that relies on solidifying samples for lab testing. DTE’s LP-LIBS™ technology, however, allows for instantaneous composition readings, enhancing efficiency, reducing energy consumption, and ensuring precision. This innovation not only aids primary aluminum producers but also secondary processors working with scrap aluminum, helping them achieve the purity levels required by automakers.
According to Karl, the advantages of real-time analysis extend beyond time savings; they also offer a substantial reduction in energy costs—an increasingly vital consideration as energy prices remain high, especially in Europe. By minimizing the time aluminum spends in a molten state, DTE’s technology allows manufacturers to cut down on the vast amounts of energy traditionally required to maintain molten aluminum at over 700°C. This efficiency is critical as the aluminum industry strives to lower its carbon footprint in response to environmental regulations and consumer demand for sustainable manufacturing practices.
Karl also highlights the growing emphasis on recycled aluminum, which uses approximately 95% less energy than producing primary aluminum from raw materials. With environmental, social, and governance (ESG) goals taking center stage, the automotive sector is turning more aggressively to secondary aluminum to meet both regulatory requirements and consumer expectations for sustainable vehicles. However, as demand for recycled aluminum increases, competition for scrap aluminum is intensifying, especially among buyers in Europe, North America, and Asia.
DTE’s LP-LIBS™ technology, paired with its AI-driven IRIS process intelligence platform, is helping to streamline the use of recycled aluminum in automotive production. By providing real-time data and predictive insights, DTE’s platform allows manufacturers to optimize batch compositions, identify potential impurities quickly, and reduce the likelihood of costly remelts. This shift toward real-time analysis and predictive insights signals a transformative step forward in the aluminum industry, one that Karl believes will be instrumental in helping automakers navigate the ongoing challenges in aluminum supply and production.
Looking ahead, Karl envisions a future where automakers increasingly integrate innovative solutions like DTE’s to bolster supply chain resilience and drive sustainability. With global aluminum demand expected to rise by over 40% by 2030, DTE’s technology offers a strategic advantage, enabling automotive manufacturers to manage energy consumption, enhance product quality, and secure a stable aluminum supply in an era marked by unpredictability and mounting environmental responsibility.
Automotive Industries interview with Karl Ágúst Matthíasson, CEO, DTE
Automotive Industries: Hi Karl, can you share your thoughts on the recent challenges Porsche has faced in sourcing adequate quantities of aluminium and how this might impact the broader automotive industry?
Matthíasson: In July, one of Porsche’s aluminium suppliers was flooded after heavy rains hit parts of Europe. As a result, Porsche was unable to source the aluminium it needed to maintain its production levels, leading to a temporary reduction in output.
Like many automakers, Porsche relies heavily on aluminium for many of its body components and requires metal with extremely precise composition to give it just the right qualities. Producing aluminium of this quality is time consuming and requires skilled manufacturing.
Given that aluminium is widely used across the automotive industry, this example highlights the broader vulnerability of automakers to supply chain disruption. Whether it’s caused by natural disasters, geopolitical factors like war disrupting shipping routes, or even rising energy costs affecting European aluminium production, the industry is increasingly exposed to risks in its aluminium supply.
Automotive Industries: In an increasingly unstable world with heightened demand for aluminium, how do you see the automotive industry addressing potential scarcity or rising costs of this critical metal?
Matthíasson: There are several strategies automakers might adopt. One option could be to source the aluminium from alternative suppliers, even if this means looking further afield. Another approach could involve reducing the amount of aluminium used in favour of other suitable materials, or by improving processes to become more energy efficient and make better use of recycled aluminium.
Improvements in the efficiency of aluminium production can reduce energy usage and therefore lower costs. Additionally, technological advancements are enabling more effective use of secondary aluminium, even when the scrap is contaminated with other materials. DTE’s technology, for example, helps aluminium producers optimise quality control and energy efficiency, delivering benefits to automakers and secondary processors too.
Automotive Industries: How does DTE’s technology contribute to securing a stable supply of aluminium for automotive manufacturers, particularly in terms of ensuring the right composition? / How important is real-time chemical composition analysis in maintaining a consistent supply of high-quality aluminium for automotive production?
Matthíasson: DTE’s technology enables aluminium processors to cut their energy usage and costs during the melt process, both at the automaker level and further up the supply chain. With real-time composition readings, we eliminate the need to solidify a sample from each batch for lab analysis, significantly reducing the time that aluminium needs to be kept molten at over 660℃. This allows producers to address impurities proactively rather than reactively. With significant rises in energy costs in recent years, particularly in Europe due to the conflicts in Ukraine and the Middle East, this kind of efficiency can result in substantial savings for manufacturers.
DTE also offers advantages for secondary processors of aluminium. Impurities within scrap metal, often introduced for previous applications, can make it difficult to achieve the precise qualities needed by automakers. Real-time analysis allows secondary processors to quickly identify impurities and blend different sources to achieve a final product that meets the necessary specifications.
By improving recyclability, even in applications requiring precise qualities, DTE’s technology helps increase the overall availability of aluminium and reduces reliance on virgin metal. Recycled aluminium offers around a 95% saving in energy usage over virgin aluminium, with a similar saving in greenhouse gas emissions.
Automotive Industries: What specific advantages does DTE’s LP-LIBS™ platform offer to the automotive industry when it comes to aluminium composition and supply?
Matthíasson: DTE’s Liquid Phase Laser-Induced Breakdown Spectroscopy (LP-LIBS)™ technology makes use of high-energy lasers to provide real-time analysis of the composition of molten aluminium.
Traditionally, analysing aluminium composition requires a sample to be drawn, solidified and taken to a lab for analysis, which is time-consuming and forces manufacturers to be reactive. This process also provides a limited number of samples, giving an incomplete picture of what is happening in the melt.
LP-LIBS™ can provide composition analysis almost instantly by sampling directly from the melt, reducing the time needed to keep the metal molten. It also provides a much larger number of samples, providing a more comprehensive picture of the melt’s composition. When coupled with DTE’s AI software, it offers a detailed analysis of the whole process.
Another advantage of LP-LIBS™ is that it reduces human error. Operator mistakes, such as mislabelling or misinterpreting samples, are a common source of issues in aluminium manufacturing. By automating much of the process, we not only eliminate these errors but also remove a major safety risk – the need for workers to handle molten metal.
By making the whole process easier, DTE’s technology can optimise production standards across the industry, potentially enabling a far larger range of producers capable of making the exact compositions automakers need in their vehicles.
Automotive Industries: Can you elaborate on how DTE’s AI-based cloud platform enhances the value chain for automotive manufacturers by providing actionable insights?
Matthíasson: DTE offers not only the LP-LIBS™ analysis, but also provides valuable insights when the results are combined with its powerful AI software.
The IRIS process intelligence platform delivers a real-time overview of plant operations via an intuitive GUI and enables operators to make quick adjustments in order to keep batches within the required composition specifications.
In addition, IRIS can alert operators to anomalies and, with its machine learning capabilities, offer predictive insights and recommendations to optimise processes and assist in quality control. By combining real-time analysis with AI, IRIS goes beyond merely speeding up existing tasks, delivering unprecedented quality and process control that save time, money and energy.
Automotive Industries: Given Porsche’s aluminium shortage, what strategies or solutions would you recommend for automakers to mitigate such supply chain disruptions in the future?
Matthíasson: Automakers should factor in supply chain disruptions into their production considerations. In a more geopolitically strained world, resilience will be key to manufacturers maintaining stability. It’s wise to seriously consider alternative sources ahead of time in case the main supplier has to stop or reduce production.
Automakers who handle their own casting, or upstream producers who cater to the automotive industry should consider how new capabilities such as real-time composition analysis could improve their quality control, improve utilisation of secondary aluminium and reduce their cost, energy consumption and waste. This would allow them to make better use of what remains available during a supply chain disruption and to offset the greater costs which always occur when there is a shortage.
Automotive Industries: What role does sustainability play in DTE’s approach to transforming the metals industry, especially concerning the automotive sector’s aluminium needs?
Matthíasson: Sustainability is central to our mission. According to the International Aluminium Institute, the aluminium industry produced over 1.1 billion tonnes of CO2 in 2022 and by helping manufacturers and users reduce their energy consumption we’re also helping lower the carbon footprint of the aluminium industry and sectors like automotive that rely heavily on aluminium.
For example, I previously mentioned the enormous 95% saving in energy and emissions that recycled aluminium offers over virgin metal. Our technology, which makes aluminium recycling easier, plays a part in reducing the carbon footprint across the entire industry and its downstream sectors.
Automotive Industries: As an experienced engineer and businessman, what are your predictions for the future of aluminium supply in the automotive industry, and how can DTE’s innovations help address these challenges?
Matthíasson: We can expect supply challenges in the short to medium term, especially in Europe due to geopolitical issues. Last year saw a decline in European production, in part due to increasing energy prices.
Continued disruption in areas like the Red Sea may make it harder for the automotive industry to source aluminium from alternatives such as China and automakers should be prepared for disruptions including longer shipping times and higher freight costs. Scrap aluminium will also be in tighter supply as users try to offset shortages and users in Europe and North America will have more competition from Asian users.
On the other hand this disruption offers opportunities for new technologies such as real-time composition analysis techniques to come into their own, to make maximum use of scrap aluminium as well as to meet increasing demand for low-carbon aluminium in response to net-zero and carbon emissions targets.
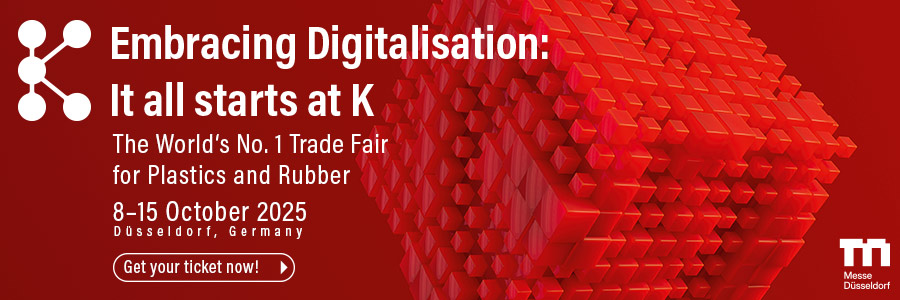
More Stories
Arkema: from cell phone to EV batteries in 40 years
BRANO and DOMO join forces to replace aluminum with TECHNYL® polyamide
trinamiX – will cars function like Smartwatches in the future?