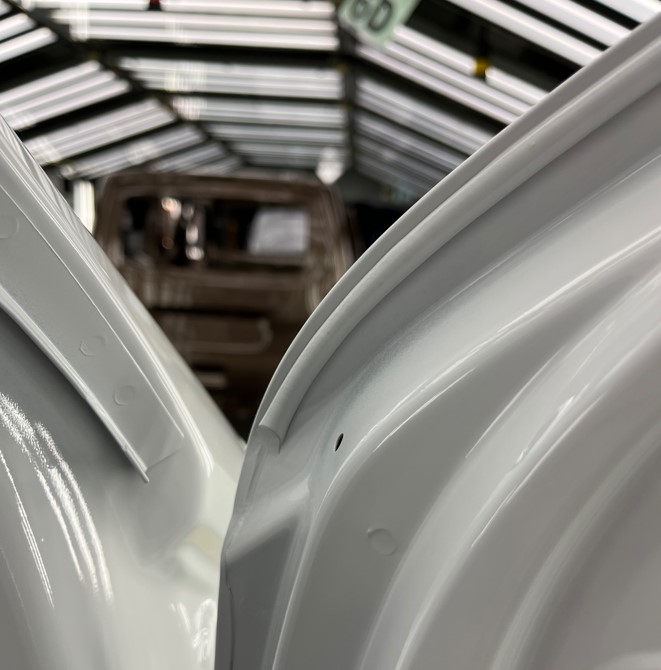
PPG CORASEAL® 4-Wet Sealer represents an innovative solution tailored for automotive original equipment manufacturers (OEMs) striving to meet their sustainability goals.
Stellantis has reported energy savings and emission reduction on its light commercial vehicle production lines after switching to the PPG CORASEAL® 4-Wet Sealer which requires just one curing stage.
Conventional OEM paint shops use a curing process comprising a sealer oven, primer oven, and topcoat oven. The PPG B1:B2™ process, also known as the 3-Wet system, reduced that to just the sealer oven and topcoat oven. With the latest PPG Coraseal 4-Wet Sealer, only the topcoat oven is required.
The system is compatible with most waterborne and solvent borne systems, according to PPG. It is estimated that, compared to the 3-Wet system, the new sealer can reduce energy consumption by nearly 8%, cut CO₂ emissions by nearly 5% based on EU average conversion factors.
Productivity is enhanced by speeding up the curing cycle, and the need for fewer ovens simplifies maintenance processes and reduces costs. Automotive Industries (AI) found out more from Dominique Busseuil, PPG Business Manager Development, Automotive Coatings and Thierry Destruhaut, PPG Customer Sustainability Business Partner, Automotive Coatings.
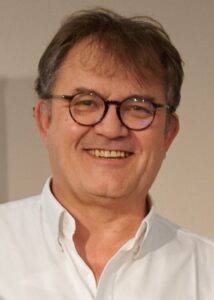
AI: How does the PPG Coraseal 4-Wet Sealer technology differ from traditional sealer processes, and what advantages does it bring to automotive OEMs?
Busseuil: PPG CORASEAL® 4-Wet Sealer represents an innovative solution tailored for automotive original equipment manufacturers (OEMs) striving to meet their sustainability goals.
The solution cures in just one step, versus up to three steps required for traditional technologies, providing sustainability benefits for automotive OEM paint shops by reducing energy usage and CO₂ emissions.
By integrating these advanced sealers into their manufacturing processes, OEMs can achieve significant energy savings, contributing to a reduced carbon footprint. Additionally, the versatility of the 4-Wet sealer allows for fine-tuning of production line speed, enhancing operational efficiency without compromising on product quality.
Q: What specific sustainability benefits have been observed at Stellantis’ LCV plants since implementing the PPG Coraseal 4-Wet Sealer?
Destruhaut: The introduction of PPG CORASEAL® 4-Wet Sealer has enabled Stellantis to significantly lower its Scope 1 greenhouse gas emissions at its production facilities. This sealer does not require a specialized oven for curing, allowing Stellantis to greatly reduce natural gas consumption by decommissioning its dedicated sealant ovens.
Q: How does the reduction in curing steps from three to just one with PPG Coraseal impact energy consumption and CO₂ emissions in automotive paint shops?
Destruhaut: Thanks to PPG CORASEAL® 4-Wet Sealer technology, Stellantis has been able to optimize its paint shop operations and achieve significant environmental benefits.
Previously, the curing process for materials, sealants, base coats, and clear coats required two separate ovens. However, with the implementation of Coraseal 4-Wet, all these components can now be cured in the topcoat oven during the final stage of the paint shop.
This consolidation of curing steps from two to one has resulted in several advantages. Firstly, it has led to a reduction in the quantity of natural gas required for heat production.
Specifically, the removal of the sealant oven has resulted in a decrease of approximately 40 kWh per vehicle produced. This reduction in natural gas consumption translates to a decrease of around 8kg of CO2e emissions per vehicle produced.
To put this into perspective, we can estimate the impact of PPG Coraseal 4-Wet on Stellantis’ plants in Hordain and Mangualde. Considering the annual production volume of these plants, the introduction of this technology has contributed to a reduction of approximately 1,520 metric tons of CO2e in their combined greenhouse gas emissions.
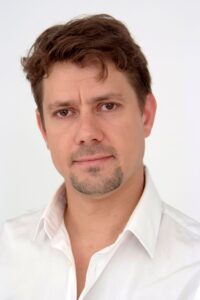
Q: What challenges did you face when introducing this new sealer technology, and how were they overcome?
Destruhaut: The challenge arises from the need to apply multiple layers, from sealer to final paint, using a wet-on-wet process, which requires only a single curing step. The sealer must be compatible with all subsequent paint layers to ensure optimal adhesion and performance.
Q: How does the PPG Coraseal 4-Wet Sealer contribute to improving productivity and reducing maintenance costs for OEMs?
Busseuil: By leveraging these technologies, OEMs can enhance the efficiency of their production lines. One key benefit is the optimization of production line speed, which allows for faster and more streamlined manufacturing processes. This can lead to increased productivity and output.
Additionally, these technologies can contribute to a decrease in temperature curing.
By implementing advanced curing methods, OEMs can reduce the amount of time and energy required for curing processes. This not only saves on energy costs but also minimizes the environmental impact associated with high temperature curing methods.
Furthermore, the adoption of these technologies can result in savings on maintenance costs. For instance, by eliminating the need for ovens in the curing process, OEMs can reduce the frequency of maintenance and repairs associated with oven equipment. This can lead to significant cost savings over time.
Q: How do you see the role of innovative coatings like PPG Coraseal in achieving broader sustainability goals within the automotive industry?
Destruhaut: PPG has a strong commitment to developing energy-efficient innovations for the OEM industry, and one notable example of this is the PPG CORASEAL® 4-Wet Sealer.
As part of our sustainability strategy, we collaborate closely with our OEM customers to implement solutions tha
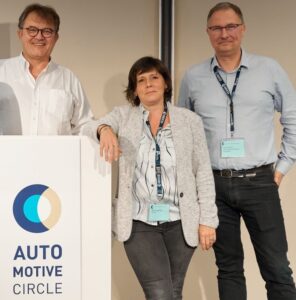
t reduce carbon emissions in the paint, electrocoat, and sealant application processes.
One effective approach to reducing carbon emissions is by minimizing the heat required for curing materials.
This can be achieved through various means, such as optimizing processes to require fewer ovens or lowering the curing temperature. By doing so, we can significantly reduce the natural gas consumption at OEM plants, resulting in a tangible reduction in greenhouse gas emissions.
However, PPG recognizes that reducing carbon emissions is not limited to heat reduction alone. We also focus on developing novel E-coat solutions that decrease both electricity and natural gas demand at OEM plants.
Every kilowatt-hour (kWh) of electricity or natural gas that PPG and our OEM partners can save through these innovations translates into a real reduction in greenhouse gas emissions at the OEM plants.
While switching to carbon-neutral energy sources is a viable option for reducing greenhouse gas emissions in electricity consumption, it remains a challenge for the industry to find carbon-neutral alternatives for natural gas as a heat source. This is why it is crucial for the industry to prioritize innovation in energy-efficient paint shop processes, as it offers a practical and effective way to enhance sustainability within the OEM sector.
Q: What feedback have you received from Stellantis and other OEMs regarding the performance and environmental impact of the PPG Coraseal 4-Wet Sealer?
Busseuil: Stellantis has provided positive feedback regarding the performance and environmental impact of the PPG CORASEAL® 4-Wet Sealer.
They consider it to be a standard solution that aligns with their sustainability targets. By implementing this technology, Stellantis can enhance its sustainability efforts and contribute to reducing their environmental footprint.
In addition to Stellantis, other OEMs are showing interest in and exploring the use of the PPG CORASEAL® 4-Wet Sealer.
These OEMs recognize the potential benefits of this innovative technology in terms of performance improvements and environmental impact reduction. By adopting this solution, OEMs can optimize their production processes, reduce energy consumption, and minimize greenhouse gas emissions.
AI: What are the next steps for PPG in terms of further enhancing sealer technologies for automotive OEMs?
Busseuil: Moving forward, PPG aims to address the evolving challenges faced by automotive OEMs by focusing on further enhancing sealer technologies. One key area of development is the reduction of curing temperatures, aiming to achieve temperatures between 80-100°C.
By introducing new material technologies, PPG aims to optimize the curing process and improve overall efficiency in automotive manufacturing.
Lowering the curing temperature offers several benefits. It can lead to energy savings by reducing the amount of heat required for the curing process. Additionally, it can contribute to a more sustainable manufacturing process by minimizing greenhouse gas emissions associated with high temperature curing methods.
More Stories
DuPont materials science advances next generation of EV batteries at The Battery Show
How a Truck Driver Can Avoid Mistakes That Lead to Truck Accidents
Car Crash Types Explained: From Rear-End to Head-On Collisions