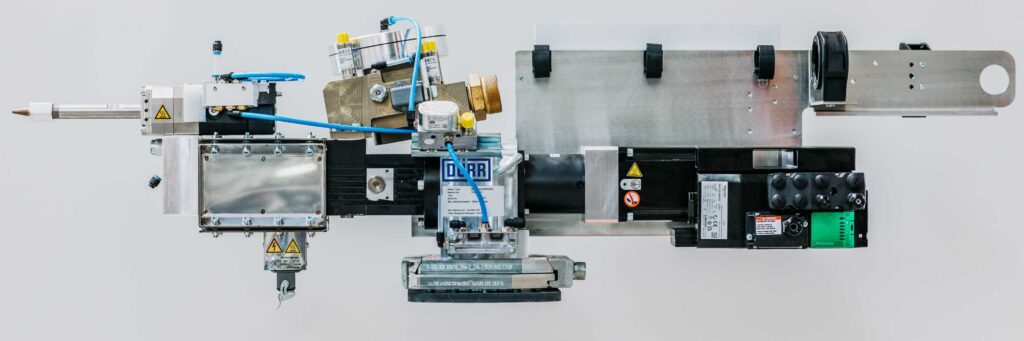
The Dürr EcoMeter SP is a continuous dosing system designed for the seamless application of highly viscous media without interrupting material flow.
Volume production of batteries for electric vehicles and the monitoring of their performance on the road over time have given engineers and designers greater understanding of the technology required to increase range and improve safety.
At the heart of the battery are bonding and filling materials used in its assembly, therefore technology is required to apply the adhesives, sealants and fillers used in battery production. A modular solution developed by Dürr gives vehicle-manufacturers high quality, flexibility and adaptability for various viscosities and mixing ratios.
Automotive Industries (AI) asked Sebastian Gries, Senior Sales Manager Automotive Gluing Systems Dürr Systems AG, how application technology affects battery lifespan.
Gries: Application technology plays a crucial role in ensuring the tightness of gasket seals and the proper functioning of the battery’s thermal management system. This extends battery lifespan by ensuring that the bonding and sealing of battery components are done with high precision and reliability.
AI: Does Dürr offer a complete solution for battery gluing application technology?
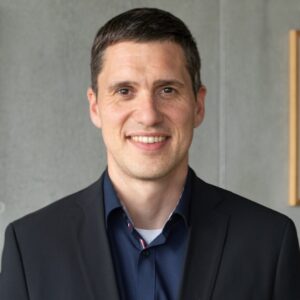
Gries: Dürr offers a wide-ranging portfolio to fulfil all battery production requirements, including various type of nozzles for different application patterns and modular shot meters for 1K, 2K and hotmelt.
AI: Does your modular system for the application of glues, sealants, and fillers in battery production ensure high quality, flexibility, and adaptability for various viscosities and mixing ratios?
Gries: Dürr’s gluing products are particularly robust and of high quality, capable of conveying dense, abrasive materials without damaging pumps and dispensers, thanks to stainless-steel material used and special coatings.
Furthermore, the system is flexible, accommodating different viscosities, materials, and processes (1K – 2K) with products designed for each specific material.
AI: Are you working on developing processes for the application of thermally conductive materials in thermal management?
Gries: We are currently working on a process called “Gapfiller-injection,” which fills cavities with gap filler as well as on dynamic-gapfiller application.
Gap filling uses thermal conductive adhesives (TCAs) or thermal interface materials (TIMs) that dissipate heat during battery charging and significantly impact temperature management. These gap fillers contain abrasive
materials that enhance thermal conductivity.
With dynamic-gapfiller application, the “gaps” that occur due to the tolerance of the components are measured per part, whereby the applied volume per part is dynamically adjusted by the adhesive control system.
AI: Is your technology suitable for small quantities in the laboratory, prototyping, pre-series, and large-volume processing in series production?
Gries: Yes, Dürr’s gluing technology supports different types of material supply – cartridges, buckets, drums – allowing for small-scale processing, prototype construction, pre-series, and large-scale series production.
AI: Do your test centers for battery gluing offer test procedures to ensure the smooth and optimized start of production?
Gries: Yes, Dürr offers test procedures at its battery gluing test centers to ensure a smooth and optimized production start in the battery factory.
By using simulation software, we can determine optimal adhesive consumption rates for newly developed battery prototypes, calculate cycle times, pressures, and volumes, and determine the best application patterns, reducing development time and
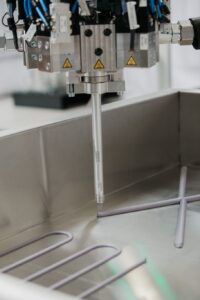
eliminating the need for complex test setups.
AI: Does your expertise cover every gluing and sealing process, including necessary pretreatment and cleaning?
Gries: Mostly yes. We also provide products for applying cleaners or primers.
AI: Is each gluing and dosing application individually tailored to customer requirements? Can the plant layouts be customized for different applications?
Gries: In battery gluing, we use a modular product kit based on a standardized system, allowing us to flexibly adapt to customer requirements and provide customized bonding systems. Dürr’s modular system covers all applications and can be flexibly customized to meet individual requirements, drawing on our extensive experience in body painting, body construction, and final assembly bonding.
Proven technologies are transferred to battery bonding to respond to new requirements in the best possible way. The portfolio includes the EcoRam material supply system, the EcoHVMP4 control system, the EcoShot Meter dosing units, and the EcoGun range of applicators.
AI: How does Dürr’s application technology ensure a reproducible process and consistent seam quality in battery systems?
Gries: Our piston shot meters combined with Dürr’s high-precision dosing controls system ensure high quality and continuous monitoring. This represents the most accurate dosing principle for reproducible processes and consistent seam quality.
AI: What new developments can we expect from Dürr, and how would they benefit the customers?
Gries: We recently introduced the EcoMeter SP, a continuous dosing system designed for the seamless application of highly viscous media without interrupting material flow. This product is well-suited for large-volume applications requiring substantial amounts of adhesives or sealants.
Powered by a screw spindle pump, the EcoMeter SP is lighter, more compact, requires less maintenance, and more cost-effective than previous alternatives. Its unlimited capacity makes it highly versatile, suitable for various applications in car manufacturing, including body-in-white construction, final assembly, and battery manufacturing.
In addition to offering endless dosing, the absence of a reverse piston stroke reduces cycle times and increases production capacity. Compared to tandem systems using two-piston dosing technology, a single spindle in the EcoMeter SP reduces the system’s overall weight by up to 20% and minimizes the required installation space.
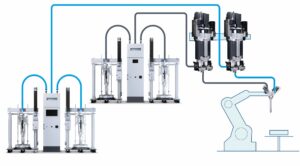
This makes the EcoMeter SP more agile and adaptable, allowing it to be integrated with smaller robot arms. Moreover, maintenance is less complicated with just one seal for material feed and the system uses less energy, resulting in up to 40% cost savings compared to tandem piston dosing systems.
Additionally, we are working on simulation tools like the “digital twin,” which simulates process sequences to shorten commissioning times and planning phases.
AI: How is Dürr responding to the constantly changing requirements for adhesives and application technology in the field of battery systems?
Gries: Dürr is adapting to the constantly evolving requirements for adhesives and application technology in the field of battery systems by leveraging its extensive experience in robot-guided application of paints, sealants, and adhesives.
The same technologies used in the body shop, paint shops, and in final assembly are now being applied to the bonding and sealing batteries. This expertise allows Dürr to react flexibly to the changing requirements of adhesives and application technology that come with each new generation of batteries.
AI: What makes Dürr unique in the field of battery gluing?
Gries: Dürr not only offers high-quality dispensing products but also provides extensive process expertise. We support our customer throughout the production lifecycle – from selecting the right components to process development, on-site support, and service— ensuring Dürr is a reliable partner for our customers.
AI: How is Dürr dealing with the issue of cycle time reduction in battery gluing?
Gries: Applications can be carried out using a single piston dispenser, but the drawback is that adhesive or sealant needs to be refilled after each process, which increases processing time.
To address this, Dürr utilizes continuous dosing in its modular system. This can be implemented in two ways: for two-component applications, two EcoShot Meters are combined into a tandem setup.
This eliminates the need for refilling, allowing cycle times to be maintained and reducing investment costs by consolidating tasks into a single work stage.
Instead of spreading the application across two or even three production or robot cells, it can now be completed in one cell, which requires less time. For single-component applications, the EcoMeter SP offers the same advantages.
It has the same weight as a single EcoShot Meter, ensuring that the robot payload for single-component continuous dosing remains the same.
More Stories
Sensor Fusion and the Next Generation of Autonomous Driving Systems
Unique Experiences in Miami: What to Do Off the Beaten Path
The Factors That Impact the Outcome of a Car Accident Claim